Precision Casting Parts Manufacturer – How To Choose The Right One
Since its inception, precision casting, also known as investment casting, has advanced significantly. It has grown from a method used to manufacture simple parts to one capable of manufacturing complicated items with precise details and high precision. Precision casting is a manufacturing process that entails producing a wax model of a component, encasing it in a ceramic body, melting the wax, and pouring metal into the shell.
The outcome is a high-precision casting with a very few thousandths of an inch accuracy. Historically, producing complicated parts was a difficult and time-consuming procedure. Complex parts required numerous operations, such as machining and welding, to manufacture, and the final product needed to be more precise for essential applications. Precision casting has enabled manufacturers to build complicated components with high precision and accuracy. The method has transformed the manufacturing business by introducing a new level of efficiency, dependability, and quality to the production of intricate parts.
Precision casting’s ability to make pieces with precise details and high precision is one of its primary advantages. The procedure enables manufacturers to create parts with specific geometries, thin walls, and complex shapes that would be impossible to create using traditional casting techniques. Precision casting produces exact parts within a few thousandths of an inch, making them excellent for situations where precision is essential. Precision casting produces components in various industries, from aerospace and defense to medical and automotive.
The capacity of precision casting to make pieces with exceptional dimensional stability is another advantage. The procedure comprises encasing the wax model of the component in a ceramic shell. The ceramic body provides high dimensional stability, which means that the precision-cast pieces will retain their shape and size even in difficult situations. This is especially relevant for applications where the components must work under extreme stress and temperature conditions. Precision casting is excellent for producing complicated pieces that demand high precision and accuracy due to its high dimensional stability.
Additionally, precision casting is a very efficient procedure. The approach removes the requirement for various processes, such as machining and welding, that conventional casting methods require to make complex pieces. This minimizes the lead time and production costs associated with making complex parts. Precision casting removes the need for expensive tooling, which conventional casting techniques require. Precision casting is a cost-effective method for producing complicated components, particularly for low- to medium-volume production runs.
Also, the precision casting technique offers exceptional material adaptability. Precision casting applies to various materials, such as steel, titanium, and aluminum. This makes it a perfect method for making complex parts from different materials, allowing producers to select the optimal material for their application. Precision casting also provides excellent surface quality, consisting of a smooth and uniform surface ready for use without extra machining or polishing.
The impact of precision casting on reducing waste and increasing efficiency in the manufacturing process
Precision casting is an exact and efficient production method that substantially impacts minimizing waste and boosting manufacturing efficiency. The procedure removes the requirement for additional operations, such as machining and welding, necessary for conventional casting methods, lowering manufacturing lead time and expense. In addition, precision casting eliminates the requirement for tooling, which is a significant expense in traditional casting technologies, further reducing manufacturing costs.
Precision casting’s ability to make pieces with excellent dimensional stability is one of its primary advantages. The ceramic shell utilized in the method gives excellent dimensional stability, meaning that the items produced by precision casting will retain their shape and size even in hostile environments. This reduces the need for extra machining or finishing, hence decreasing production waste.
The casting procedure removes the requirement for additional operations, such as machining and welding, necessary in conventional casting methods, lowering manufacturing lead time and expense. In addition, precision casting eliminates the requirement for tooling, which is a significant expense in conventional casting technologies, further reducing manufacturing costs.
Precision casting’s ability to make pieces with excellent dimensional stability is one of its primary advantages. The ceramic shell utilized in the method gives great dimensional stability, meaning that the items produced by precision casting will retain their shape and size even in hostile environments. This reduces the need for extra machining or finishing, hence decreasing production waste.





Revolutionizing Complex Part Production: The Advantages of Precision Casting
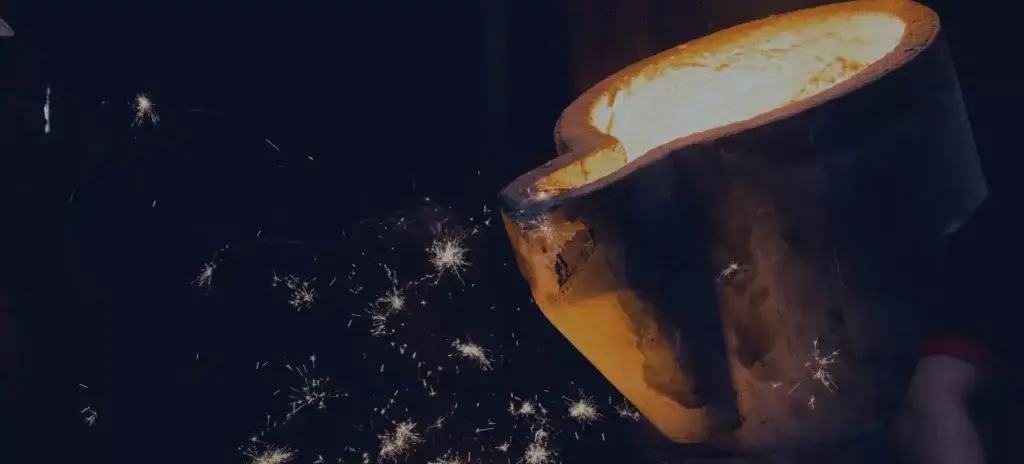
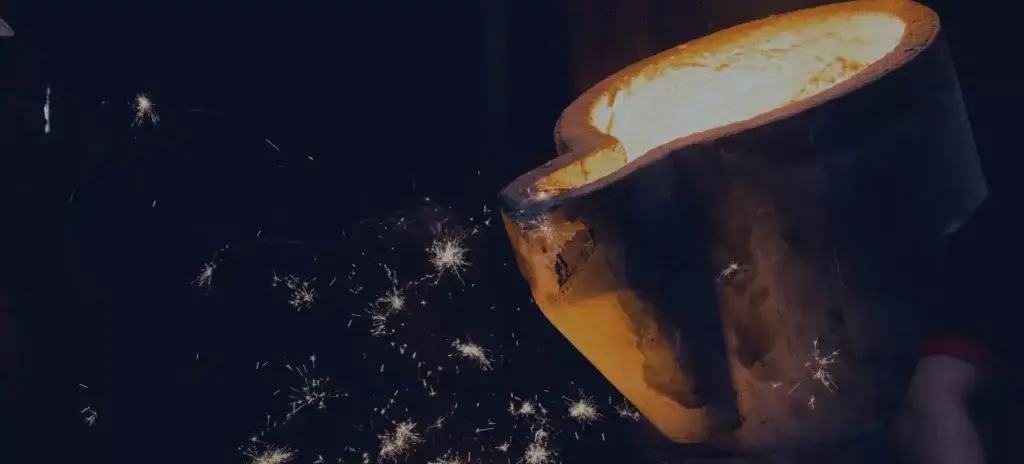
Precision casting’s ability to make complicated parts with high precision and accuracy is one of its primary advantages. The procedure enables manufacturers to create parts with precise geometries, thin walls, and complex shapes that would be impossible to create using traditional casting techniques.
Due to the great precision of precision casting, the parts produced are appropriate for applications requiring accuracy, such as those in the aerospace and defense industries. Furthermore, precision casting gives excellent dimensional stability, which implies that the created parts will retain their shape and size even in hostile environments.
This is especially relevant for applications where the components must work under extreme stress and temperature conditions. Precision casting is appropriate for areas such as the medical and automotive sectors, where accuracy and dependability are crucial because of its excellent dimensional stability.
Precision casting is also incredibly efficient, reducing the time required to produce complex components and lowering manufacturing costs. The procedure removes the requirement for various operations, such as machining and welding, which are necessary for conventional casting methods and expensive tools. Precision casting also provides significant material versatility since the technique can be applied to various materials, including steel, titanium, and aluminum. This enables industries to select the optimal material for their application, hence increasing efficiency and decreasing waste.
Zetwerk is a manufacturing company specializing in precision casting parts for various projects. They have a team of highly skilled engineers who use advanced technologies and techniques to produce high-quality casting parts that meet industry standards. Zetwerk also works closely with its clients to understand their requirements and deliver customized solutions that meet their needs. They offer a wide range of casting materials, including aluminum, brass, bronze, and stainless steel. Additionally, Zetwerk provides comprehensive services, including design, manufacturing, quality control, and logistics, ensuring that clients receive end-to-end project support. With their expertise and commitment to quality, Zetwerk is a reliable partner for precision casting parts in any industry.




