MAXIMIZE MANUFACTURING
With an unbreakable supply chain and virtually unlimited manufacturing capacity, Zetwerk is your solution for getting the components you need when you need them.
MANUFACTURING PROCESSES
Explore manufacturing capabilities that support a wide range of applications and processes.
MANUFACTURING FOR INDUSTRIES
Explore a full spectrum of solutions across industries.
About Zetwerk
Zetwerk offers high-quality production, globally competitive costs and unparalleled lead times in the manufacturing of capital goods, consumer goods and precision parts.
UP TO 50%
REDUCTION IN LEAD TIMES
Zetwerk offers transparent tracking and timely delivery for customers.
9 MILLION+
NUMBER OF PARTS MANUFACTURED
Zetwerk provides unmatched manufacturing capabilities for all industries.
1800+
ACTIVE CUSTOMERS
Zetwerk’s manufacturing network caters to clients across the globe.
20+
COUNTRIES ZETWERK DELIVERS TO
Zetwerk’s manufacturing network caters to clients across the globe.
UNBREAKABLE SUPPLY CHAIN
Zetwerk’s global supply chain management has built-in redundancies, so typical production issues never become your problem.
Zetwerk is your local supplier no matter where in the world you manufacture your product.AVOIDING BUSINESS DISRUPTION
Zetwerk Managed Inventory provides Just in time deliveries in less than 5 days, regardless of where your components are manufactured.
ZMI makes months-long lead times a thing of the past.PROVEN TECHNOLOGY
Zetwerk’s in-house Manufacturing Operating System software includes proprietary tools, technology, and teams for project management, offering automation, transparency, and quality across manufacturing operations.
UNLIMITED MANUFACTURING CAPACITY
Zetwerk has the capacity to double production needs overnight regardless of product, specification, scale, or geography. Its partner facilities and worldwide supplier base enable scaling up and down production with a quick turnaround time.
“Our Partnership with Zetwerk has helped us focus on our side of the business while they take end-to-end ownership of our manufacturing needs.”
HITACHI
Partners and Customers
Zetwerk partners with companies of all sizes ranging between SMBs and Fortune 500 companies in markets such as North America, Southeast Asia, Australia, New Zealand, and the Middle East.
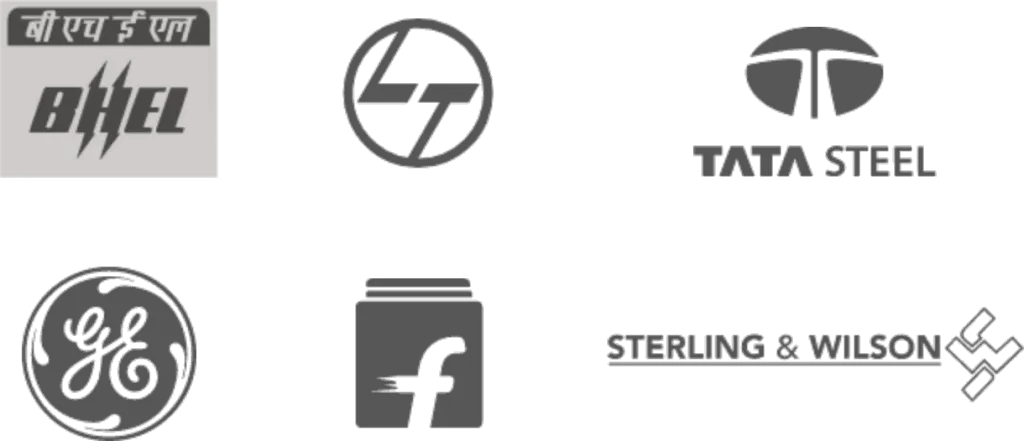
Our Capabilities
With our worldwide network of owned, operated, and partner manufacturing plants, we can have components built to your specification at your doorstep with industry-best lead times. These are just a few of Zetwerk’s manufacturing capabilities.
Zetwerk provides high-quality die-cast components produced using a range of materials including aluminum, zinc, copper, brass, and bronze alloys. Once a component has been die-cast, it can be further refined with CNC machining. Surface finishes are commonly applied through processes like shot-blasting, texturing, plating, and painting.
Zetwerk offers a variety of forging types, including drop forging, hot/cold forging, rolled ring forging, and press forging. We provide forged parts using lower-alloy and carbon steels, as well as alloys of aluminum, brass, and bronze. Once forged, components can be post-processed by precision CNC machining and surface finishing.
Injection molding can produce parts in a wide range of sizes and complexity. Small features, intricate geometries, and thin walls can be captured with ease using the injection molding process. Injection-molded components can be post-processed via various surface finishing options such as painting and texturing.
Zetwerk produces custom sheet metal stampings in a wide range of custom materials. Some of the materials include cold-rolled steel (CRS), hot-rolled steel, stainless steel, galvanized, brass, aluminum, and beryllium copper among others. We offer complete secondary operations including powder coating, painting, anodizing, silk screening, and pad printing. Assembly services are also available.
Zetwerk produces investment cast components using carbon steel, low-alloy steel, and stainless steel grades, in addition to a wide variety of non-ferrous metals such as aluminum, brass, and bronze. We also perform necessary secondary operations on the cast parts such as finish machining, heat treatment, and surface treatment.
Industries
Zetwerk is a manufacturing services provider that offers virtually unlimited manufacturing capacity and a wide range of capabilities. Regardless of your industry, from aircraft engines, or medical equipment to mining, we offer best-in-class precision manufacturing solutions alongside manufacturing services that improve quality and reduce lead times.
QUALITY CERTIFICATIONS
Quality is at the core of Zetwerk’s global manufacturing network. Be it systems, people, processes or technology, everything moves in one gear to deliver 100% certified quality for every project and every customer.
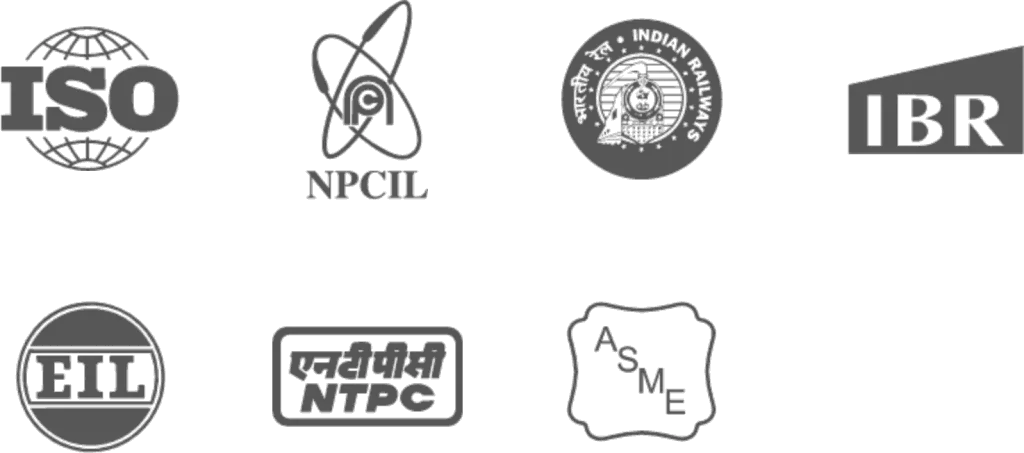
The Zetwerk Effect
Zetwerk helps our customers reduce the costs of existing and new production parts, while maximizing efficiency, quality, and value. Learn how Zetwerk’s advanced project management techniques and virtually unlimited manufacturing quality can help you maximize manufacturing.