The Future of Aerospace Components : How Casting Methods are Transforming Design and Performance
Aerospace manufacturing is a challenging area that necessitates the creation of complicated, high-performance components. Aerospace manufacturing companies increasingly employ casting techniques to make high-performance components with intricate geometries and forms to satisfy these demands. Casting is a manufacturing technique involving pouring molten metal into a mold, where it solidifies. This method has various advantages over other manufacturing techniques, particularly when it comes to the production of intricate designs. For instance, casting techniques enable manufacturers to construct intricately shaped components, such as hollow holes or internal channels, that would be difficult or impossible to fabricate using other methods.
One of the primary advantages of casting is the capacity to make high-strength, complex-shaped components that are lighter and more efficient than those produced by other processes. This is because casting technologies enable manufacturers to build shapes optimized for strength while minimizing the amount of raw material required to produce a component. This produces a more robust, lighter part that can survive the arduous conditions of flight. Another advantage of casting processes is the ability to produce uniform and durable components. This is because casting molds can be meticulously planned and made to ensure that each object produced has uniform forms and dimensions. In addition, casting techniques enable manufacturers to manage the grain structure of the metal, which can enhance the component’s strength and durability.
Despite the numerous advantages of casting processes, manufacturing complicated designs in the aerospace industry requires overcoming a number of obstacles. Casting techniques, for instance, can be time-consuming and need specific equipment and knowledge. In addition, casting procedures frequently result in longer lead times than other manufacturing techniques, which can be problematic for producers attempting to meet delivery deadlines or adapt to changing client demands.
Aerospace manufacturers are turning to innovative casting technologies and materials that offer greater performance and efficiency to address these obstacles. Manufacturers use sophisticated computer-aided design (CAD) tools and simulation software, for instance, to optimize casting molds and anticipate the performance of cast components. This enables manufacturers to discover possible problems early in the design phase and make revisions before production, hence reducing the time and expense involved with casting.
Another trend in aerospace casting is utilizing new materials to enhance performance and efficiency. Manufacturers use, for instance, sophisticated alloys with improved strength-to-weight ratios, enhanced thermal characteristics, and enhanced corrosion resistance. These cutting-edge materials enable manufacturers to create high-performance components that are more dependable and effective than ever before.
Casting techniques are gaining importance in the aerospace industry, allowing manufacturers to create complicated components with stringent performance specifications. Aerospace manufacturers are overcoming the obstacles associated with sophisticated designs by utilizing modern casting technologies and materials to produce high-performance components that are lighter, stronger, and more efficient than ever before. As the aerospace industry continues to develop, casting techniques will play an increasingly vital role in addressing the demand for high-performance, complex-shaped, and -geometric components.
The Key Factors in Choosing Materials for Aerospace Casting
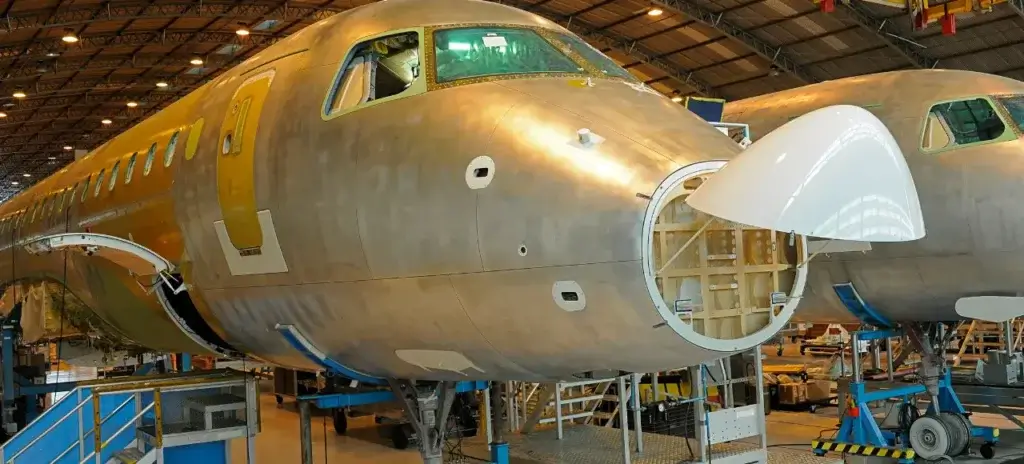
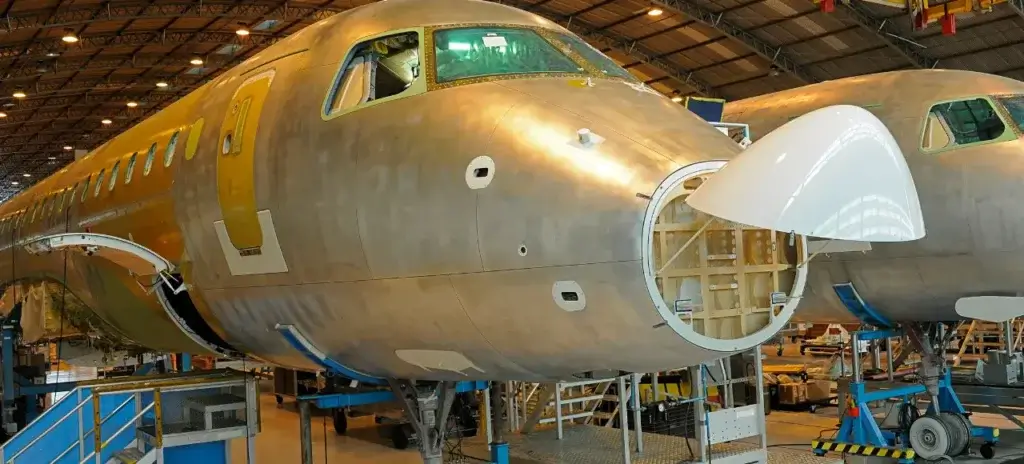
The aerospace industry requires the highest level of performance from its components, and the materials used in aerospace casting are essential to attaining these requirements. Aerospace castings must be lightweight, strong, heat-resistant, and long-lasting, whether for commercial airliners, military aircraft, or spacecraft. Manufacturers must carefully evaluate many material selection variables to produce high-quality castings that fulfill these specifications. Consider the following variables when selecting materials for aerospace castings:
- Strength-to-Weight Ratio: Aerospace castings must be strong enough to endure harsh flight conditions and light enough to reduce fuel consumption and enhance performance. This entails selecting materials with the best ratio of strength to weight.
- Thermal Properties: Castings for the aerospace industry must be able to endure high temperatures without deforming or weakening. This necessitates selecting materials with superior thermal stability and thermal shock resistance.
- Cost: Cost is a factor in all manufacturing processes, including the aerospace sector. When selecting materials, producers must carefully balance cost and performance.
- Manufacturability: In addition to meeting performance specifications, aerospace casting materials must be appropriate for the casting process. Casting temperature, moldability, and machining ease can influence the selection of materials.
- Corrosion Resistance: Aerospace castings are frequently subjected to hostile environments, such as high quantities of moisture, corrosive chemicals, and extreme temperatures. Choosing corrosion-resistant materials can increase the durability and performance of casting over time.
Selecting acceptable materials for aerospace castings is complex and requires careful consideration of numerous criteria. By taking the time to consider all of these elements, producers are able to develop high-quality, high-performance castings that satisfy the stringent requirements of the aerospace industry.
As a manufacturer, Zetwerk can assist you with your unique project by linking you with dependable aerospace casting manufacturers. The casting choices available on Zetwerk’s platform include sand casting, investment casting, and die casting. Their manufacturers are certified to fulfill rigorous aircraft quality standards and have extensive expertise working with complicated alloys and close tolerances. You can effortlessly manage your entire project with Zetwerk, from sourcing through delivery, with access to real-time updates and quality checks. Overall, Zetwerk can provide an efficient and dependable solution for your aerospace casting requirements.



