Printed Circuit Board Assembly (PCBA) manufacturing is the cornerstone of modern electronics, enabling the functionality of devices we use every day. From smartphones and laptops to industrial machinery and medical equipment, PCBA ensures seamless integration of electronic components into robust and reliable assemblies. Achieving high-quality PCBAs involves advanced processes, stringent quality control measures, and continuous innovation.
The PCBA Manufacturing Process
Delivering quality circuit assemblies starts with a comprehensive and precise manufacturing process. Each step is designed to ensure performance, durability, and compliance with industry standards. Here are the key stages:
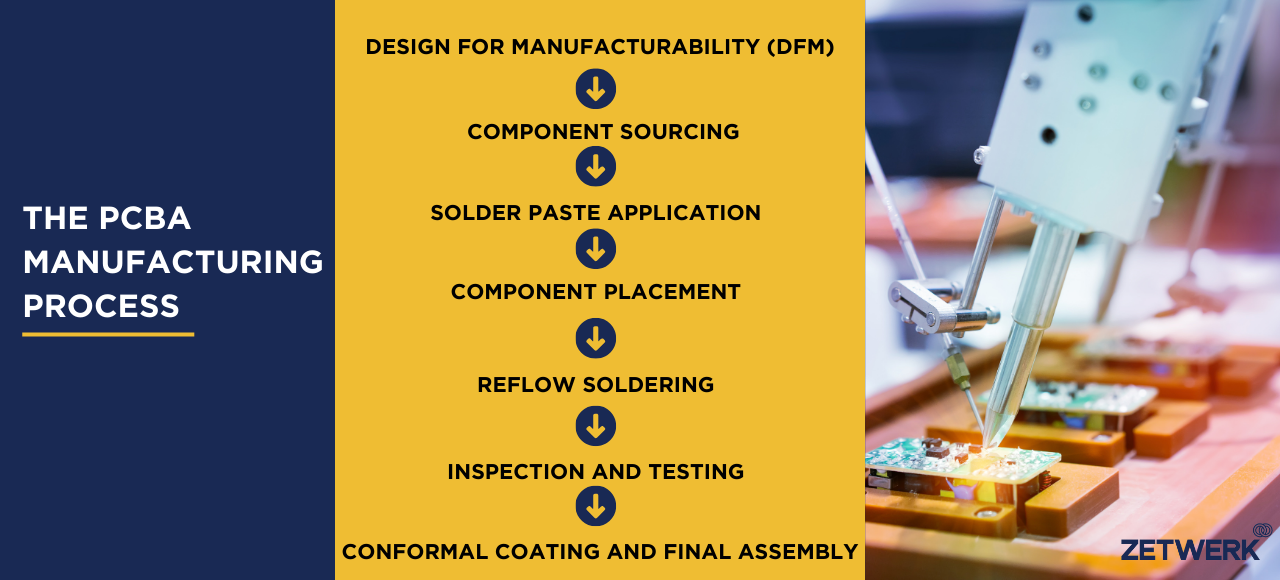
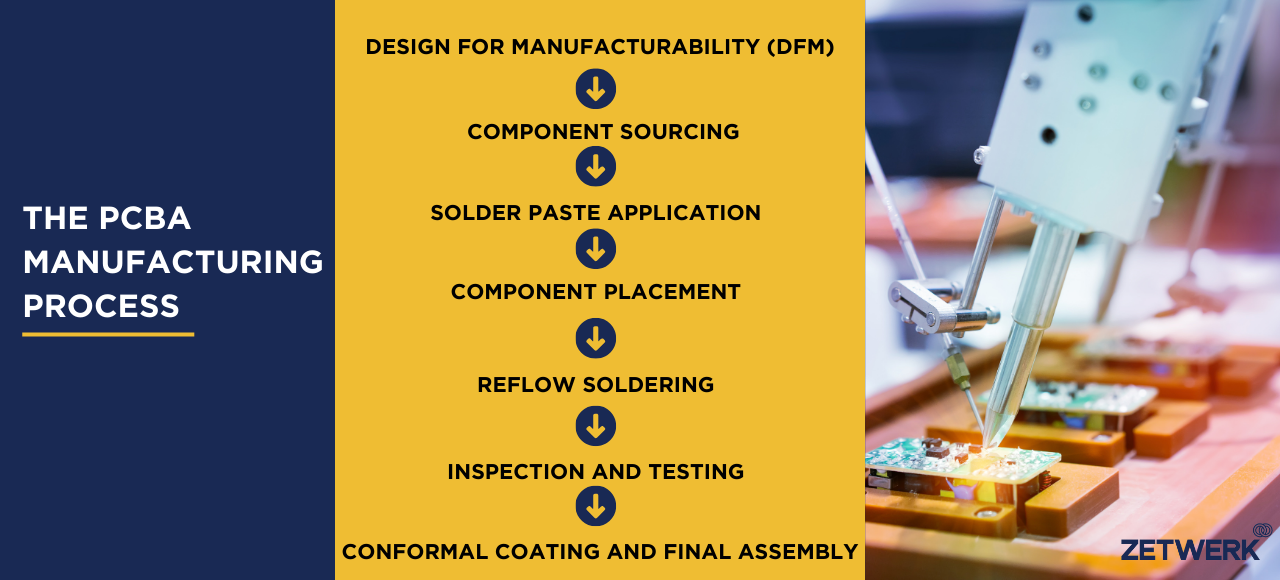
1. Design for Manufacturability (DFM)
The process begins with DFM, where engineers optimize PCB designs for efficient manufacturing. DFM identifies potential issues that could arise during production, reducing defects and improving yield.
2. Component Sourcing
- Quality components are critical to a successful PCBA. Reliable suppliers, compliance with RoHS standards, and thorough incoming inspection ensure that only high-grade materials are used.
3. Solder Paste Application
- Solder paste is applied to the PCB using a stencil to ensure precise deposition. This step lays the foundation for component attachment.
4. Component Placement
- Automated pick-and-place machines position components with precision based on the design specifications. Advanced vision systems verify the accuracy of placement.
5. Reflow Soldering
- The assembly passes through a reflow oven where the solder paste melts and creates reliable connections. Proper temperature profiling is critical to prevent defects such as cold joints or overheating.
6. Inspection and Testing
- Rigorous inspection methods like Automated Optical Inspection (AOI), X-ray inspection, and functional testing ensure the quality and reliability of the assembly.
7. Conformal Coating and Final Assembly
- For products exposed to harsh environments, conformal coating is applied to protect against moisture, dust, and chemical damage. Finally, the PCB is integrated into its enclosure or system.
Ensuring Quality in PCBA Manufacturing
Delivering high-quality PCBAs requires adherence to stringent quality control practices and standards. Here are key factors that manufacturers prioritize:
1. ISO Certifications and Industry Standards
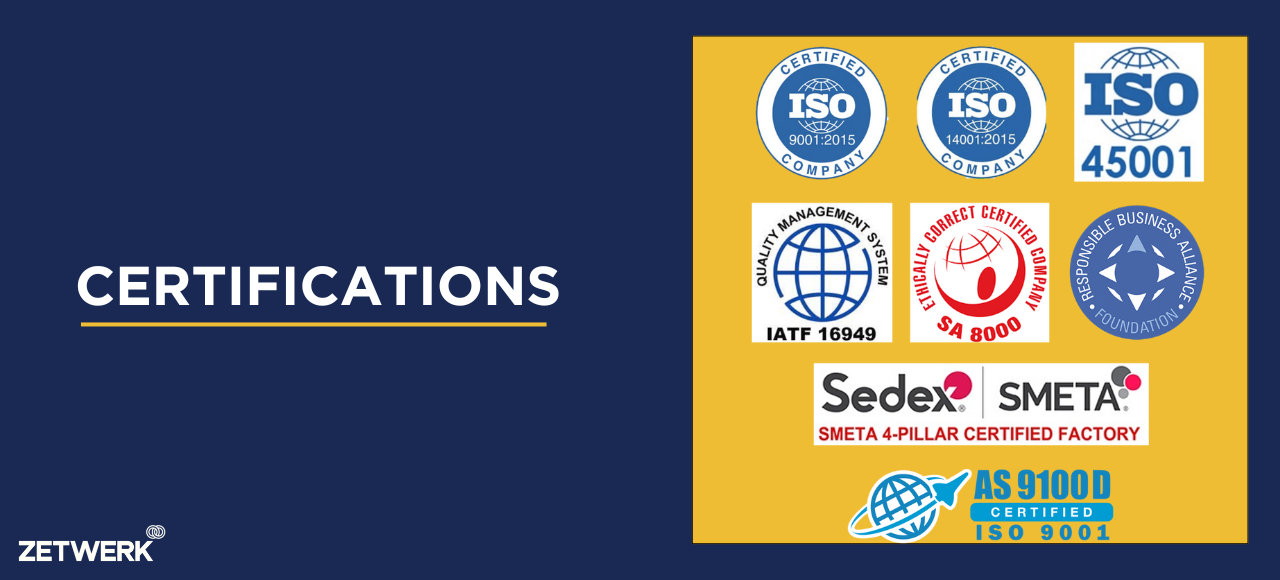
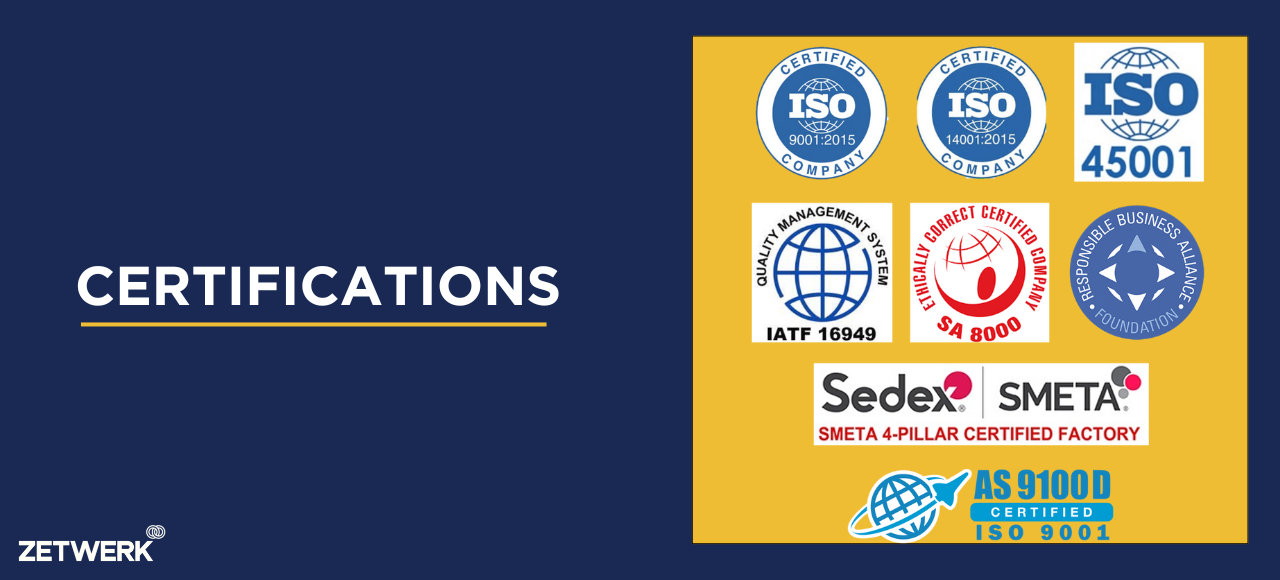
- Compliance with certifications such as ISO 9001, IPC-A-610, and ISO 13485 ensures that manufacturing processes meet global quality standards.
2. Traceability Systems
- Advanced traceability tools track every component and process step, enabling manufacturers to identify and resolve issues efficiently.
3. Process Automation
- Automation reduces human error and ensures consistent quality in processes such as solder paste application and component placement.
4. Continuous Improvement
- Manufacturers implement Six Sigma, Kaizen, and other methodologies to drive ongoing improvements in quality, efficiency, and cost.
5. Environmental Testing
- PCBAs undergo thermal cycling, humidity exposure, and vibration testing to ensure they meet the demands of real-world applications.
Trends in PCBA Manufacturing
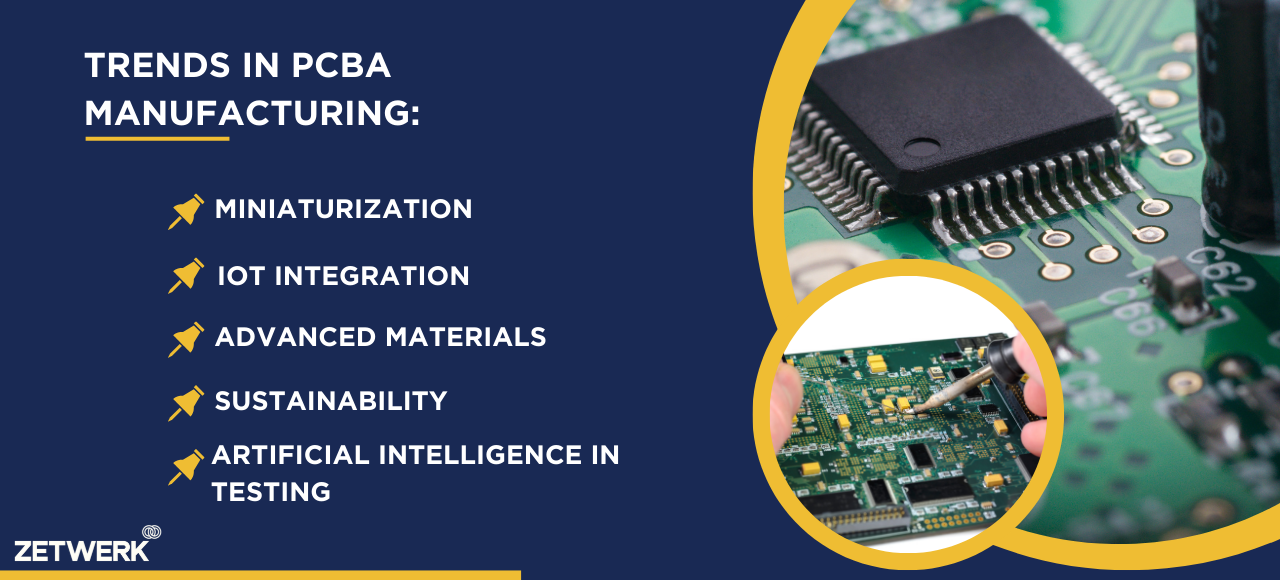
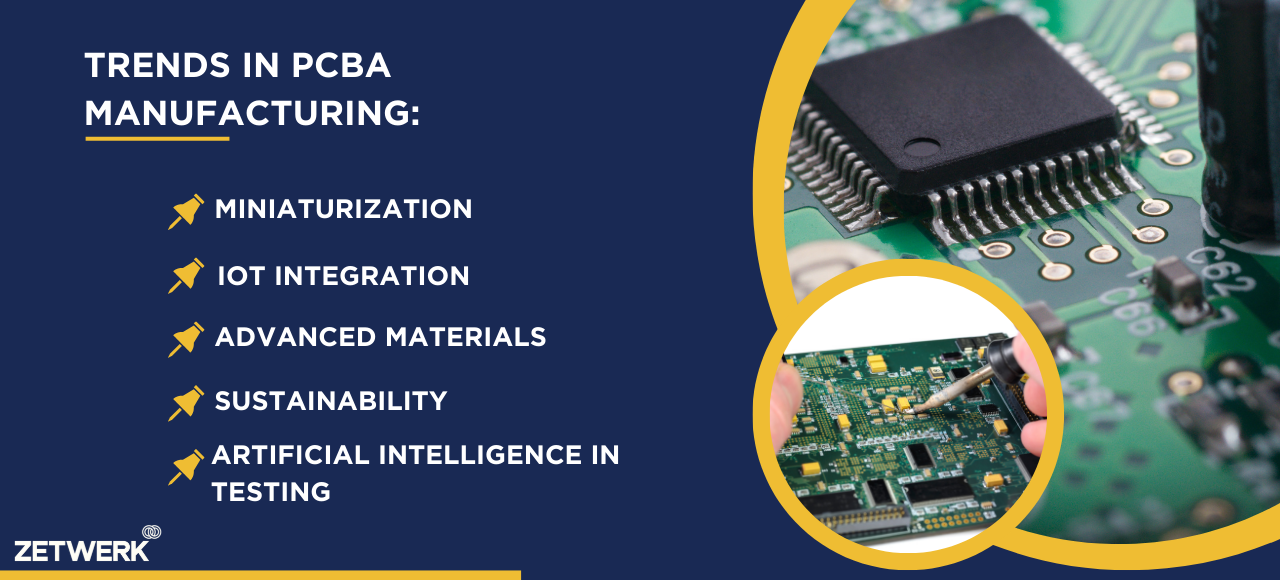
1. Miniaturization
- The demand for smaller, lighter devices has led to the development of compact PCB designs with higher component densities.
2. IoT Integration
- With the rise of the Internet of Things (IoT), PCBAs now include wireless communication modules, sensors, and advanced processors.
3. Advanced Materials
- High-frequency materials and flexible substrates are gaining traction for specialized applications in telecommunications, medical devices, and automotive electronics.
4. Sustainability
- Manufacturers are adopting eco-friendly practices, such as using lead-free solder, recycling waste, and reducing energy consumption.
5. Artificial Intelligence in Testing
- AI-powered testing systems are enhancing defect detection and predictive maintenance capabilities, improving efficiency and reducing costs.
Zetwerk Electronics: Excellence in PCBA Manufacturing
Zetwerk Electronics has established itself as a trusted partner for PCBA manufacturing, catering to diverse industries such as telecommunications, automotive, medical devices, and industrial machinery. Their key strengths include:
- Global Manufacturing Network: With facilities in India, Vietnam, and Mexico, Zetwerk offers cost-efficient manufacturing solutions while maintaining high quality.
- End-to-End Solutions: Zetwerk provides comprehensive services, from design support to assembly and testing, ensuring seamless execution of complex projects.
- Focus on Quality: Adhering to ISO and IPC standards, Zetwerk integrates advanced inspection techniques like AOI and X-ray testing into its processes.
- Scalability: Zetwerk’s flexible manufacturing capabilities enable it to handle both small and large-scale production requirements efficiently.
- Sustainability Initiatives: The company emphasizes eco-friendly practices, including waste management and energy-efficient manufacturing processes.
Conclusion
PCBA manufacturing is a complex and critical process that underpins modern technology. By focusing on quality, innovation, and sustainability, manufacturers are enabling the development of reliable and advanced electronic products. Companies like Zetwerk Electronics are setting benchmarks in the industry, offering exceptional PCBA solutions that drive technological progress. As the demand for smarter, more efficient devices continues to grow, PCBA manufacturing will remain a vital contributor to global advancements.



FAQs
A. A PCB (Printed Circuit Board) is the bare board without any components, while a PCBA (Printed Circuit Board Assembly) includes all the electronic components mounted and soldered onto the PCB, making it functional.
A. Reliability is ensured through rigorous testing, high-quality component sourcing, and adherence to industry standards such as IPC-A-610. Environmental tests further validate performance under real-world conditions.
A. Industries such as automotive, aerospace, medical devices, telecommunications, and consumer electronics heavily rely on high-quality PCBAs for their products.