Die-casting has a rich history that dates back thousands of years. The first evidence of its use can be traced back to as early as 6000 BC in China. However, it wasn’t until the mid-19th century that modern die-casting techniques were developed. China played a significant role in promoting die-casting techniques, particularly during the Song Dynasty (960-1279 AD). The Chinese mastered bronze castings using intricate molds made from clay or sand. Over time, die casting evolved into a crucial element in modern manufacturing processes. It enables manufacturers to produce complex shapes with high precision and repeatability.
Advantages of Die-Casting Parts
Die-casting offers numerous advantages over other manufacturing methods. One key advantage is its ability to produce parts with exceptional strength-to-weight ratios. Aluminum die-castings, for example, are renowned for their lightweight properties while maintaining structural integrity. Precision is another hallmark of die-cast components. The mold design allows for intricate details and complex shapes that would be challenging to achieve through other processes. Furthermore, high-volume production is cost-effective and efficient with die casting due to its quick cycle times. The molds used in die casting can withstand thousands of cycles, making them ideal for mass production.
Top 5 Industries Benefiting from Die-Casting Parts
The following are the top five industries that greatly benefit from the use of die-casting parts:
Automotive Industry
The automotive industry is the largest purchaser of die-cast components. By 2026, it is projected to reach a market value of USD 58.4 billion with a compound annual growth rate (CAGR) of over 6.19%. Key components such as engine blocks made from cast iron or aluminum alloy provide the strength and efficient heat transfer required for high-performance vehicles.
Construction Industry
Die-cast parts are widely used in the construction industry due to their strength and lightweight properties. Aluminum metal castings are utilized in window frames, roof superstructures, building frames, bridges, and skyscrapers. These components offer durability while reducing structural weight.
Healthcare Industry
In the healthcare industry, complex medical devices rely on precise die-cast parts for performance and flexibility. Ultrasound systems, pacemakers, dialysis equipment, and medical robots require intricate components that can be efficiently produced through die-casting.
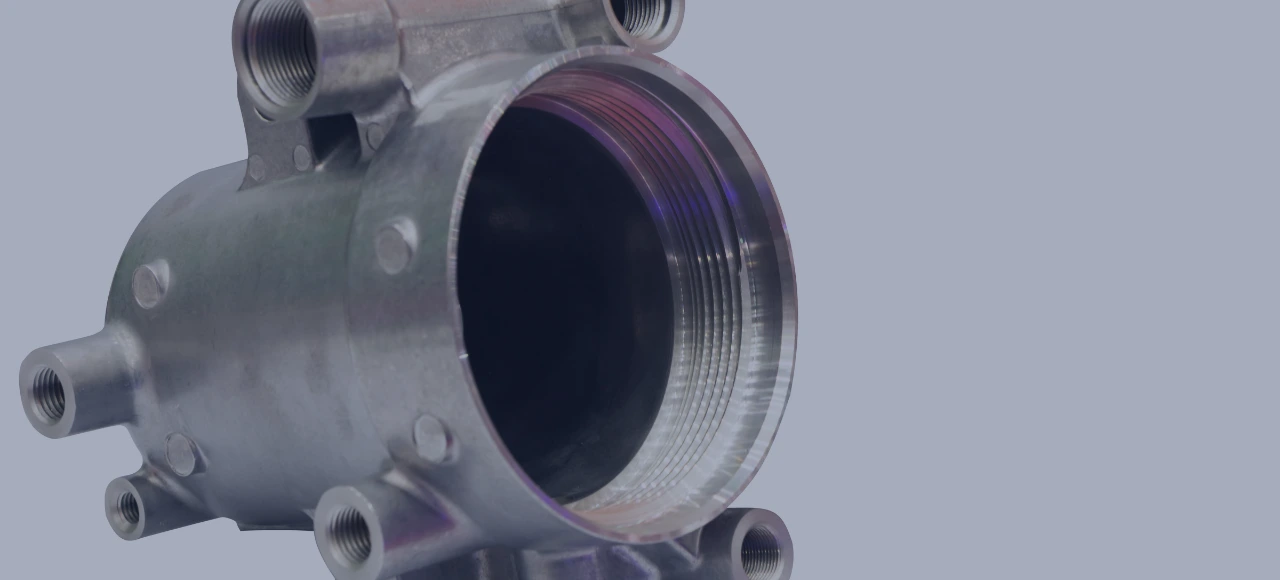
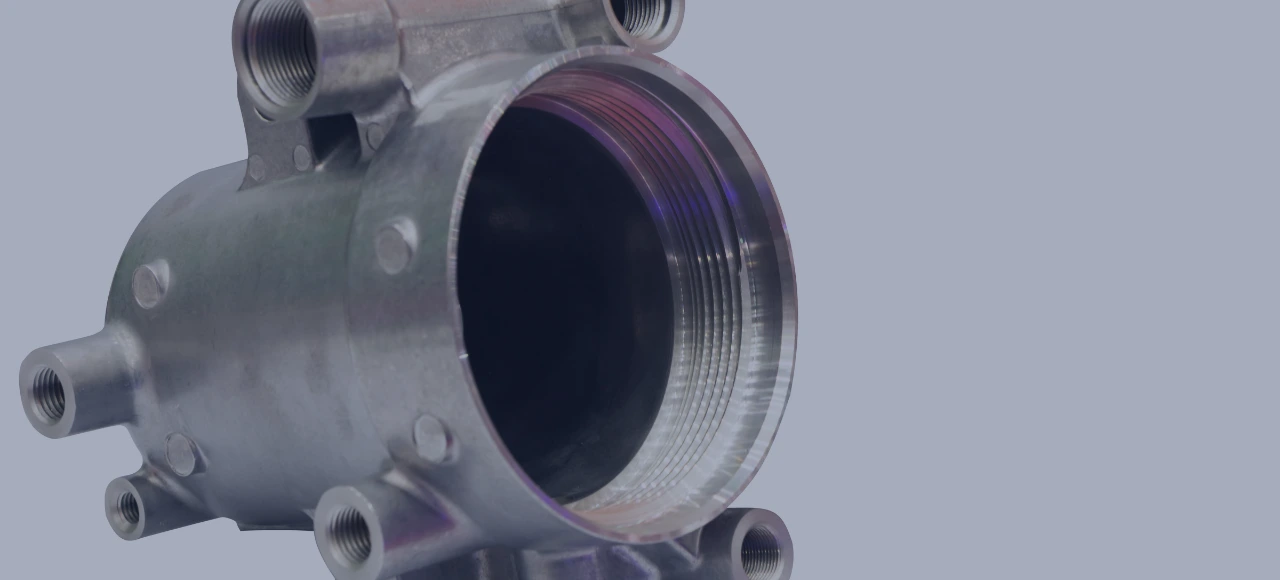
Energy Sector
Die-cast components are utilized in various applications within the renewable energy sector. Piping, drilling machinery, valves, impellers for wind turbines, and brackets for solar panels are all examples of parts made through the die-casting process. These components provide strength and durability while meeting the demand for sustainable energy sources.
Electronics Industry
The electronics industry extensively utilizes die-cast precision parts in products such as 5G base station housings, smartphones, drones, personal computers, and home appliances. The high precision achievable through die casting ensures reliable performance and durability in these electronic devices.
Conclusive Key Takeaways
In conclusion, the use of die-casting parts is crucial across various industries due to their advantages in terms of lightweight properties, strength-to-weight ratio, precision, and cost-effectiveness. The automotive industry leads as the largest purchaser of die-cast components while other industries like construction, healthcare, renewable energy, and electronics also greatly benefit from this manufacturing process.
As global supply chains face disruptions caused by factors like trade wars and pandemics, understanding the significance of reliable suppliers becomes essential for businesses seeking quality die-casting parts. Zetwerk offers a comprehensive range of manufacturing services including extrusions, die casting, CNC machining, forging injection molding sheet metal stamping. Explore Zetwerk’s website to learn more about how they can assist you in meeting your industry demands with high-quality die-casting solutions.




FAQs
Die-casting parts offer several advantages over other manufacturing methods. They provide excellent dimensional accuracy, and high production rates and can create complex shapes with tight tolerances. Additionally, die-cast parts have superior strength-to-weight ratios and excellent surface finishes.
High-pressure die casting is a process where molten metal is injected into a mold under extreme pressure. It is used in various industries to produce complex components with tight tolerances and excellent surface finishes. The automotive, electronics, and healthcare industries are just a few examples of sectors that benefit from high-pressure die casting.
Aluminum die-casting parts are widely used in many industries due to their lightweight properties and excellent strength-to-weight ratio. Common applications include automotive components such as engine blocks and transmission cases, electronic enclosures, aerospace components, and consumer goods like kitchen appliances.
Die-casting components play a crucial role in the automotive industry by providing lightweight yet durable solutions for key components such as engine blocks, transmission housings, suspension systems, and structural parts. Die-cast parts help improve fuel efficiency without compromising on strength or performance.
When selecting a supplier for die-casting parts, it’s important to consider factors such as experience in the industry, quality control processes, certifications (such as ISO 9001), material selection expertise, production capacity, and ability to meet specific requirements.