Globally, the aluminum casting manufacturing market has witnessed significant growth in the past few years. The driving force behind the development of this market is attributed to the increased application of aluminum in numerous industries and rising disposable income in developing regions. The leading aluminum companies focus on innovations and strategic business expansions to gain a competitive edge.
History & Manufacturing Process of Cast Aluminum
The history of cast aluminum dates back to ancient times when aluminum was first used in various applications. However, the production of aluminum as a pure metal was only possible in the 19th century when it was isolated through the electrolysis of aluminum oxide (alumina).
Aluminum is hardened by melting it and pouring it into a mold. It solidifies and takes on the shape of the mold. There are several methods for casting aluminum, including sand casting, die casting, and permanent mold casting.
Sand casting is a traditional method of casting aluminum using a mold made from sand. The aluminum is melted and poured into the mold, where it solidifies and takes on its shape. Sand casting is relatively simple and inexpensive, but it is unsuitable for producing high-precision parts.
The die casting process is a more precise method of casting aluminum that uses high pressures and temperatures to inject molten metal into a mold. This process produces parts with high dimensional accuracy, a smooth surface finish, and very little porosity.
Permanent mold casting is similar to die casting, but the mold is made from a durable material such as steel or cast iron. This process is suitable for producing parts with high precision and a smooth surface finish.
Today, aluminum is widely used in many industries, including automotive, aerospace, construction, and consumer products. It’s strong enough to be used in structural applications and lights sufficient in manufacturing. Also, its corrosion resistance makes it ideal for many different applications.





Why Does The Demand For Aluminum Increase?
The demand for aluminum has grown significantly over the past few decades due to its desirable properties and versatility in various applications. Some of the factors that have contributed to the increased demand for aluminum include:
- Lightweight: Aluminum is about one-third the weight of steel, making it an ideal material for use in the automotive and aerospace industries, where weight reduction is essential.
- Strength: Despite its lightweight nature, aluminum is also strong and durable, making it suitable for various structural applications.
- Corrosion resistance: Aluminum is resistant to corrosion, making it an ideal material for use in outdoor and marine applications.
- Conductivity: Aluminum has high electrical and thermal conductivity, making it an essential material in the electrical and electronics industries.
- Recyclability: Aluminum can be recycled indefinitely without losing its properties, making it an environmentally friendly material.
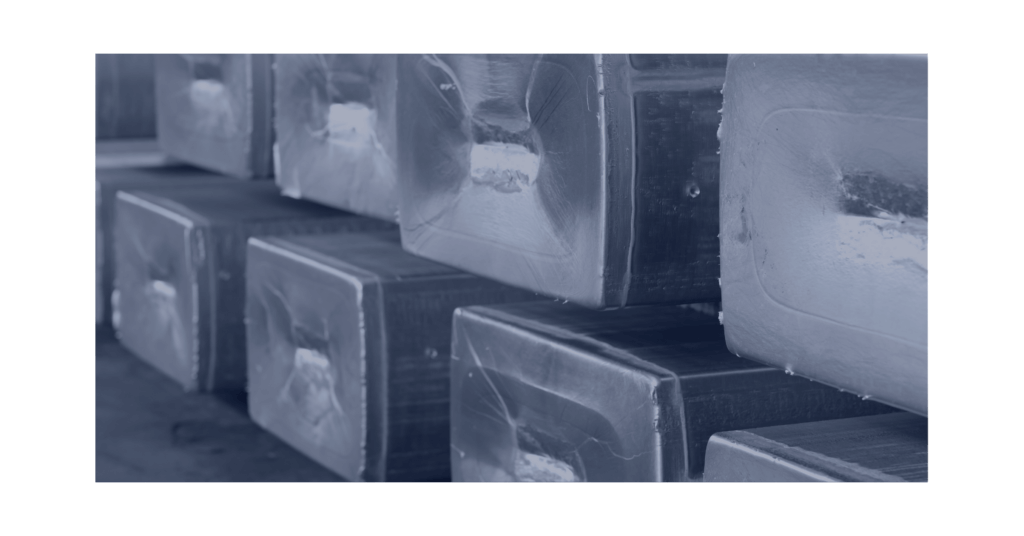
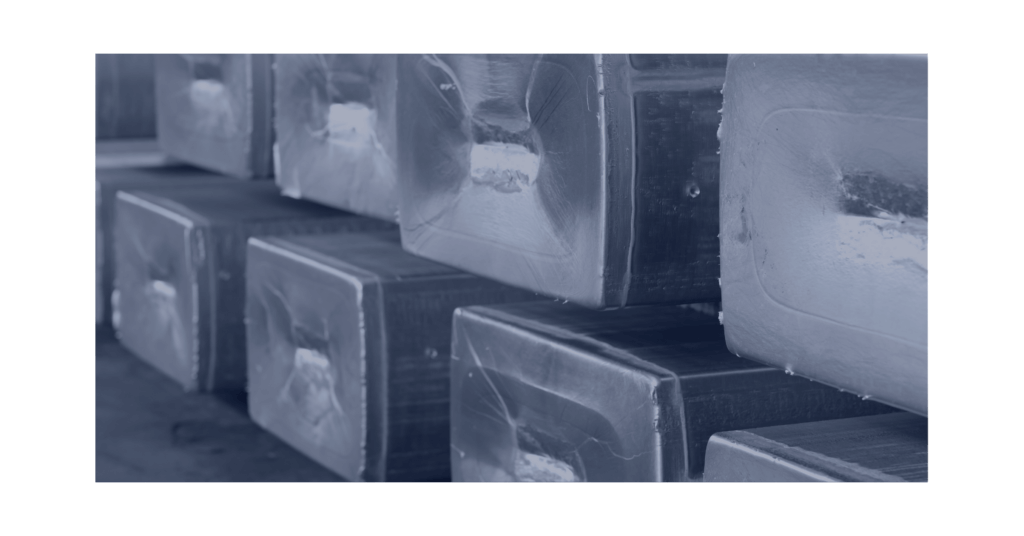
In addition, the increasing demand for aluminum in emerging economies such as China and India has contributed to the growing demand for the metal. As a result, the global aluminum industry has grown significantly over the past few decades, with aluminum now being one of the most widely used metals in the world.
Aluminum’s Many Uses
Aluminum is a versatile and widely used material with a wide range of applications in various industries. Some of the many uses of aluminum include:
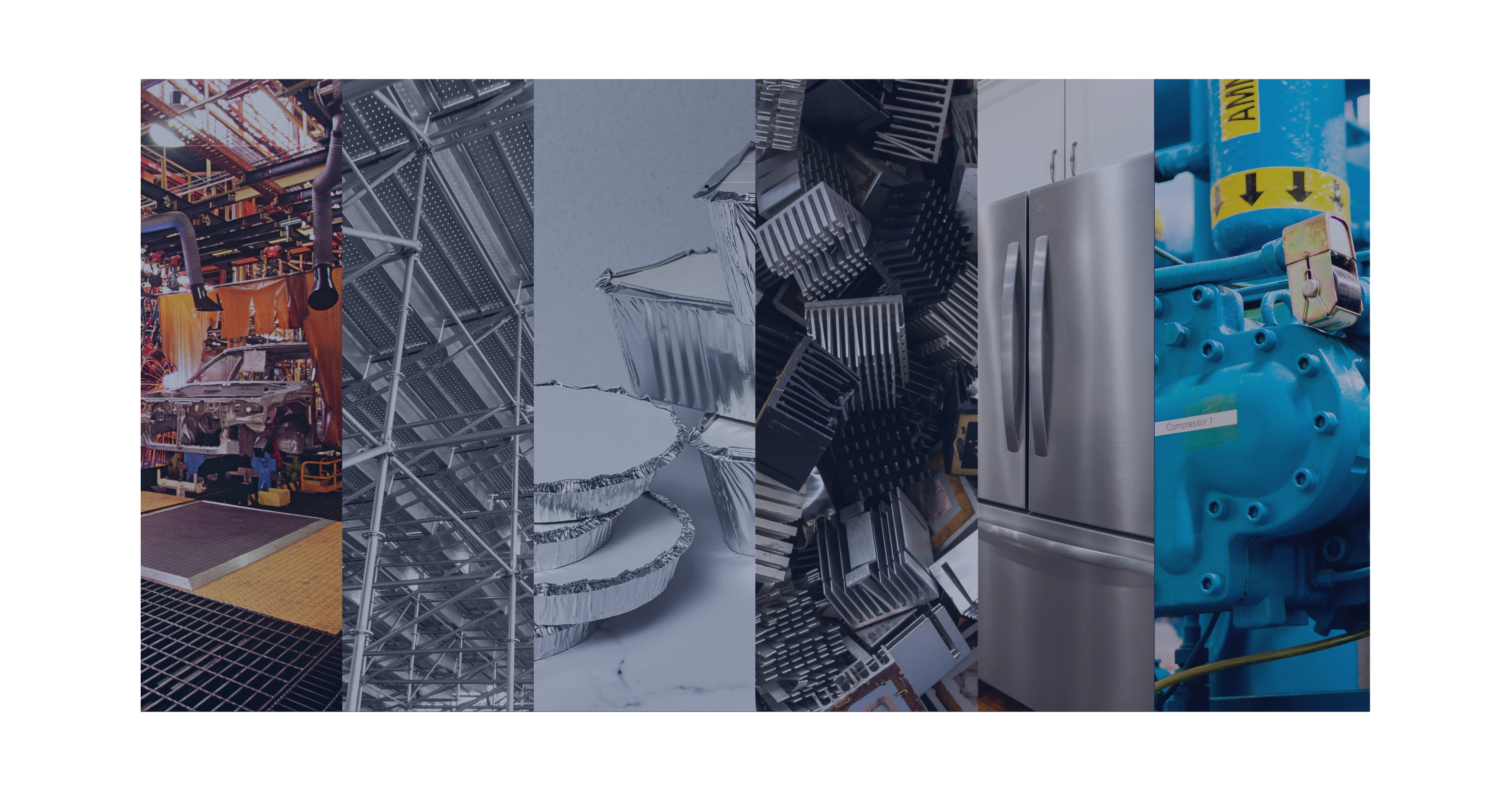
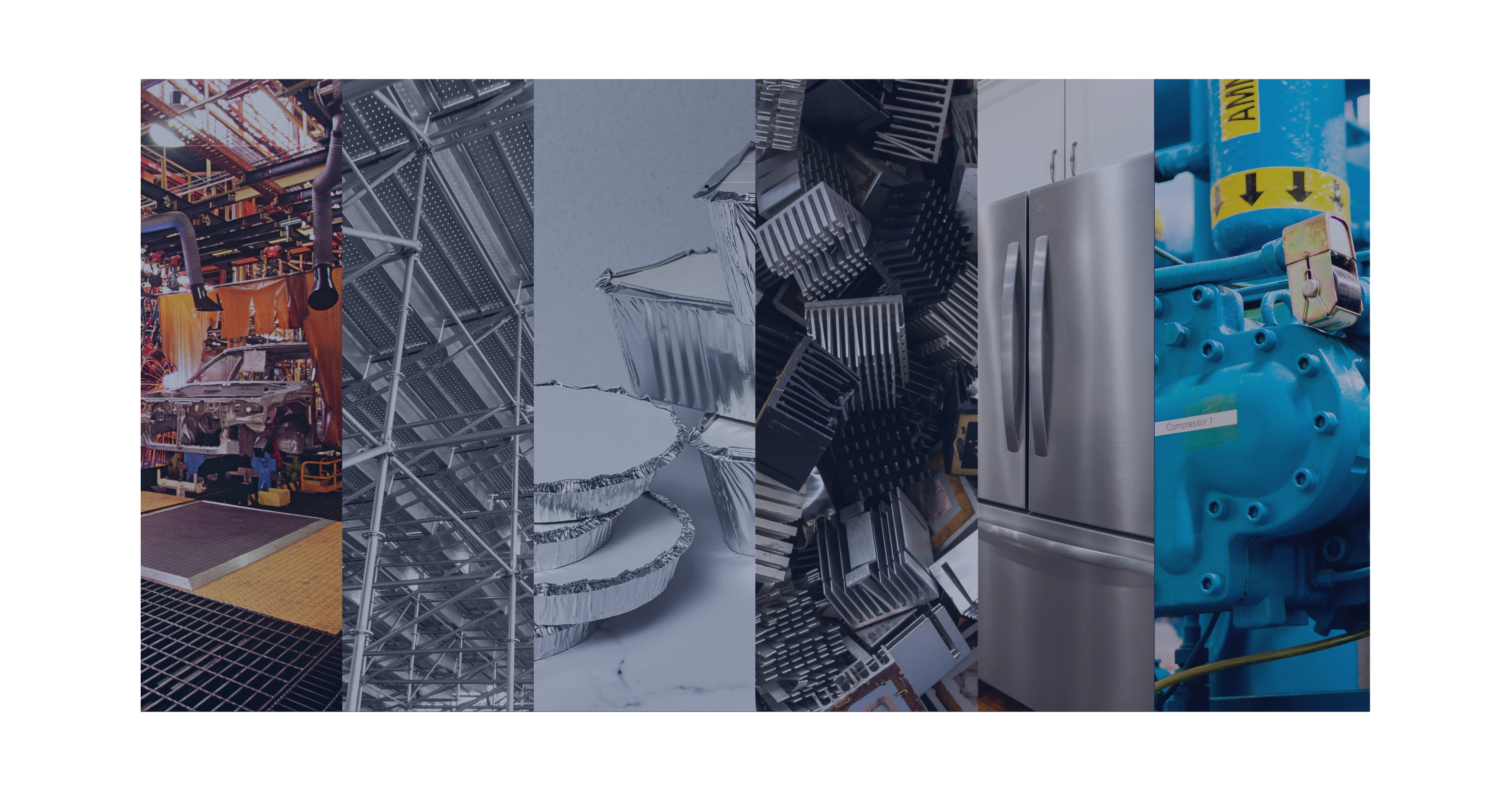
- Transportation: Aluminum is used in the production of cars, airplanes, and trains due to its strength and lightweight properties.
- Construction: Aluminum is used in the construction industry for windows, doors, siding, and roofing due to its corrosion resistance and durability.
- Packaging: Aluminum is used in producing packaging materials, such as foil and beverage cans, due to its ability to be easily molded and shaped.
- Electronics: Aluminum is used in producing electronic devices, such as laptops and smartphones, due to its conductive properties.
- Appliances: Aluminum is used in producing devices, such as refrigerators and washing machines, due to its corrosion resistance and ability to be molded into complex shapes.
- Industrial: Aluminum is used in producing a wide range of industrial products, such as machinery and equipment, due to its strength and durability.
Overall, aluminum is an important and widely used material due to its strength, lightweight, and corrosion resistance. It has various applications in various industries, and its versatility makes it an essential material in many products and structures. First and foremost, you want to ensure your aluminum company can deliver the product on time. Aluminum is a popular material that many companies employ, and while it usually isn’t the most expensive choice, it is widespread. Because of this, delivery delays are common, especially at busy times of the year.
Zetwerk is the best aluminum manufacturing company for your specific needs. We offer high-quality products, have the capabilities to make anything you can imagine, and their pricing is better than the competition. We deeply understand the value customers place on quality, capabilities, pricing, delivery, and more. When you choose to work with us as your aluminum manufacturer, you will be assured that you are getting the best product for your needs.




