The manufacturing industry has long relied on innovative techniques to improve efficiency, precision, and overall product quality. Among these techniques, gravity die casting has played a pivotal role, offering a cost-effective and efficient way to produce intricate metal components. As technology continues to advance at a rapid pace, the future of aluminum gravity die-casting holds numerous opportunities for growth and innovation. This article delves into the evolving landscape of this essential manufacturing process, from aluminum gravity die-casting to revolutionary gravity die-cast machines.
Advancements And Opportunities In Gravity Die Casting
Advancements in Material Utilization
In the realm of gravity die casting, material utilization is a paramount consideration. Aluminum gravity die casting, in particular, has gained prominence due to its remarkable properties. Aluminum alloys offer high strength-to-weight ratios, corrosion resistance, and excellent thermal conductivity. Manufacturers are now exploring ways to optimize alloy compositions, leading to enhanced mechanical properties and performance. The future of aluminum gravity die casting involves harnessing these advancements to create lightweight and robust components catering to the automotive and aerospace industries.
Integration of Advanced Simulation Techniques
One of the most exciting developments in gravity die casting is the integration of advanced simulation techniques. Simulation software allows manufacturers to visualize and analyze the casting process before production begins. This enables engineers to identify potential defects, optimize gating and casting designs, and predict the final product’s quality. With the incorporation of artificial intelligence and machine learning, these simulations are becoming increasingly accurate, paving the way for enhanced precision and reduced wastage in aluminum gravity die casting.
Rise of Smart Gravity Die Cast Machines
The advent of Industry 4.0 has ushered in a new era of manufacturing, and gravity die casting is no exception. Smart gravity die-cast machines equipped with sensors, IoT connectivity, and real-time monitoring capabilities are revolutionizing the manufacturing landscape. These machines provide real-time insights into the casting process, enabling operators to make instantaneous adjustments for optimal results. Additionally, predictive maintenance algorithms help prevent downtime by identifying potential machine failures before they occur.
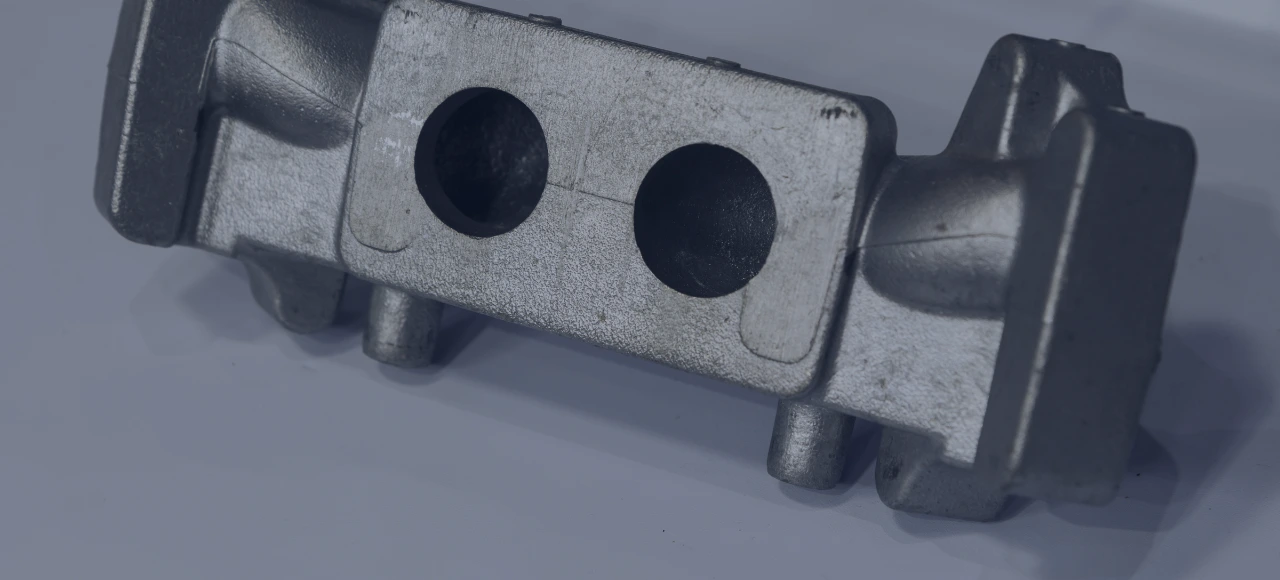
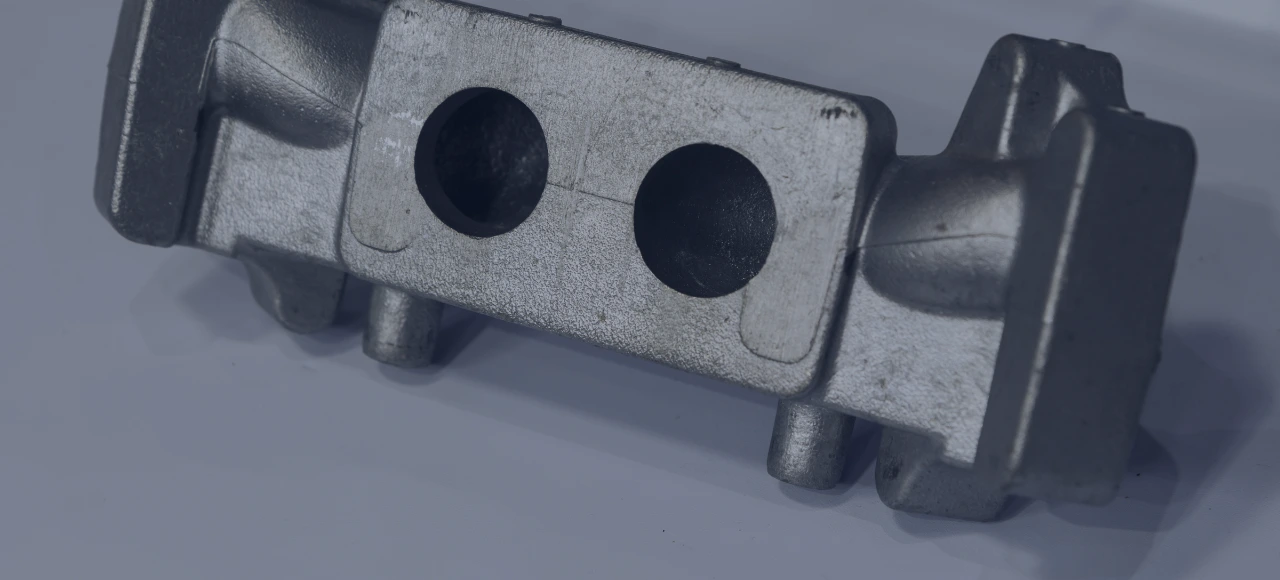
Sustainable Practices and Environmental Impact
As sustainability gains prominence across industries, gravity die casting is also evolving to meet environmentally conscious standards. Manufacturers are exploring eco-friendly die lubricants and cooling fluids that reduce waste and minimize the environmental impact. Moreover, improved energy efficiency in gravity die-cast machines contributes to lowering carbon footprints during the production process. The future of gravity die casting is undoubtedly aligned with sustainable practices that prioritize both product quality and environmental responsibility.
Global Collaboration and Knowledge Sharing
The digital age has enabled global collaboration and knowledge sharing like never before. Manufacturers, engineers, and researchers from different parts of the world can now connect, exchange ideas, and collectively drive innovation in gravity die casting. Online platforms and forums dedicated to manufacturing processes facilitate discussions on best practices, challenges, and emerging trends. This interconnectedness fosters a rich ecosystem of expertise, propelling the future of gravity die-casting forward.
Shaping Tomorrow’s Gravity Die Casting Manufacturing With Zetwerk
In the ever-evolving manufacturing landscape, gravity die casting stands as a cornerstone of efficiency and precision. With advancements such as aluminum gravity die casting, smart machines, and simulation-driven optimization, the future of this technique is indeed promising. As industries continue to demand lighter, stronger, and more intricate components, gravity die casting will play an instrumental role in meeting these demands. The ongoing pursuit of sustainable practices and global collaboration ensures that gravity die-casting remains at the forefront of manufacturing innovation.
Zetwerk is a leading platform that empowers manufacturing processes, fostering innovation and collaboration in the industry. For more information on gravity die casting and related services, visit Zetwerk page.




FAQs
Gravity die casting is a manufacturing process that involves pouring molten metal into a reusable mold under the force of gravity. It is widely used to produce complex metal components efficiently.
Aluminum gravity die casting offers high strength-to-weight ratios, corrosion resistance, and thermal conductivity. It is ideal for producing lightweight yet robust components.
Simulation software allows manufacturers to predict and optimize the casting process, reducing defects and enhancing product quality.
Smart machines equipped with sensors and real-time monitoring capabilities provide insights for real-time adjustments and predictive maintenance, improving efficiency and reducing downtime.
Manufacturers are adopting eco-friendly lubricants, cooling fluids, and energy-efficient practices to minimize waste and environmental impact.