Gravity die casting is a decades-old manufacturing process that has proven itself to be a reliable and efficient method for producing high-quality metal products. Thanks to its ability to produce complex geometries, this process has become a go-to solution for many industries. In this blog we will explore the lists of gravity die casting products, learning about their benefits, applications and key considerations for choosing this method of production.
What Is Gravity Die Casting?
Gravity die casting, also known as permanent mold casting, is a technique for manufacturing high-performance components from a variety of low-temperature metals. Gravity casting differs from die casting in that the molten metal is poured into the mold without the use of additional force. In contrast to die casting, gravity die casting can utilize metal and sand cores to create more intricate designs referred to as semi-permanent mold casting.
Steps Involved In Gravity Die Casting Process
Gravity casting is a method that differs from die casting in that it relies solely on gravity to fill the mold with molten metal. This technique is great for those who want fast processing and mass production. The die is made of steel and can withstand high heat to melt aluminum, zinc, or other alloys. In just three steps, the gravity die casting process allows manufacturers to create precision parts at a high rate of speed.
- Die release agent : The first step in the process is to heat the mold and apply a release agent that will help remove the part from the alloy. This agent also helps cool down the mold surface after it casts a part, readying it for casting more parts.
- Part release : When the metal has cooled sufficiently, the operator or machine opens the die to release the part. Machining is then performed to remove any gate and runner features that were used to guide molten metal into the die cavity.
- Metal pouring : After the coating is applied, molten alloy is poured into a mold. To do this, metal is poured into runners that transport it to different parts of the cavity and ensure proper filling of the cavities. When pouring metal into a mold, the designated runner must fill it from the bottom up to prevent turbulence in the hardened part and pores. Machines can do this automatically, or it can be done by hand with steel ladles.
What Are The Benefits Of Gravity Die Casting?
Gravity die casting is a preferred technique because it does not rely on high pressure, is versatile, and can be used with a variety of materials. These include:
- The right tool ensures consistent, repeatable quality.
- Tight tolerances ensure excellent accuracy of finished parts.
- The mechanical properties are better than sand casting, including tensile strength.
- Gravity die casting allows for shorter production times and faster lead times by reducing the number of production steps and simplifying the rod.
- Part walls can be thinner than sand castings.
- Sand core inserts can be performed and used to create internal pockets.
- Gravity die castings have a much smoother surface than sand castings.
- The part can be made with steel pins and internal inserts.
Limitations Of Gravity Die Casting
- Tooling costs more than sand casting.
- The production rate of some alloys can be slower than high pressure casting.
Key Considerations Of Choosing Gravity Die Casting Method
When choosing a casting process, consider the desired surface finish, complexity and mechanical properties of the finished product. Other considerations include production speed, lead time and process flexibility, as well as commercial considerations such as cost. Gravity casting is a suitable process for short production runs because it has lower initial tooling costs than die casting. It can also be used with zinc, brass, and magnesium alloys; however, metals with higher melting points are not suited to this process. Although gravity die casting is much heavier than die casting, it produces thinner sections than produced by less precise sand casting process.
Lists Of Gravity Die Casting Products Used In Industries
Most of the gravity die casting products are produced using aluminum that weigh from 1 lbs to 100 lbs. We can see these products in numerous sectors including:
- Military components: parts for surveillance, weaponry, and more.
- Electrical components: Motor housings, switchgear components, transformer components.
- Aerospace components: Engine parts, and hydraulic components.
- Automotive components : Engine blocks, cylinder heads, brake calipers, knuckles, transmission parts, suspension components, electronic and structural equipment, turbos, gearbox cases, and more.
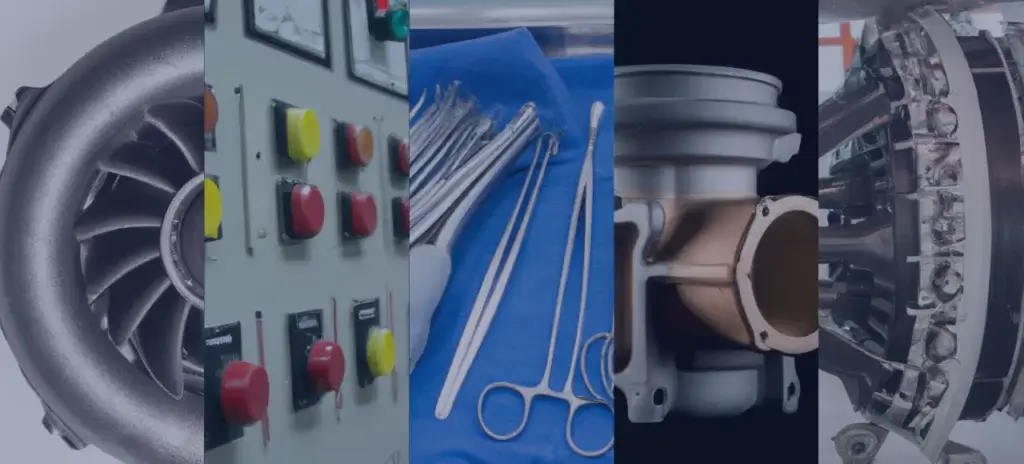
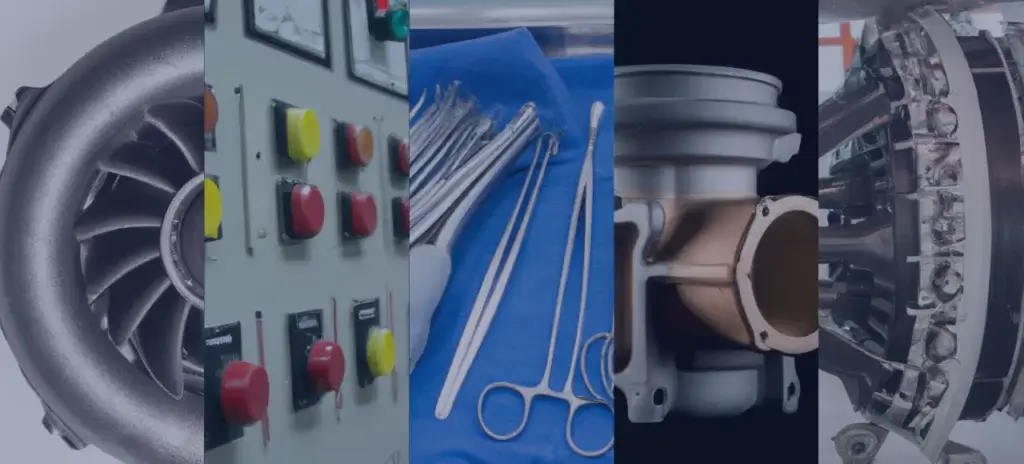
For a hassle-free and reliable sourcing of Gravity Die Casting Products, contact Zetwerk. Our vast network of trusted suppliers and top-notch manufacturing facilities make them the ideal solution for businesses looking for high-quality products at competitive prices. Visit our website today to learn more about our manufacturing services and see how we can help your business thrive.





