Forged rings are metal rings that are made from a forging process. Forging is a manufacturing process that shapes metal by hammering, pressing, or rolling hot metal while it is in a molten state. Forged rings are stronger and more durable than those made by other manufacturing processes. They are used in a wide range of industries including aerospace, automotive, and oil and gas. They are often used in applications where strength, durability, and reliability are critical, such as in high-pressure valves, gears, and bearings. Forging rings come in a variety of materials and sizes. They can be made from carbon steel, alloy steel and stainless steel. They are used for manufacturing precision tools, heavy machinery and other products.
Zetwerk, forging components manufacturer, provides high-quality parts and all secondary operations.
Submit the relevant part drawings, 3D files, and other information by clicking on the button below.





Forging and Its Methods
The process of using concentrated compressive forces to shape metals is called forging. The forging block is used to push and shape metal in a forge. Forging blocks are utilized for forging heavy metal, filigree materials like gold, and other metals. Forging works that are extremely precise and dimensionally accurate in the customer’s order are built on the precision of the forging block in shape, size, and weight. Therefore, attention is given to the selection, purity, condition, and shaping process throughout the production of forging blocks.
Metal blocks can be shaped using the industrial block forging technique into desired shapes, much like how a forged component is made. The metal is formed into the required shape by repeatedly striking a heated metal block with a hammer. Drop forging is used to describe this method, as the metal block is molded by being hit with a raised and then dropped the hammer.
- Open Die Forging: Open die forging is a process used to shape heated metal pieces. A top die is attached to a ram, and a bottom die is attached to a hammer, anvil, or bolster used in this process.
- Closed Die Forging: Finished Die Forging is a forging technique in which the dies move toward one another and partially or completely enclose the workpiece. The bottom die is filled with molten material that has been heated, and it is about the size or shape of the finished forged object.
The manufacturing process in Open Die Forging
In open die forging, a piece of metal is shaped between two or more dies that do not entirely enclose it. In order to create the desired shape, the material is “hammered” through a sequence of movements by the dies. Open-forging products frequently need additional machining and refinement to obtain the tolerances required for the finished standards. Open die forging is frequently used for small batches, simple as opposed to complex products like rings and discs.
Open die forging also enables the production of custom shapes since it maximizes grain flow during deformation, enhancing the strength of the underlying grain structure. A further advantage of open die forging is the improvement of fatigue resistance and strength due to producing a finer grain structure instead of catastrophic collapse (such as shrink fitting). Additionally, by repeatedly working on each billet during the rolling or extrusion process, voids can be successfully eliminated after opening die forging.
The manufacturing process in Closed Die Forging
A metal piece is compressed under intense pressure during the closed-die forging process to fill the impression left by the enclosed die. A second forging procedure is necessary to produce the final shapes and dimensions for particular shapes and unique materials. The kind of material, the degree of tolerance, and if heat treatment is required can all affect the price of closed-die forged parts
Few Types of Forging Process
- Hand forging – a hammer hits the metal and gives it shape.
- Machine forging – such as a pressing or rolling machine, is used to strike the metal into the required shape.
- Drop forging – A hot metal is struck with drop hammers at the bottom dye during drop forging, and the dye’s shape is transferred to the hot metal. Drop forging creates wrenches and other common objects by heating iron in a furnace and then molding it into the desired shapes.





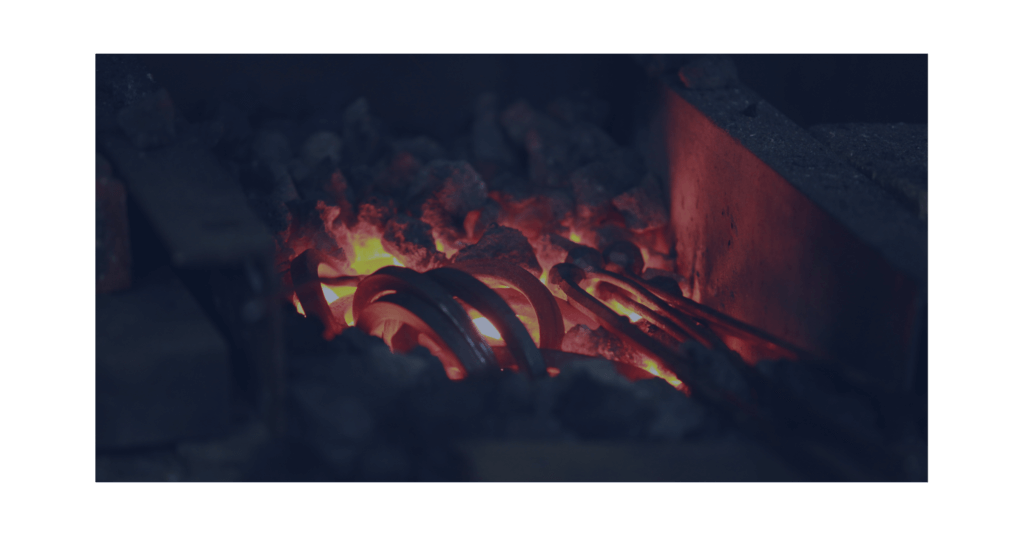
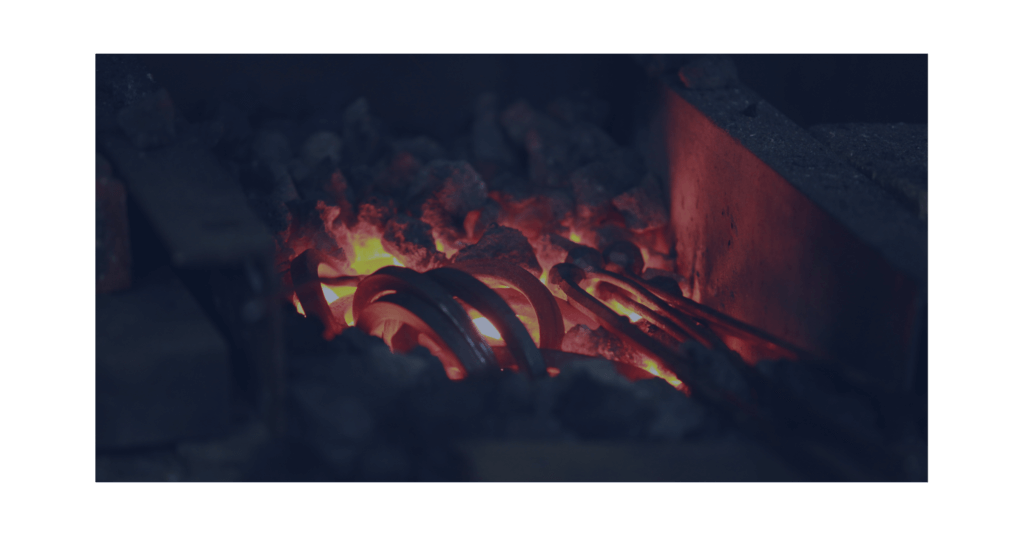
Benefits of Custom Forging
Custom steel forgings are highly reliable and offer excellent tolerance capabilities. Their consistency in composition and structure makes them ideal for use in applications where quality is paramount. Additionally, forgings generated from a single “hot” material are stronger than machined or cast items due to grain flow strengthening. This makes custom steel forgings the ideal choice when strength is crucial.
Applications of Forging
- Forged components are commonly used in the automotive and trucking industries because of their strength, dependability, and economy. They are often used in high-stress areas such as wheel spindles, kingpins, axle beams and shafts, torsion bars, ball studs, idler arms, and steering arms. Forged components are also frequently used in the powertrain, where they are made into connecting rods, transmission shafts, gears, and differential gears.
- Aerospace forgings are essential to jet turbine engines, helicopters, piston-engine planes, military aircraft, and spacecraft. Depending on the project’s needs, they can be made of different ferrous, non-ferrous, and special alloy materials. Bulkheads, wing roots and spars, hinges, engine mounts, brackets, beams, shafts, landing gear cylinders, and struts are a few examples of where a forging’s size, shape, and qualities make it an ideal component.
- Generic equipment used by industries: Enormous forges are used by a variety of industries, including steel, textile, paper, power generation, and transmission, chemical, and refinery, to create bars, blanks (or rods), blocks ( discs), connecting rods, cylinders (or shafts), elbows (or T’s), rings (or sleeves), and other components.
Forged Rings uses in Automotive Industry
A ready-made base plate from a steel producer is what is known as a “forged ring”. To fit the base plate’s required dimensions, it is hot-rolled and shaped into a ring shape. Forged rings are a great place to start with many machining jobs. The automobile sector uses forge rings. As a result, the engine and transmission are put under less stress. They are employed to help reduce weight and boost strength. In addition, clutches, braking systems, and camshafts all require forge rings. The forged rings application is mainly used in the application of braking systems.
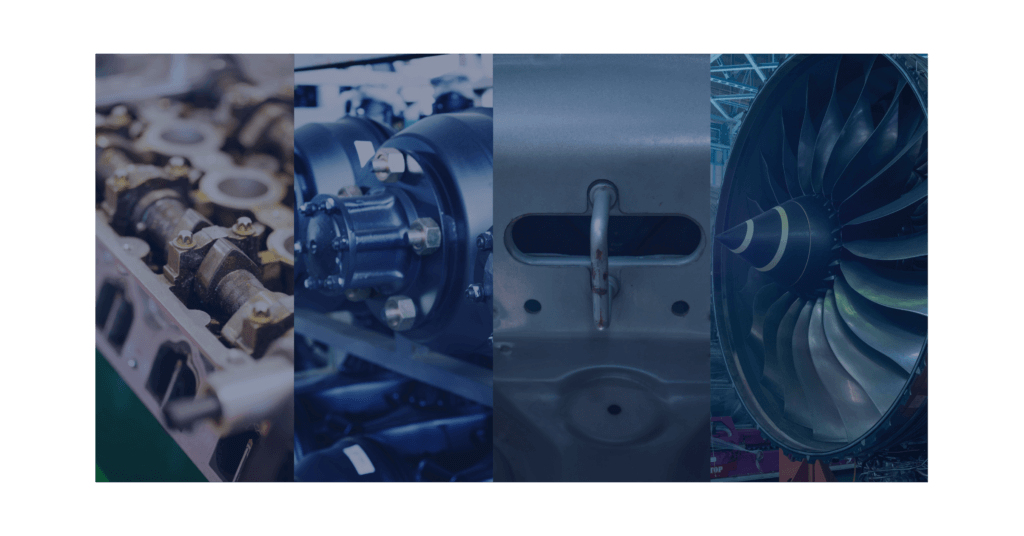
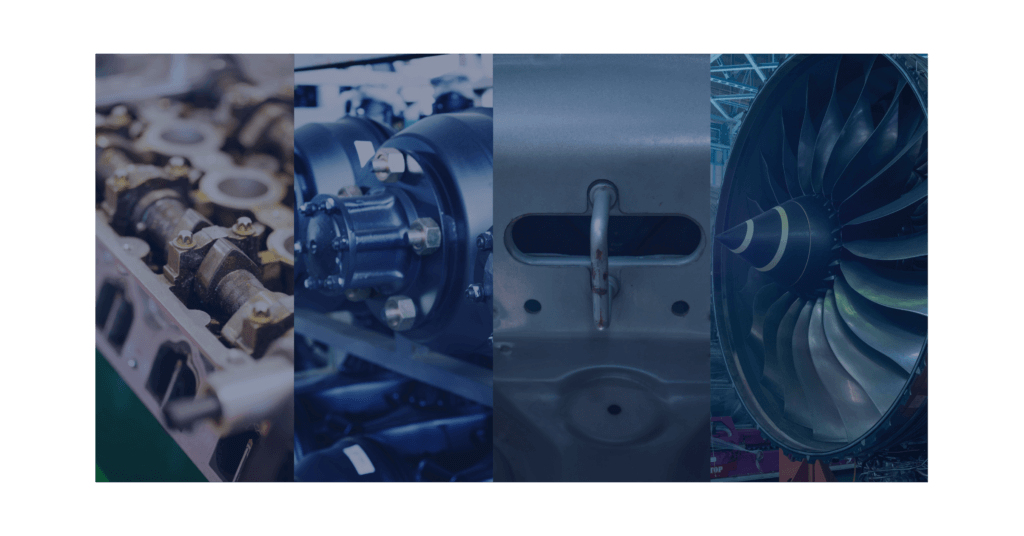
At Zetwerk, we specialize in forged rings, forms, step and crankshafts, hollows, hubs, tooled forgings, semi-closed die forgings, and bars. We can produce components with weights ranging from a few pounds in various ferrous and non-ferrous materials, including titanium, nickel, stainless steel, carbon alloy steel, and aluminum. We serve the industries of shipbuilding, power generation, oil and gas, semiconductor gear manufacturing, aerospace defense, and metal service centers.




