In electronics manufacturing, the journey from concept to final product often begins with a prototype. Prototype design services play a pivotal role in ensuring the feasibility, functionality, and manufacturability of electronic products. By leveraging these services, businesses can reduce risks, improve efficiency, and accelerate time-to-market. Here, we explore the benefits and best practices of prototype design in electronics manufacturing.
The Importance of Prototyping in Electronics Manufacturing
Prototyping serves as a bridge between the design phase and full-scale production. It allows electronics manufacturers and designers to:
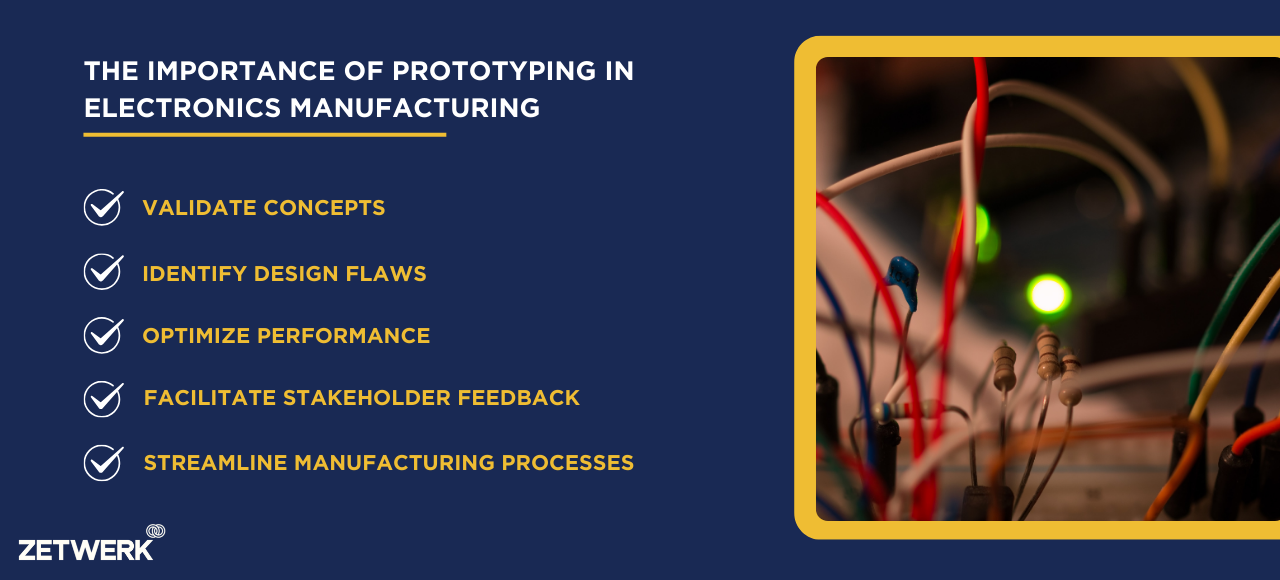
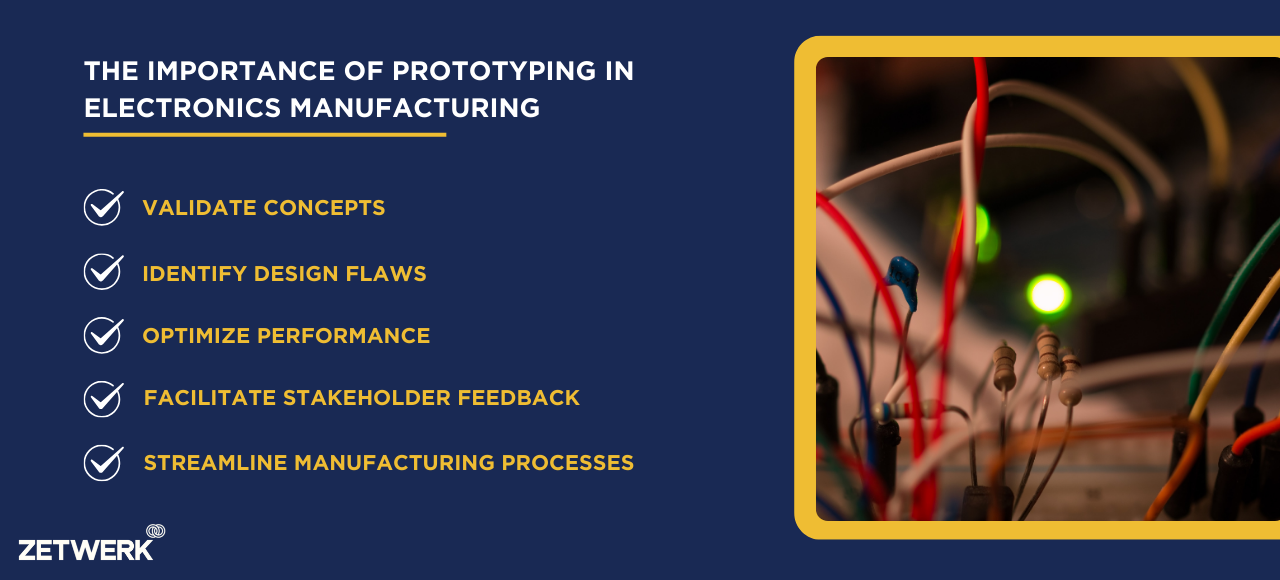
- Validate Concepts: Prototypes provide a tangible representation of a product idea, helping stakeholders assess its viability.
- Identify Design Flaws: Testing a prototype can reveal potential issues early, saving costs and time during later production stages.
- Optimize Performance: Iterative prototyping enables fine-tuning of functionality and performance.
- Facilitate Stakeholder Feedback: Early-stage prototypes help gather feedback from customers, engineers, and other stakeholders, ensuring alignment with requirements.
- Streamline Manufacturing Processes: By identifying potential manufacturing challenges, prototypes pave the way for smoother production workflows.
Benefits of Prototype Design Services
In the fast-evolving electronics industry, where innovation and speed to market are critical, prototype design services play a pivotal role. Here’s how leveraging these services benefits electronics manufacturers:
1. Accelerated Product Development
Prototype design services enable manufacturers to rapidly convert concepts into tangible models. This reduces the overall product development cycle, allowing companies to bring innovations to market faster. Quick iterations and refinements during the prototype phase eliminate delays in final production.
2. Cost-Effective Problem Identification
Building a prototype helps identify design flaws and functionality issues early in the development process. This proactive approach minimizes costly rework during mass production and reduces the risk of product recalls, ensuring a smoother manufacturing process.
3. Enhanced Customization
Prototyping allows for tailored designs that meet specific customer or market demands. Customization in the prototype stage ensures the final product aligns perfectly with user requirements and industry standards, enhancing customer satisfaction.
4. Improved Testing and Validation
Prototypes serve as functional models to test the product’s performance under real-world conditions. Manufacturers can validate key attributes such as durability, efficiency, and compliance with regulatory standards before scaling production.
5. Risk Mitigation
Developing a prototype helps mitigate risks associated with large-scale production. It allows manufacturers to evaluate materials, components, and processes, ensuring the final product is optimized for manufacturing, cost-efficiency, and quality.
6. Facilitates Stakeholder Buy-In
A tangible prototype is a powerful tool for demonstrating product potential to investors, clients, and internal teams. It provides a clear, visual representation of the product’s design and functionality, building confidence among stakeholders.
7. Supports Innovation
Prototyping encourages experimentation and creativity. Engineers and designers can test multiple configurations, explore alternative materials, and integrate advanced features without committing to full production, fostering innovation in electronics manufacturing.
8. Streamlined Transition to Mass Production
By ironing out design and production challenges during the prototype phase, manufacturers can ensure a seamless transition to mass production. This reduces downtime and enhances overall efficiency, ensuring the product meets market demands promptly.
Types of Prototypes in Electronics Manufacturing
1. Proof-of-Concept Prototypes
These prototypes demonstrate the feasibility of a concept or technology. They focus on core functionalities rather than aesthetics.
2. Functional Prototypes
Functional prototypes replicate the performance and behavior of the final product. They are essential for rigorous testing and validation.
3. Visual Prototypes
These prototypes focus on the product’s appearance and ergonomics, providing a realistic representation of its design.
4. Pre-Production Prototypes
These are near-final prototypes that incorporate all design and manufacturing specifications. They are used to finalize production workflows and tooling.
Best Practices for Effective Prototype Design
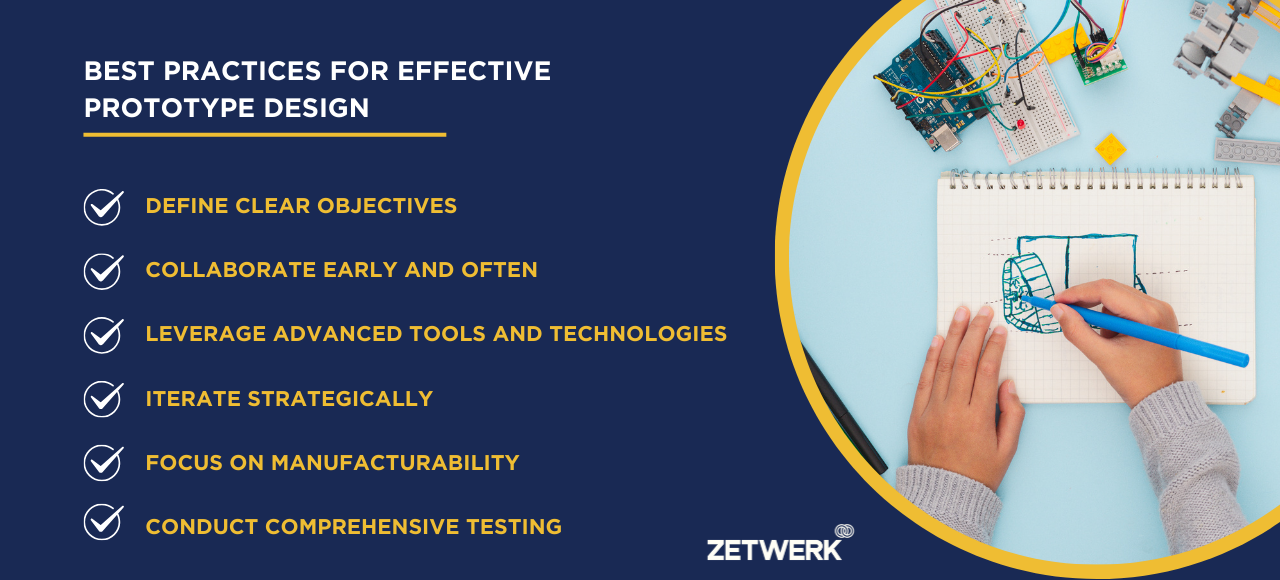
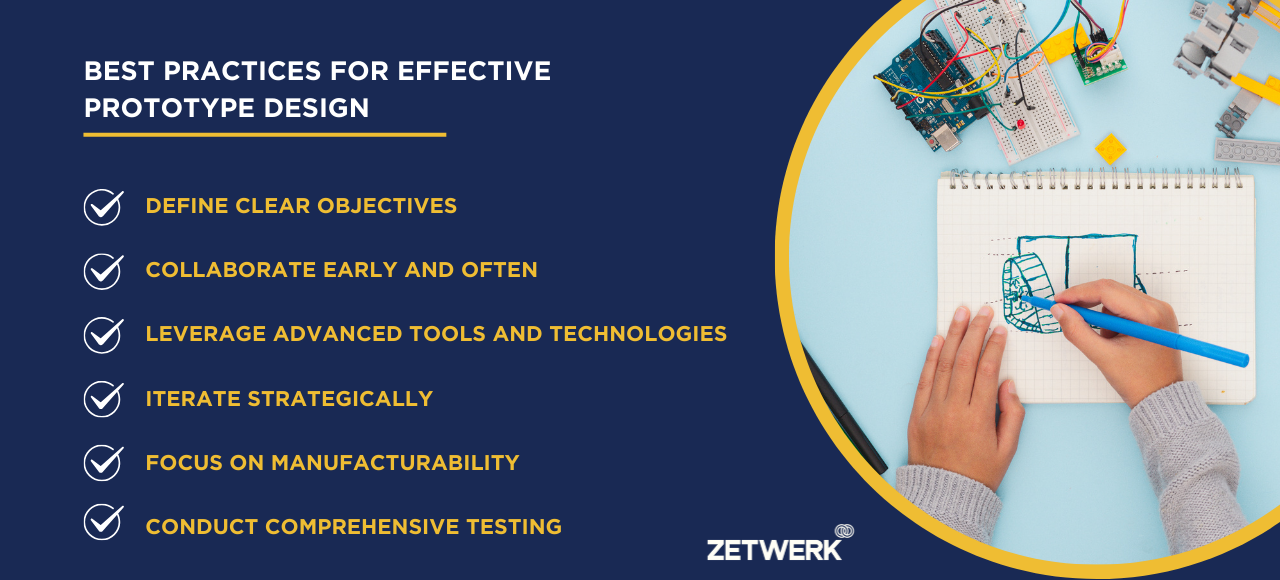
1. Define Clear Objectives
Identify the goals of the prototype—whether it’s to test functionality, validate a concept, or refine aesthetics. Clear objectives guide the design process and ensure resource efficiency.
2. Collaborate Early and Often
Engage cross-functional teams, including engineers, designers, and supply chain managers, early in the prototyping process. Regular collaboration ensures alignment and reduces the risk of miscommunication.
3. Leverage Advanced Tools and Technologies
Utilize tools such as CAD software, simulation platforms, and rapid prototyping technologies to enhance precision and speed.
4. Iterate Strategically
Adopt an iterative approach, refining the prototype based on feedback and testing. Each iteration should bring the design closer to the final product.
5. Focus on Manufacturability
Design with manufacturing in mind. Ensure that the prototype can be scaled efficiently and cost-effectively.
6. Conduct Comprehensive Testing
Test the prototype under various conditions to evaluate performance, durability, and compliance with industry standards.
The Role of Prototype Design in Industry 4.0
As electronics manufacturing embraces Industry 4.0, prototype design services are evolving to integrate smart technologies. Features like digital twins, IoT-enabled testing, and AI-driven design optimization are enhancing the prototyping process. These advancements enable real-time monitoring, predictive analysis, and seamless transitions from design to production.
Conclusion
Prototype design services are an indispensable part of electronics manufacturing, bridging the gap between ideas and reality. By adopting best practices and leveraging advanced tools, businesses can maximize the benefits of prototyping, ensuring faster time-to-market, cost efficiency, and superior product quality. In an era of rapid technological advancements, effective prototyping is not just an advantage—it is a necessity for staying competitive.



FAQs
A. Prototyping bridges the gap between design and production, allowing manufacturers to validate concepts, identify flaws, optimize performance, and ensure manufacturability.
A. Testing ensures that prototypes meet performance, durability, and quality standards. It identifies potential flaws or areas for improvement, enabling engineers to refine the design before mass production, minimizing defects and ensuring customer satisfaction.