In the world of precision engineering and manufacturing, the creation of custom die casting parts plays a pivotal role. These intricate components find their application in a wide range of industries, from automotive to aerospace. As demand for high-performance and tailor-made parts continues to grow, the emphasis on quality control becomes paramount. This article delves into the crucial aspects of maintaining excellence in the production of custom die casting parts, highlighting the significance of quality assurance processes.
The Art of Crafting Custom Die Casting Parts
Custom die casting is a specialized process that involves injecting molten metal, such as custom aluminum die casting or custom zinc die casting parts, into meticulously crafted molds. The result is a near-net-shape component that exhibits exceptional strength, precision, and surface finish. The versatility of this process allows for the manufacturing of complex parts that are both lightweight and durable, meeting the unique requirements of various industries.
The Crucial Role of Quality Control
Precision in Custom Die Casting Part Dimensions
Custom die casting parts must adhere to strict dimensional specifications to seamlessly fit into larger assemblies. Employing advanced metrology techniques like 3D scanning and coordinate measuring machines (CMMs) ensures that every custom die casting part meets the exacting tolerances demanded by the design. This dimensional accuracy guarantees optimal functionality and compatibility.
Minimizing Defects in Custom Die Casting Parts
Quality control measures are instrumental in identifying and rectifying defects that may arise during the die casting process. Advanced technologies like X-ray and ultrasonic inspection help pinpoint internal flaws that could compromise the structural integrity of custom die casting parts. By detecting these defects early on, manufacturers can eliminate subpar components, thus enhancing the overall reliability of the final product.
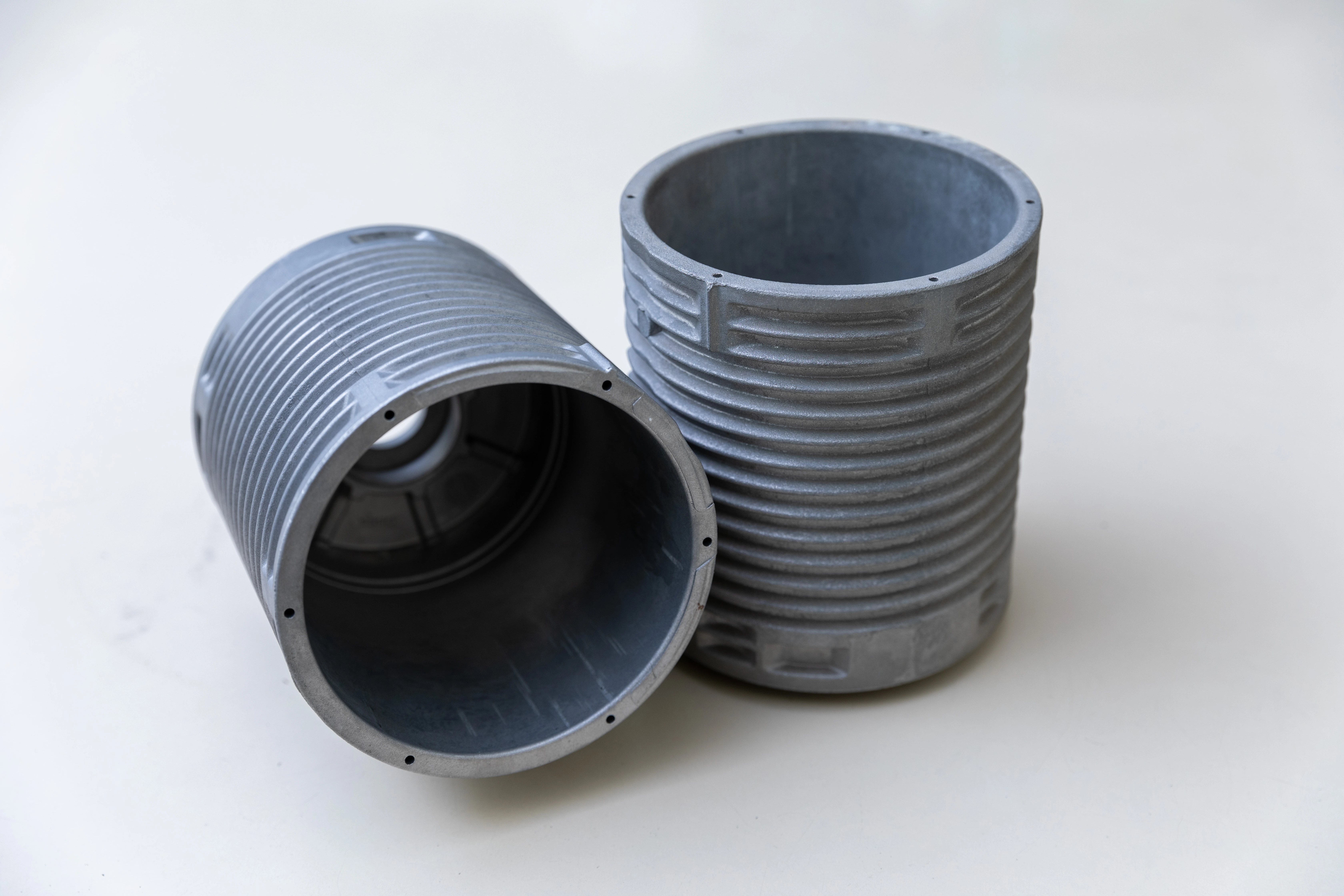
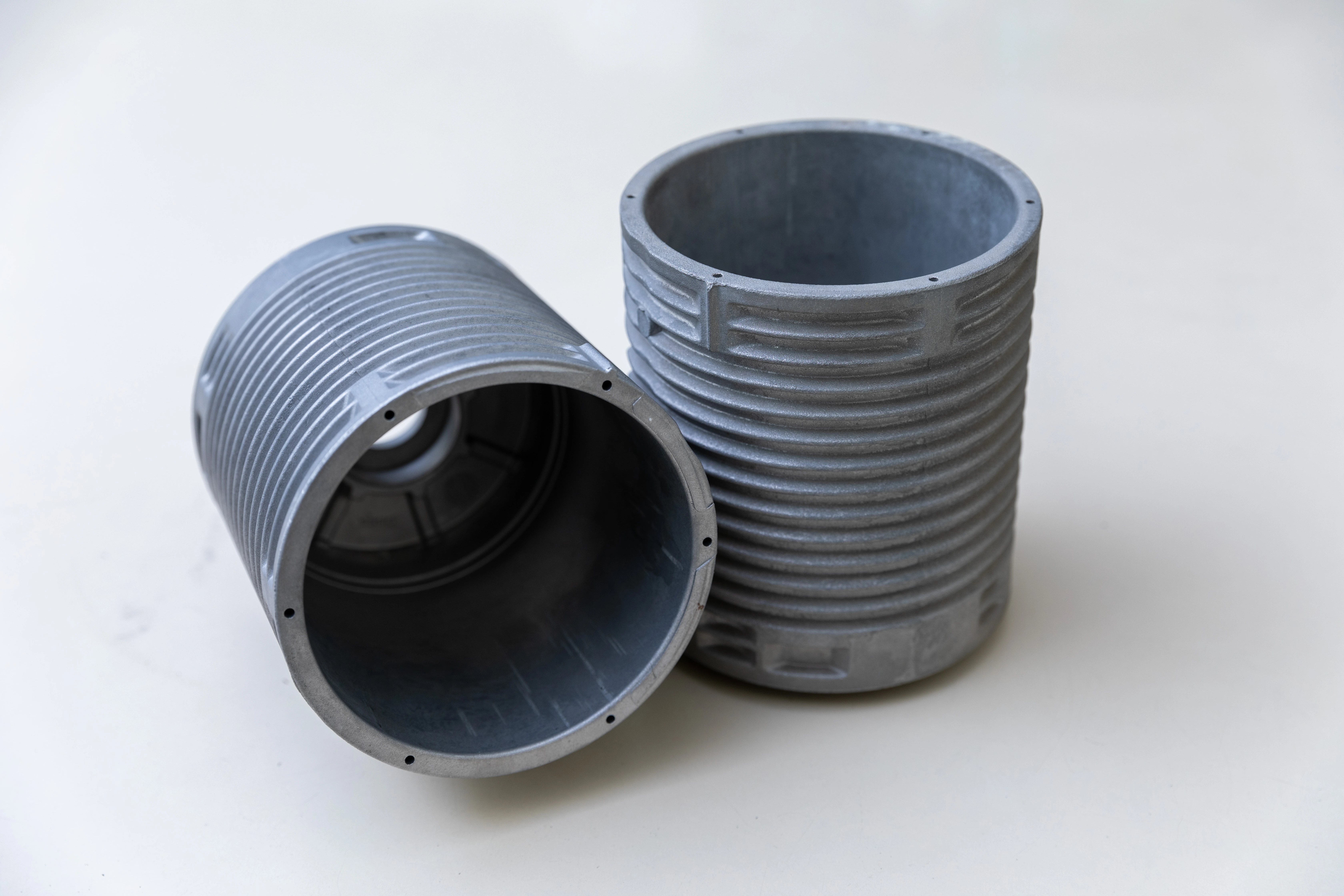
Implementing Robust Quality Assurance Processes
Leveraging Advanced Simulation Tools
The journey towards impeccable quality begins with the use of cutting-edge simulation tools. These tools enable engineers to virtually analyze the die casting process, predict potential defects, and optimize mold designs for custom die casting parts. By simulating various scenarios, manufacturers can make informed decisions that lead to enhanced part quality.
Ensuring Material Excellence in Custom Die Casting
Custom die casting involves the careful selection of materials that meet specific performance criteria. Conducting thorough material testing, including mechanical property analysis and chemical composition verification, guarantees the suitability of the chosen metal for custom die casting. This not only enhances the part’s functionality but also contributes to its longevity.
Transitioning from Inspection to Prevention
In the pursuit of excellence, a shift from mere inspection to proactive prevention is essential. Rather than relying solely on post-production inspections, manufacturers are embracing technologies that identify issues before they escalate. This approach reduces production bottlenecks, minimizes waste, and optimizes overall efficiency in crafting custom die casting parts.
Fostering Sustainability in Custom Die Casting Parts Production
Waste Reduction Efforts
Embracing quality control practices in custom die casting parts production inherently leads to waste reduction. By preventing the production of defective parts, manufacturers reduce material waste and energy consumption. This not only contributes to operational cost savings but also aligns with sustainable manufacturing practices.
Prolonged Lifespan of Custom Die Casting Parts
A core tenet of quality control is the creation of custom die casting parts that endure the test of time. Components manufactured through meticulous processes and stringent quality checks inherently boast extended lifespans. This longevity translates to reduced replacement cycles, conserving resources, and minimizing environmental impact.
Key Takeaways:
In the intricate realm of custom die casting parts production, the pursuit of quality control is an unceasing journey toward perfection. Through advanced technologies, rigorous processes, and a commitment to excellence, manufacturers ensure that every custom die casting part that leaves their facilities is of the highest standard. By embracing quality control, the industry not only meets the demands of the present but also shapes a future characterized by precision, reliability, and sustainability in crafting custom die casting parts.
Explore Zetwerk’s Knowledge Hub
Zetwerk offers a wide range of services related to custom die-casting parts production. Whether you’re looking for aluminum or zinc die-casting parts or require assistance with quality control processes, Zetwerk’s expertise can help you meet your specific requirements. For more articles related to quality control in manufacturing and other valuable insights into the industry, explore Zetwerk’s Knowledge Hub.




FAQs
Custom die-casting parts are components produced through the die-casting process, where molten metal is injected into a mold cavity under high pressure to create complex shapes with tight tolerances. These parts are customized to meet specific design requirements.
Custom aluminum die-casting parts offer lightweight yet durable solutions due to the low density of aluminum. They have excellent thermal conductivity, corrosion resistance, and dimensional stability. Aluminum alloys also provide a high strength-to-weight ratio and good surface finishes.
Custom zinc die castings offer exceptional precision and dimensional accuracy, making them ideal for intricate designs. Zinc alloys have excellent fluidity, allowing complex shapes with thin walls to be produced easily. They also provide superior electrical conductivity and can be easily plated or finished.
Quality control measures throughout the manufacturing process help identify and rectify any issues that may affect the quality of custom die-casting parts. By implementing strict inspections, and testing procedures, and adhering to industry standards, manufacturers can ensure defect-free production.
Mold design is crucial in producing high-quality castings as it determines factors such as flow rate, pressure, filling speed, and gas entrapment prevention during the injection process. Optimal mold design ensures proper alloy flow, reduces defects like porosity or cold shuts, and improves overall casting quality.