Printed Circuit Boards (PCBs) are the backbone of modern electronics, serving as the foundation for virtually every device we use today. Whether you’re developing consumer electronics, medical devices, or industrial systems, partnering with the right PCB contract manufacturer is critical to ensuring the quality, reliability, and performance of your product. However, selecting the best manufacturer can be challenging given the multitude of factors to consider. This guide will walk you through the key aspects of choosing a PCB contract manufacturer in electronics, helping you make an informed decision.
The Importance of Choosing the Right PCB Contract Manufacturer
The right PCB manufacturer can make your project. A competent manufacturer ensures high-quality production, adherence to timelines, and cost-effectiveness, while a poor choice can lead to delays, defects, and budget overruns. Additionally, the complexity of modern PCB designs—including multi-layer boards and advanced materials—requires specialized expertise and state-of-the-art equipment. This makes the selection process even more critical for businesses aiming to stay competitive.
Key Factors to Consider When Choosing a PCB Contract Manufacturer
1. Technical Capabilities
Evaluate the manufacturer’s technical expertise and capabilities. Ensure they can handle the complexity of your PCB design, including:
– Multi-layer PCBs
– High-density interconnect (HDI) boards
– Flexible and rigid-flex boards
– Advanced materials like Rogers or ceramic
Verify their ability to work with different technologies, such as through-hole and surface-mount technologies (SMT), and their proficiency in design for manufacturing (DFM) and design for testability (DFT).
2. Certifications and Compliance
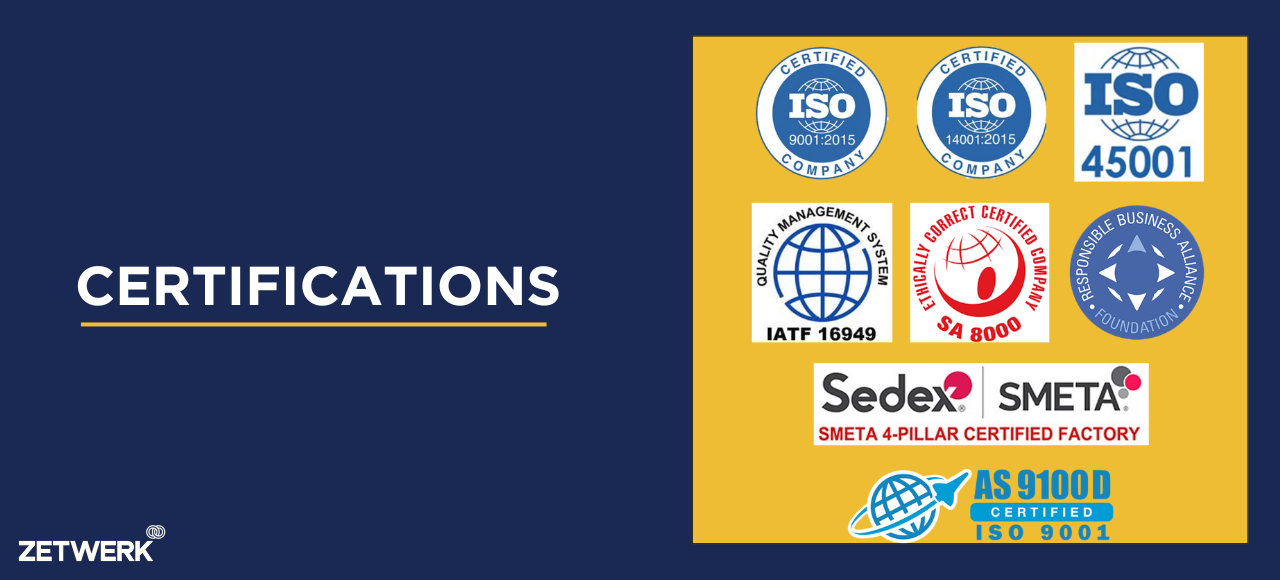
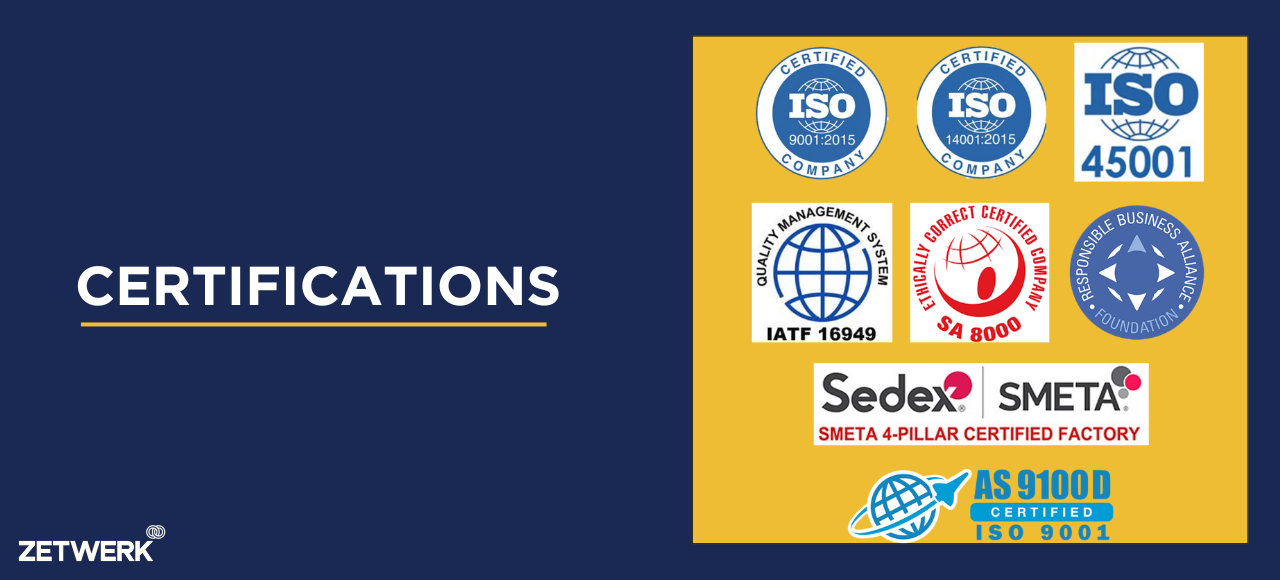
Certifications are a strong indicator of a manufacturer’s commitment to quality and compliance. Look for certifications such as:
– ISO 9001: Quality management systems
– ISO 13485: Medical devices
– IPC-A-610: Standards for electronic assembly
– AS9100: Aerospace and defense
– RoHS and REACH compliance for environmental standards
These certifications ensure that the manufacturer adheres to industry standards, reducing the risk of defects and ensuring product reliability.
3. Production Capacity and Scalability
Assess the manufacturer’s production capacity and ability to scale with your business needs. Whether you require a small prototype batch or high-volume production, the manufacturer should be equipped to handle varying levels of demand without compromising quality or lead times.
4. Quality Assurance Processes
A robust quality assurance (QA) process is essential for ensuring defect-free PCBs. Ask about their testing methodologies, which may include:
– Automated optical inspection (AOI)
– X-ray inspection for multilayer boards
– In-circuit testing (ICT)
– Functional testing
These tests ensure the PCBs meet design specifications and perform reliably in their intended applications.
5. Lead Times and Delivery
Time-to-market is critical in the competitive electronics industry. Evaluate the manufacturer’s lead times and on-time delivery record. Ensure they have efficient logistics and supply chain management systems in place to avoid delays.
6. Cost Transparency
While cost is an important factor, it should not come at the expense of quality. Request detailed quotes and ensure transparency in pricing, including material costs, labor, testing, and shipping. Beware of manufacturers offering significantly lower prices, as this may indicate subpar materials or processes.
7. Customer Support and Communication
Strong communication is vital for a successful partnership. Choose a manufacturer with a responsive and knowledgeable support team that can address your queries and provide updates throughout the production process. Regular communication minimizes misunderstandings and ensures project alignment.
8. Experience and Reputation
Research the manufacturer’s track record and industry reputation. Look for customer reviews, case studies, and testimonials to gauge their reliability and expertise. An experienced manufacturer is better equipped to handle challenges and deliver high-quality results.
9. Location and Logistics
The geographical location of the manufacturer can impact lead times, shipping costs, and tariff implications. Consider whether local or offshore manufacturing aligns better with your project’s requirements. Local manufacturers may offer faster communication and delivery, while offshore options can provide cost advantages.
Steps to Evaluate and Select a PCB Contract Manufacturer
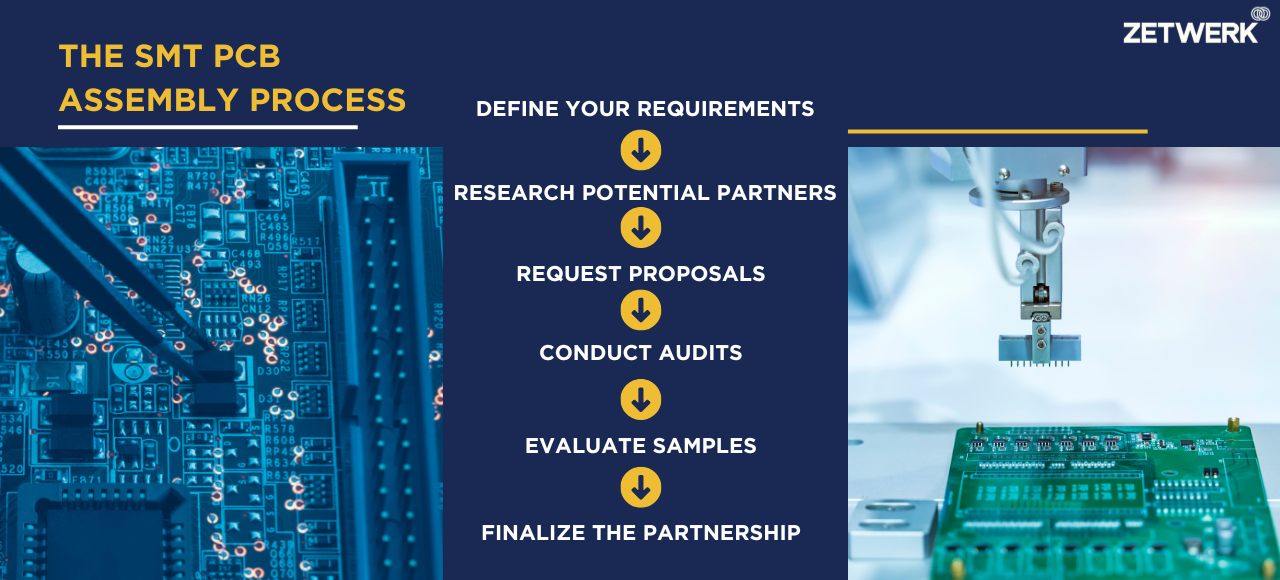
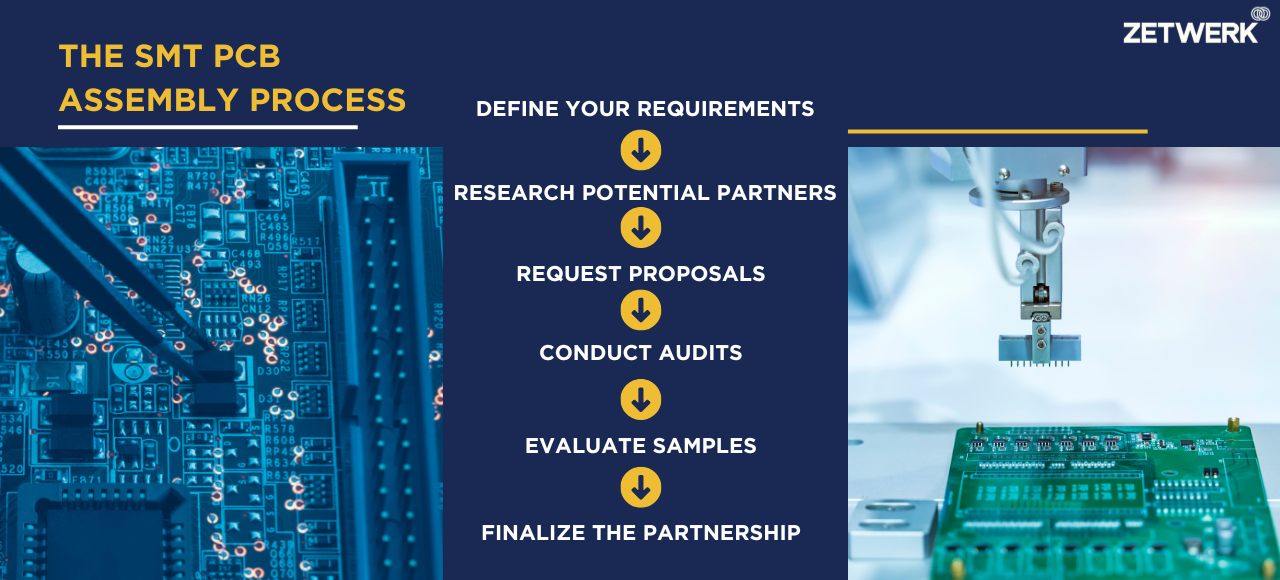
- Define Your Requirements: Clearly outline your technical specifications, volume needs, budget, and timeline.
- Research Potential Partners: Create a shortlist of manufacturers based on their expertise, certifications, and reviews.
- Request Proposals: Solicit detailed quotes and proposals, including technical capabilities, lead times, and pricing.
- Conduct Audits: If possible, visit the manufacturer’s facilities to assess their infrastructure, processes, and quality systems.
- Evaluate Samples: Request prototypes or samples to evaluate their quality and performance.
- Finalize the Partnership: Choose a manufacturer that aligns with your requirements and offers the best overall value.
Conclusion
Choosing the best PCB contract manufacturer is a critical decision that directly impacts your product’s quality, cost, and time-to-market. By evaluating factors such as technical capabilities, certifications, quality assurance processes, and customer support, you can select a reliable partner to support your business goals. Investing time in thorough research and evaluation will ensure a successful partnership and pave the way for your product’s success in the market.



FAQs
A. A PCB fabricator specializes in manufacturing the bare board, including layers, materials, and vias. An EMS (Electronics Manufacturing Services) provider, on the other hand, handles the assembly of components onto the PCB, along with testing and quality assurance. Some companies offer both services, providing a one-stop solution for businesses.
A. To ensure quality, choose a manufacturer with relevant certifications, robust QA processes, and advanced testing capabilities. Evaluate their track record and request prototypes for testing. Additionally, clear communication and regular updates can help maintain quality standards.
A. The choice between local and offshore manufacturers depends on your project’s priorities. Local manufacturers often provide faster communication and delivery, while offshore options may offer cost advantages. Consider factors like lead times, shipping costs, tariffs, and the complexity of your project when making this decision.
Contact Us
Contact us today to discuss your project requirements and discover how we can help you achieve your goals efficiently and effectively.