Surface Mount Technology (SMT) assembly is a game-changing method in the electronics manufacturing industry. Unlike traditional through-hole techniques, SMT allows for smaller, more efficient, and cost-effective production of Printed Circuit Boards (PCBs). By enabling components to be directly mounted onto the surface of the PCB, SMT assembly has transformed how electronic devices are designed and manufactured.
In this blog, we will explore the essentials of SMT assembly, its advantages, and its role in revolutionizing PCB production processes.
What is SMT Assembly?
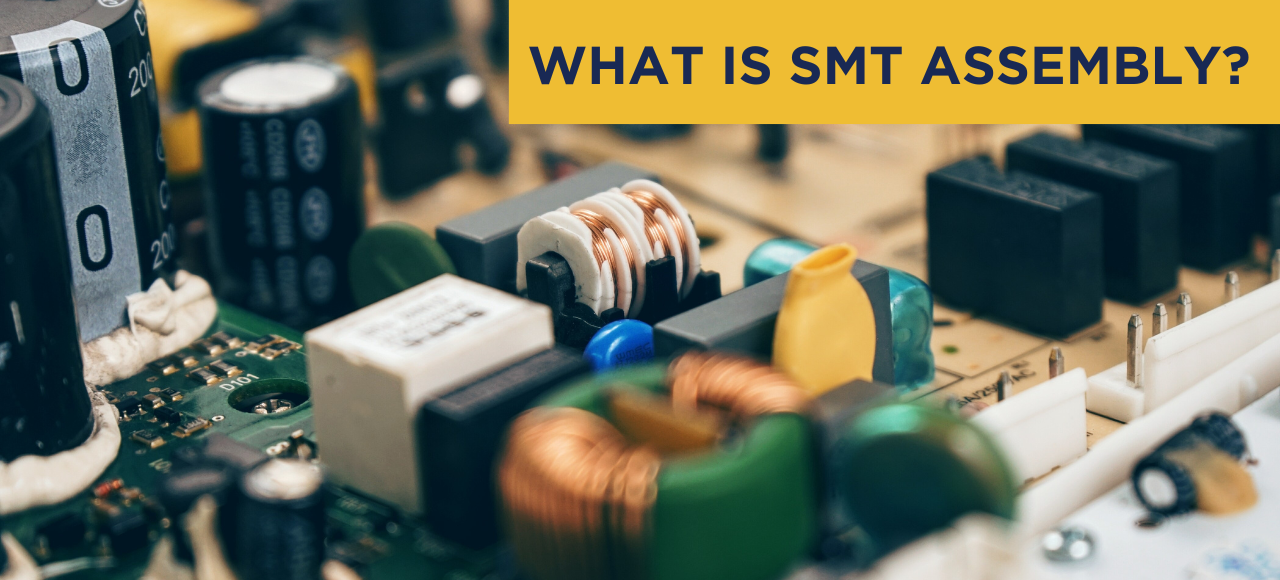
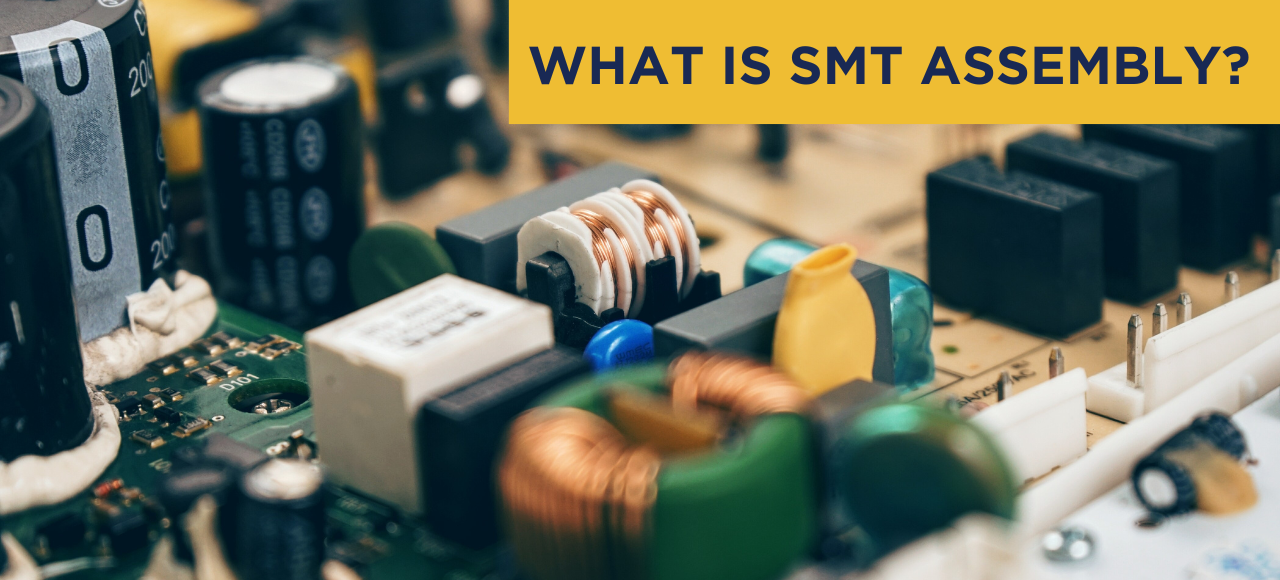
SMT assembly is a method used to mount electronic components, also known as Surface Mount Devices (SMDs), directly onto the surface of a PCB. This contrasts with the older through-hole method, where component leads are inserted into drilled holes on the PCB and soldered.
The SMT process involves the following steps:
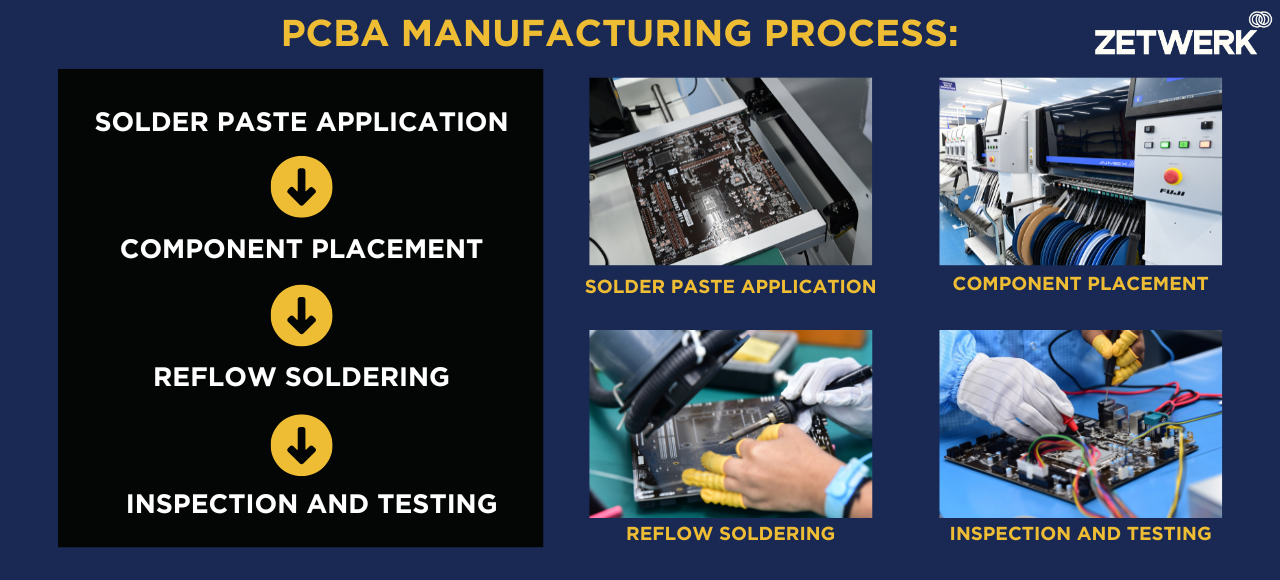
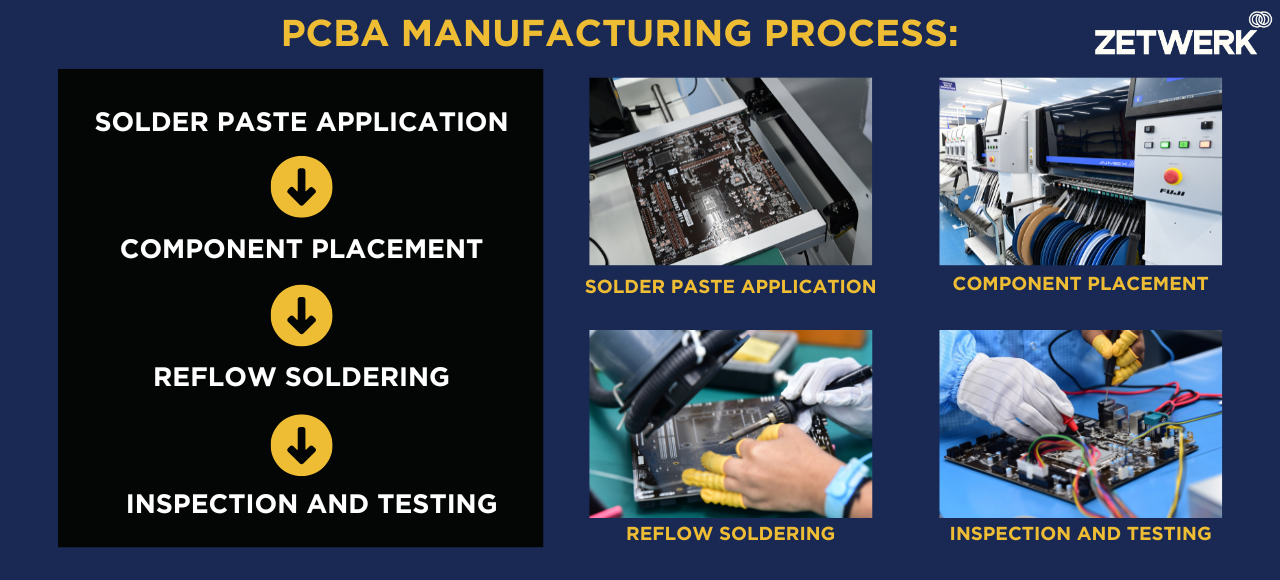
- Solder Paste Application: A stencil applies solder paste onto specific areas of the PCB.
- Component Placement: Robotic pick-and-place machines precisely position components onto the solder paste.
- Reflow Soldering: The PCB passes through a reflow oven, where the solder paste melts and creates secure connections.
- Inspection and Testing: Automated optical inspection (AOI) and functional testing ensure the assembly meets quality standards.
Advantages of SMT Assembly
The widespread adoption of SMT assembly is due to its numerous advantages:
1. Compact Design
SMT allows for the use of smaller components, enabling more compact PCB designs. This is critical for modern devices like smartphones, wearables, and IoT devices.
2. Increased Component Density
By mounting components on both sides of the PCB, SMT significantly increases the number of components that can fit on a single board.
3. Faster Production
SMT assembly is highly automated, making it faster and more efficient than manual or semi-automated through-hole assembly processes.
4. Cost-Effective
Automation reduces labor costs, and the smaller size of SMDs leads to material savings.
5. Improved Performance
The shorter leads of SMDs minimize parasitic capacitance and inductance, improving the electrical performance of the PCB.
6. Greater Design Flexibility
With no need for drilled holes, designers have more freedom to create innovative PCB layouts.
SMT vs. Through-Hole Technology
While SMT has largely replaced through-hole technology, the latter is still used for certain applications. Here’s a quick comparison:
Aspect | SMT Assembly | Through-Hole Technology |
Component Size | Smaller, lighter components | Larger components |
Production Speed | Faster due to automation | Slower due to manual assembly |
Reliability | Ideal for low-impact environments | Better for high-impact environments |
Applications | Consumer electronics, IoT devices | Aerospace, automotive, industrial |
Applications of SMT Assembly
SMT assembly is a cornerstone in the production of modern electronics. Its applications span across industries:
- Consumer Electronics: Smartphones, tablets, wearables, and smart home devices.
- Automotive: Advanced driver-assistance systems (ADAS), infotainment systems, and EV components.
- Medical Devices: Portable monitors, diagnostic tools, and implantable devices.
- Industrial Electronics: Sensors, controllers, and automation equipment.
- Telecommunications: Network infrastructure, routers, and IoT gateways.
Challenges in SMT Assembly
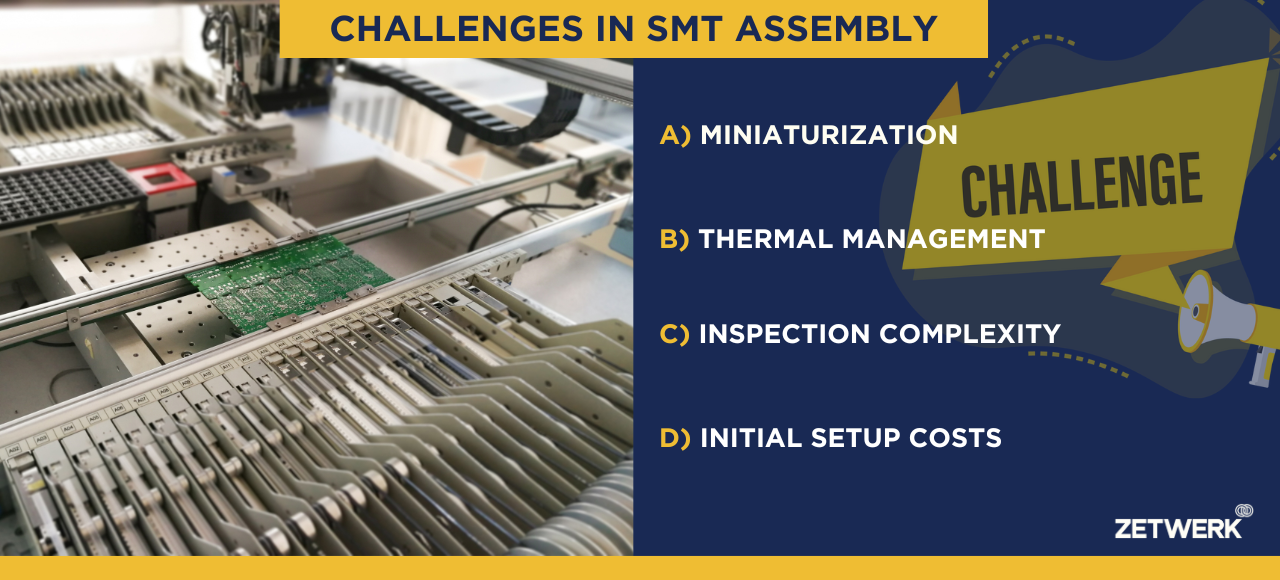
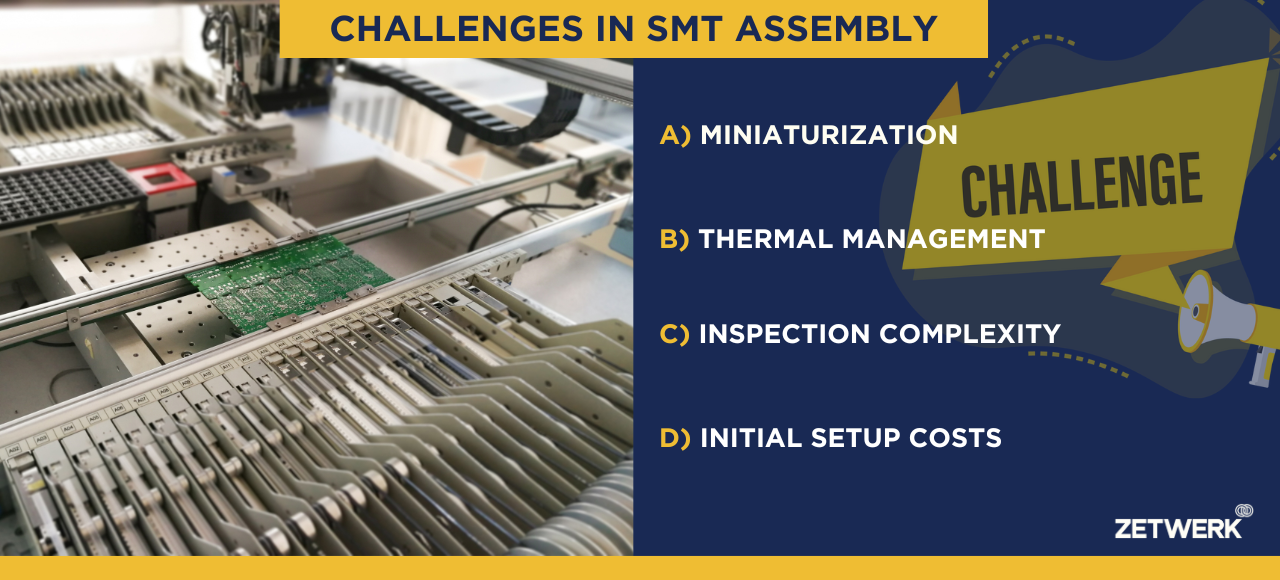
Despite its advantages, SMT assembly comes with challenges:
1. Miniaturization
As components get smaller, the precision required in placement and soldering increases.
2. Thermal Management
Reflow soldering can expose sensitive components to high temperatures, requiring careful thermal profiling.
3. Inspection Complexity
The high density of components makes inspection and testing more challenging, necessitating advanced AOI systems.
4. Initial Setup Costs
Investing in SMT equipment can be expensive, making it a barrier for smaller manufacturers.
How SMT Revolutionizes PCB Production
SMT assembly has transformed PCB production in several ways:
- Scalability: The automation of SMT assembly allows for rapid scaling of production volumes, meeting the demands of mass-market electronics.
- Innovation: By enabling smaller and more complex designs, SMT fuels innovation in miniaturized electronics.
- Quality Assurance: Advanced inspection techniques ensure consistent quality, even at high production speeds.
- Sustainability: SMT assembly uses fewer raw materials, contributing to more sustainable manufacturing processes.
Zetwerk: Your Partner in SMT Assembly
As a global leader in manufacturing solutions, Zetwerk offers comprehensive SMT assembly services to meet the needs of modern electronics manufacturers. With cutting-edge facilities and a focus on precision, Zetwerk ensures seamless integration of SMT into your production processes.
Why Choose Zetwerk for SMT Assembly?
- State-of-the-Art Equipment: Advanced pick-and-place and reflow soldering technologies.
- Global Manufacturing Capabilities: Facilities in India, Vietnam, and other strategic locations for cost optimization.
- Quality Assurance: Rigorous inspection and testing processes to guarantee high-quality PCBs.
- Flexible Production: Support for both prototyping and large-scale production.
Zetwerk’s expertise in SMT assembly helps businesses bring innovative products to market faster, with the assurance of exceptional quality and competitive pricing.
Conclusion
SMT assembly has revolutionized PCB production by enabling faster, smaller, and more efficient manufacturing processes. From consumer electronics to industrial applications, SMT continues to drive advancements in the electronics industry.
Partnering with a trusted provider like Zetwerk ensures you leverage the full potential of SMT assembly, optimizing your production processes and achieving a competitive edge. Contact Zetwerk today to explore how their SMT solutions can transform your electronics manufacturing journey.



FAQs
A. SMT (Surface Mount Technology) refers to the process of mounting components, while SMD (Surface Mount Device) refers to the components themselves that are mounted on the PCB.
A. SMT is ideal for small and lightweight components. However, larger components or those requiring stronger mechanical connections may still require through-hole technology.
A. Partner with a reliable manufacturer like Zetwerk that uses advanced inspection techniques such as Automated Optical Inspection (AOI) and X-ray inspection to ensure quality and precision.
Contact Us
Contact us today to discuss your project requirements and discover how we can help you achieve your goals efficiently and effectively.