The Vital Role of Investment Casting Die Makers in the Precision Metal Casting Process
Investment casting, also known as a lost wax casting, has been used for millennia to produce delicate and accurate metal components. In investment casting, a ceramic shell is applied to a wax design, which is heated until the wax melts and drains away, leaving a mold. This mold is then filled with molten metal to produce a nearly identical component to the original wax pattern. A well-made die is key to a successful investment casting. Die or mold is the backbone of investment casting and dictates the quality and precision of the final product.
A qualified investment casting die maker is required to create a high-quality die that will result in a casting that is precise, consistent, and precise. Typically, a die maker will begin by developing a pattern, which is a detailed and precise reproduction of the final result. Typically formed from wax or a similar substance, this pattern is utilized to create the mold. The pattern is then coated with a ceramic slurry and allowed to cure, forming a ceramic shell around it. After baking the shell to firm it, the wax is melted away, leaving a mold.
The following stage involves preparing the mold for casting. This entails washing and polishing the mold’s inside to remove any impurities or flaws. Before the mold is prepared for casting, the diemaker will inspect it for any defects or problems and make any required repairs. The mold is heated to a high temperature in the casting process and then filled with molten metal. Once the metal is cooled down and solidified, the mold is cut off to expose the casting.
The investment casting process relies heavily on the talent and experience of the investment casting die, manufacturer. A skilled die maker has a thorough understanding of the materials and processes involved in investment casting and knows how to design a mold that will yield a casting of excellent quality. Additionally, they must have a keen eye for detail, as even little faults in the mold can result in significant defects in the final casting.
In addition to their technical abilities, a professional investment casting die manufacturer must also possess the ability to collaborate with others. They must be able to speak with the customer to ascertain if the final product fits their requirements and expectations. Additionally, they must be able to work with other members of the investment casting team, such as ceramists, to ensure that the casting process is as fast and successful as possible.
Diemakers for investment casting play a vital role in the investment casting process. They are responsible for developing high-quality molds that result in accurate, consistent, and precise castings. They must exhibit a blend of technical capabilities, attention to detail, and teamwork abilities. Investing in a qualified and experienced investment casting die maker is essential to investment casting success.
Factors to select Investment Casting Die Makers in 2023
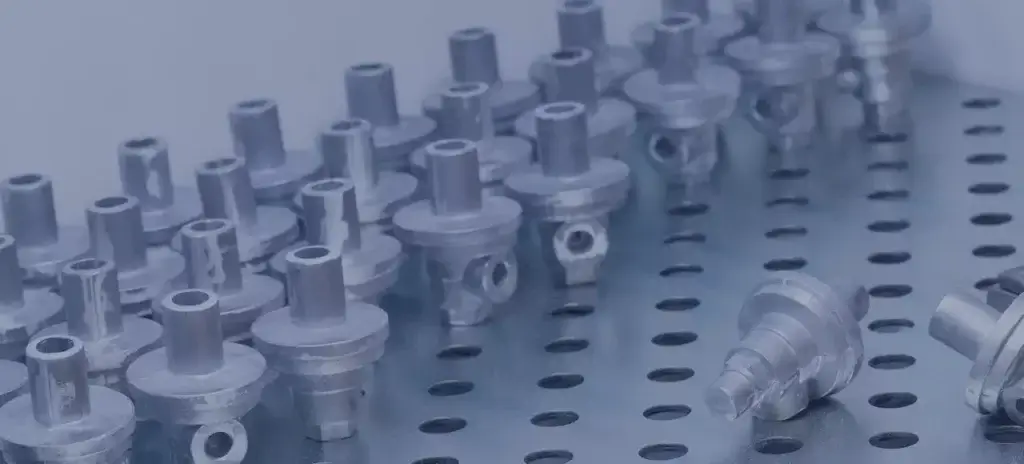
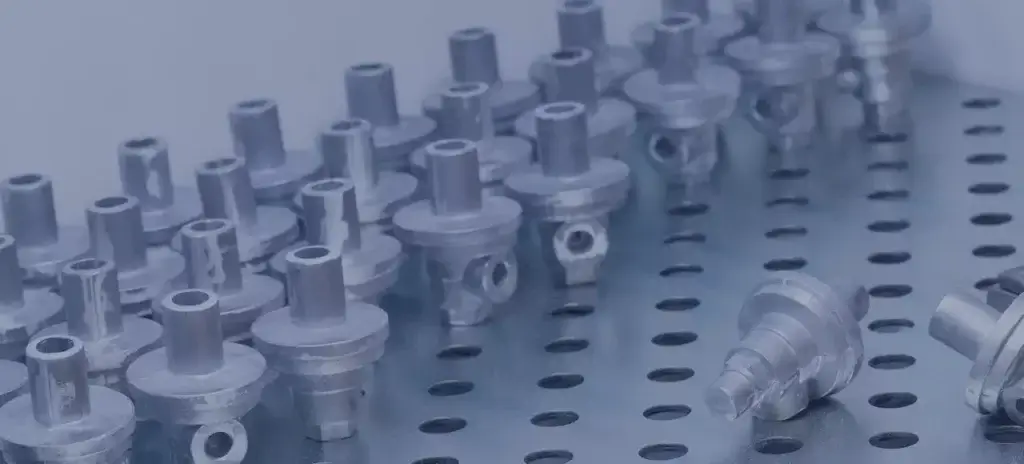
When selecting an investment casting die maker in 2023, there are many crucial elements to examine to guarantee a knowledgeable and experienced expert who can produce high-quality castings. These factors are as follows:
- Technical expertise: The die maker should have a comprehensive comprehension of the components and procedures involved in investment casting, as well as the knowledge necessary to design and construct a mold that will result in the casting of superior quality.
- Attention to detail: The die maker needs to have a keen eye for detail since even slight imperfections in the die can lead to significant problems in the casting that is produced.
- Communication skills: The die maker ought to be able to communicate effectively with the customer to understand the customer’s requirements and ensure that the end product meets the customer’s expectations.
- Customer service: A die manufacturer who prioritizes providing excellent customer service and is prepared to go the extra steps to fulfill their client’s requirements is more likely to provide a satisfying experience.
- Experience: An investment casting die maker with a history of creating castings of high quality is more likely to produce consistent outcomes because of their level of expertise. Consider a die manufacturer that has worked in the industry for a considerable time.
- Equipment and technology: To build exact and accurate molds, a professional die maker should have access to the most up-to-date equipment and technology in the industry.
- Collaboration skills: To ensure that the casting process is as effective and efficient as possible, the die maker needs to be able to interact effectively with other members of the investment casting team, such as ceramists.
- Quality control: A competent die maker should have a stringent quality control procedure to guarantee that each mold is free from flaws and is prepared for casting.
By examining these variables, you may select a die manufacturer for investment casting who will help you obtain the desired outcomes and advance your investment casting process. Zetwerk is a renowned manufacturer that provides end-to-end die producing solutions for investment casting projects. We provide investment casting dies explicitly built for each project’s demands. The team of seasoned engineers and technicians at Zetwerk uses the most advanced design and manufacturing methods to develop efficient and long-lasting investment casting dies of superior quality.
Zetwerk’s investment casting dies are designed to offer high precision and accuracy, ensuring that the final product meets the client’s exact specifications. To ensure that the investment casting dies are entirely functional and ready for use, we also offer a variety of post-manufacturing services, including heat treatment, machining, and finishing.



