Modern electronics factories are the powerhouses behind the devices we rely on daily. From smartphones to industrial automation systems, the journey from concept to completion involves cutting-edge technology, intricate processes, and precise execution. This blog takes you inside an electronics factory to explore how innovative ideas transform into market-ready products.
Step 1: Ideation and Design
The journey begins with a concept. This stage involves brainstorming, feasibility analysis, and design engineering. Electronics factories collaborate with product designers and Original Equipment Manufacturers (OEMs) to:
- Develop detailed schematics and PCB layouts.
- Evaluate materials and components for cost and functionality.
- Ensure designs meet regulatory and industry standards.
Using advanced CAD tools, engineers simulate performance and optimize designs before production begins.
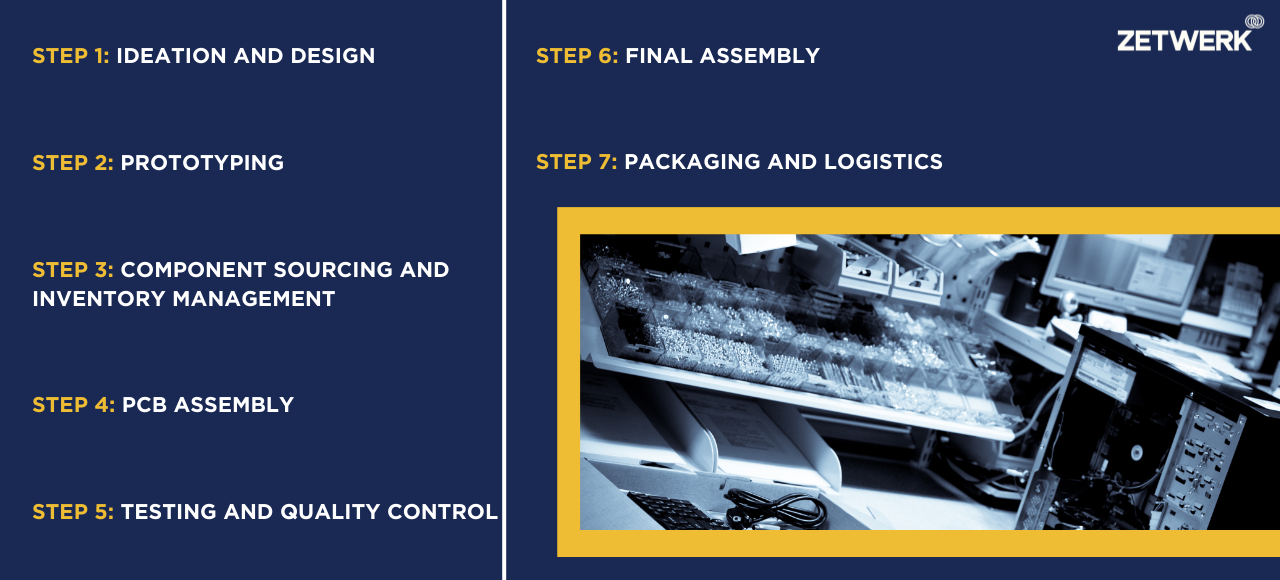
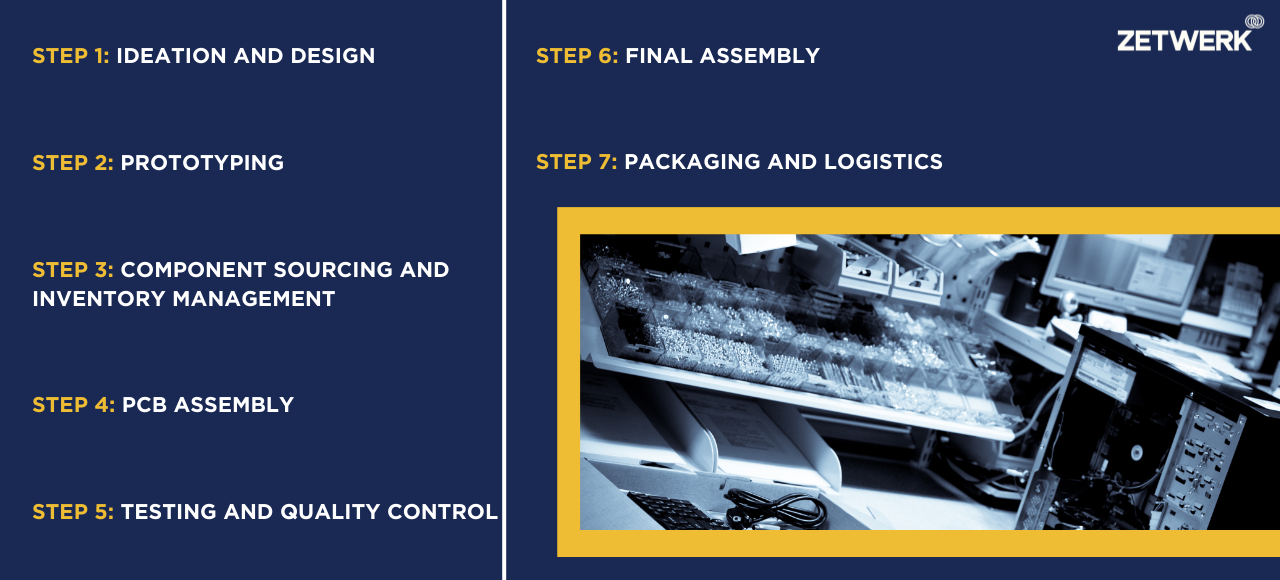
Step 2: Prototyping
Prototyping is where ideas take tangible form. Factories employ rapid prototyping techniques to create initial models. This process allows for:
- Testing product functionality and resolving design flaws.
- Gathering client feedback for improvements.
- Accelerating the transition to production.
Technologies like 3D printing and automated soldering machines enhance speed and accuracy during prototyping.
Step 3: Component Sourcing and Inventory Management
Component sourcing is critical to maintaining quality and timelines. Electronics factories rely on extensive supplier networks to procure certified components. Key considerations include:
- Quality Assurance: Ensuring components meet stringent standards.
- Supply Chain Optimization: Minimizing lead times and costs.
- Inventory Management: Balancing stock levels to prevent delays without overstocking.
Factories often integrate ERP systems to monitor inventory and streamline procurement.
Step 4: PCB Assembly
At the heart of every electronic device is the printed circuit board (PCB). PCB assembly is a meticulous process involving:
- Solder Paste Application: Applying solder paste to PCB pads where components will be placed.
- Pick-and-Place Machines: Automated machines position components with precision.
- Reflow Soldering: Heating the board to solidify the solder paste and secure components.
- Inspection: Visual and automated inspections detect soldering defects and misaligned components.
Surface-mount technology (SMT) and through-hole technology (THT) are commonly used for PCB assembly, depending on the product’s complexity.
Step 5: Testing and Quality Control
Quality is non-negotiable in electronics manufacturing. Factories employ rigorous testing protocols, including:
- In-Circuit Testing (ICT): Verifies electrical performance and connectivity.
- Functional Testing: Simulates real-world usage to ensure functionality.
- Environmental Testing: Subjects products to temperature, humidity, and vibration tests to confirm durability.
- Compliance Testing: Ensures adherence to industry certifications like ISO, CE, and UL.
Quality control teams continuously monitor processes to maintain high standards.
Step 6: Final Assembly
Once PCBs pass testing, they are integrated into the final product. This stage involves:
- Assembling enclosures and mechanical parts.
- Adding features like displays, connectors, and user interfaces.
- Conducting end-of-line testing to ensure the product meets specifications.
Skilled technicians and automated systems work in tandem to ensure efficiency and accuracy during assembly.
Step 7: Packaging and Logistics
The final step is preparing products for the market. Factories manage:
- Custom Packaging: Designing packaging that protects products during transit and enhances brand presentation.
- Labeling: Adding regulatory labels, barcodes, and instructions.
- Logistics: Coordinating with global shipping providers to ensure timely delivery.
Advanced logistics systems enable real-time tracking and efficient distribution across multiple locations.
The Role of Automation in Modern Electronics Factories
Automation has revolutionized electronics manufacturing. Robots, AI-driven systems, and IoT-enabled devices enhance every aspect of production by:
- Reducing errors and improving precision.
- Increasing production speed and scalability.
- Enabling predictive maintenance for equipment.
- Enhancing data analysis for better decision-making.
Sustainability in Electronics Manufacturing
Sustainability is gaining prominence in the industry. Factories adopt eco-friendly practices such as:
- Using recyclable materials and reducing waste.
- Implementing energy-efficient production methods.
- Adhering to RoHS (Restriction of Hazardous Substances) guidelines.
These efforts not only protect the environment but also meet the expectations of socially conscious customers.
Challenges in Electronics Manufacturing
Despite advancements, challenges persist in electronics factories, including:
- Component Shortages: Supply chain disruptions can delay production.
- Technological Complexity: Advanced products require continuous skill development and investment in new equipment.
- Regulatory Compliance: Navigating global regulations demands meticulous documentation and testing.
- Cost Pressures: Balancing affordability and quality remains a key challenge.
Future Trends in Electronics Manufacturing
The future of electronics manufacturing is shaped by:
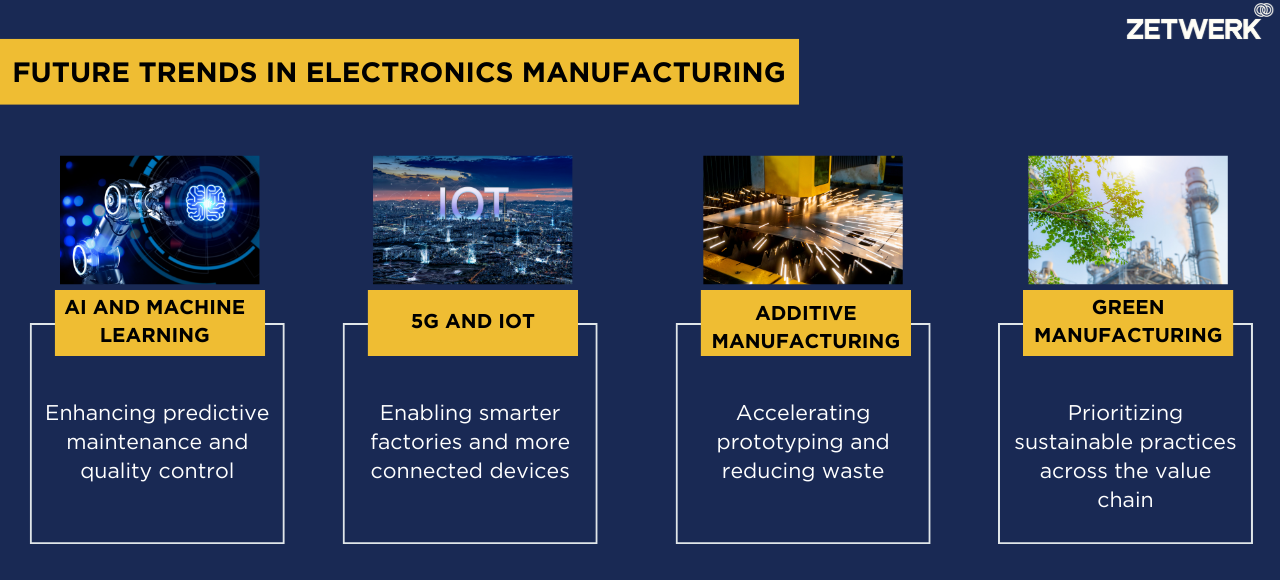
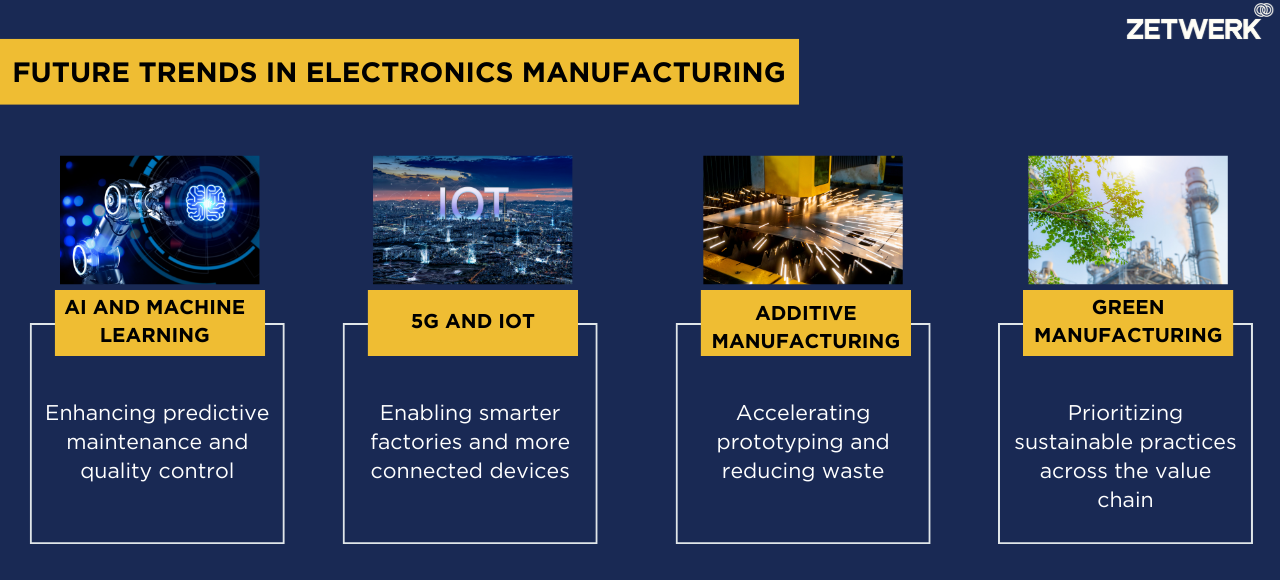
- AI and Machine Learning: Enhancing predictive maintenance and quality control.
- 5G and IoT: Enabling smarter factories and more connected devices.
- Additive Manufacturing: Accelerating prototyping and reducing waste.
- Green Manufacturing: Prioritizing sustainable practices across the value chain.
Conclusion
Electronics factories are at the forefront of technological innovation, transforming concepts into high-performance products. From meticulous design to precision assembly, every stage is optimized for efficiency, quality, and customer satisfaction.
Zetwerk Electronics stands as a reliable partner in this space, offering end-to-end solutions tailored to your needs. With a focus on quality, sustainability, and on-time delivery, Zetwerk ensures that your ideas are transformed into reality seamlessly.



FAQs
A. Electronics factories use comprehensive quality control measures, including automated inspections, functional testing, and compliance checks. They also implement rigorous testing at each stage, from component sourcing to final assembly, ensuring high-quality standards.
A. Automation enhances precision, reduces errors, and improves production speed. From pick-and-place machines in PCB assembly to AI-driven quality control systems, automation is integral to modern electronics manufacturing.
A. Factories mitigate supply chain risks by diversifying supplier networks, maintaining strategic inventory levels, and leveraging advanced ERP systems for real-time monitoring and management.
Contact Us
Contact us today to discuss your project requirements and discover how we can help you achieve your goals efficiently and effectively.