In the rapidly evolving world of electronics, innovation demands speed, precision, and reliability. Printed Circuit Board (PCB) assembly is at the heart of this process, forming the foundation for next-generation devices that shape industries such as IoT, automotive, telecommunications, and consumer electronics.
Streamlined PCB assembly processes are essential for accelerating the development of cutting-edge designs while maintaining quality and cost efficiency. This blog explores how streamlined PCB assembly drives next-gen electronics and what manufacturers can do to stay ahead in the competitive market.
The Importance of Streamlined PCB Assembly
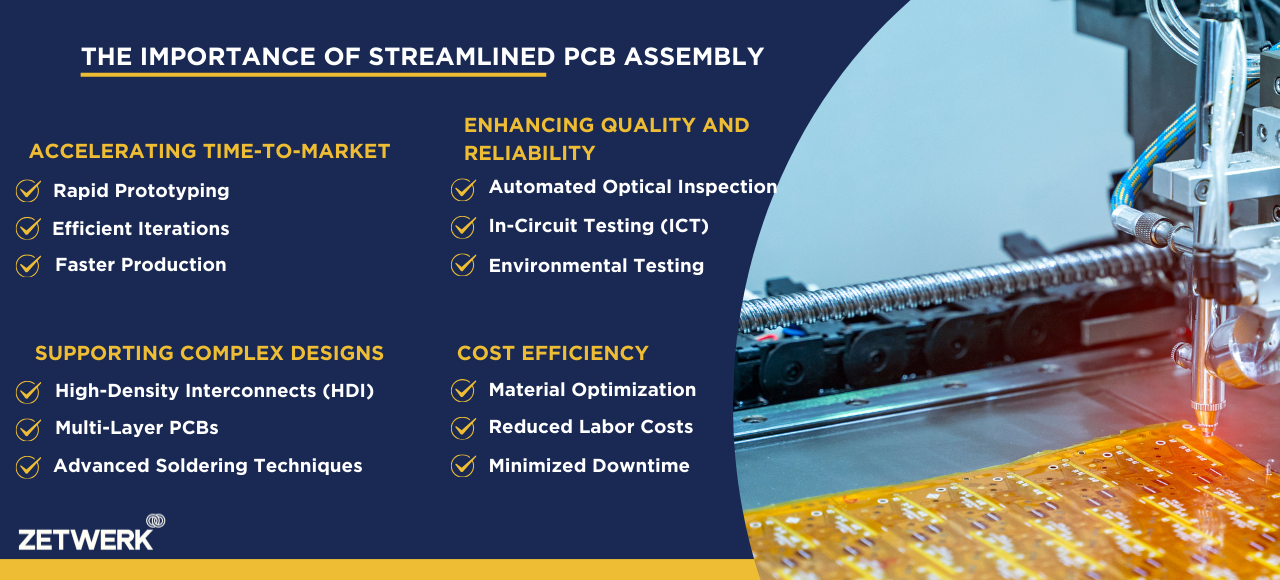
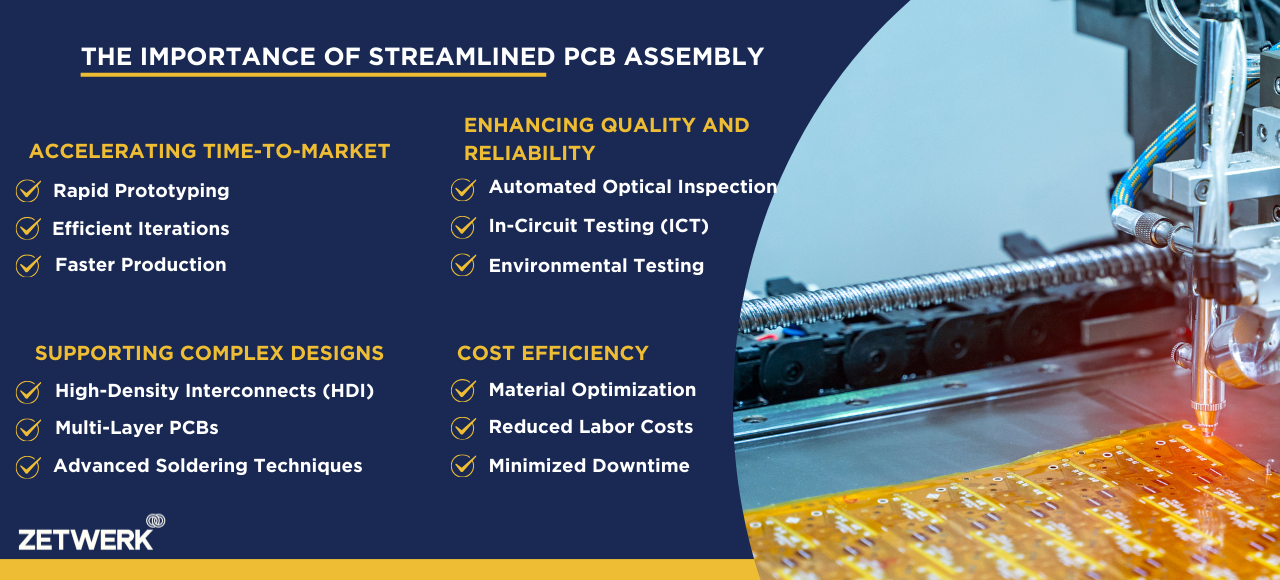
1. Accelerating Time-to-Market
In a competitive landscape, speed is critical. A streamlined PCB assembly process minimizes production timelines by integrating advanced automation, optimized workflows, and efficient resource allocation.
– Rapid Prototyping: Quickly transitioning from design to physical prototypes.
– Efficient Iterations: Reducing delays in implementing design changes.
– Faster Production: High-speed assembly lines enable swift scaling for mass production.
2. Supporting Complex Designs
As electronic devices become more advanced, their PCBs require intricate designs with high component density, multi-layer configurations, and fine-pitch placements. Streamlined assembly ensures precision and reliability even for the most complex designs.
– High-Density Interconnects (HDI): Compact designs for modern electronics.
– Multi-Layer PCBs: Supporting sophisticated functionality in compact spaces.
– Advanced Soldering Techniques: Reflow and wave soldering for flawless connections.
3. Enhancing Quality and Reliability
Streamlined processes incorporate robust quality control measures to ensure defect-free assemblies. Automation and real-time monitoring reduce human error and enhance product reliability.
– Automated Optical Inspection (AOI): Ensures precision in component placement.
– In-Circuit Testing (ICT): Validates electrical performance of the assembly.
– Environmental Testing: Simulates real-world conditions to ensure durability.
4. Cost Efficiency
By optimizing workflows, material usage, and production schedules, streamlined PCB assembly significantly reduces costs. Efficient processes also minimize waste and lower the likelihood of rework.
– Material Optimization: Accurate component sourcing and usage.
– Reduced Labor Costs: Automation reduces dependency on manual labor.
– Minimized Downtime: Predictive maintenance ensures consistent production.
Key Elements of Streamlined PCB Assembly
1. Advanced Manufacturing Equipment
Modern PCB assembly relies on high-speed pick-and-place machines, precise soldering systems, and cutting-edge testing tools. These technologies enable accurate, high-volume production with minimal errors.
2. Design for Manufacturability (DFM)
DFM is a critical step in ensuring streamlined production. By designing PCBs with manufacturing constraints in mind, potential issues can be identified and resolved early, saving time and costs during assembly.
– Optimized Layouts: Ensures compatibility with automated assembly lines.
– Material Selection: Uses cost-effective and durable materials.
– Assembly Feasibility: Accounts for manufacturing tolerances and limitations.
3. Automation and Real-Time Monitoring
Automation speeds up the assembly process while ensuring consistency. IoT-enabled monitoring systems track production in real time, identifying bottlenecks or defects early in the process.
4. Integration of Prototyping and Testing
Combining prototyping and testing into the assembly process allows for faster validation of designs, ensuring issues are addressed before full-scale production.
Industries Benefiting from Streamlined PCB Assembly
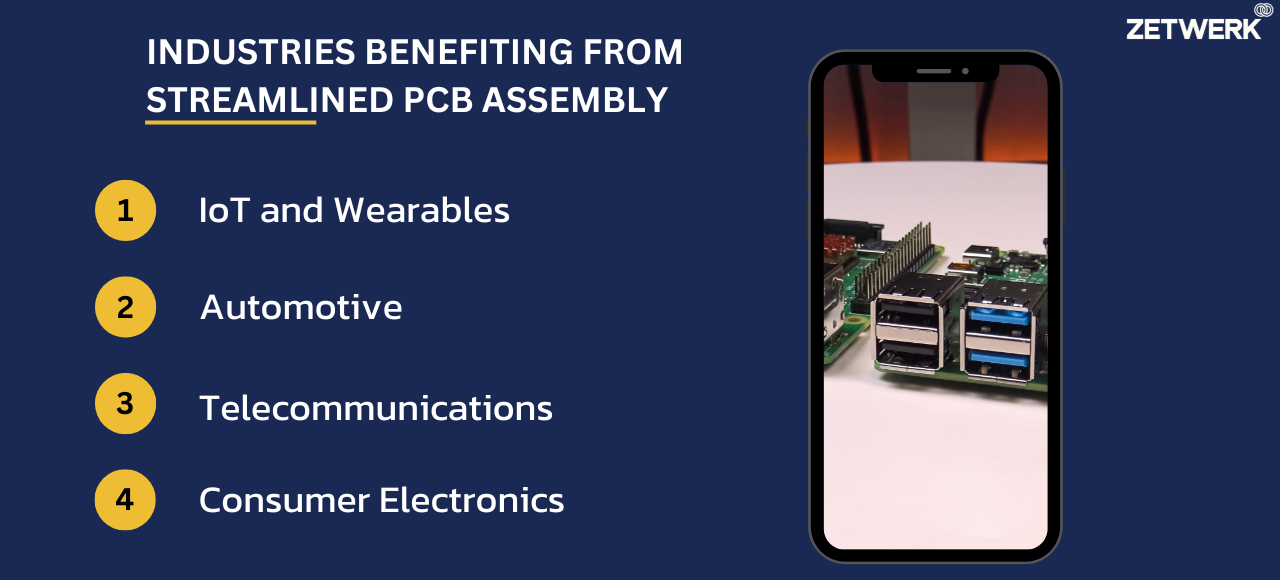
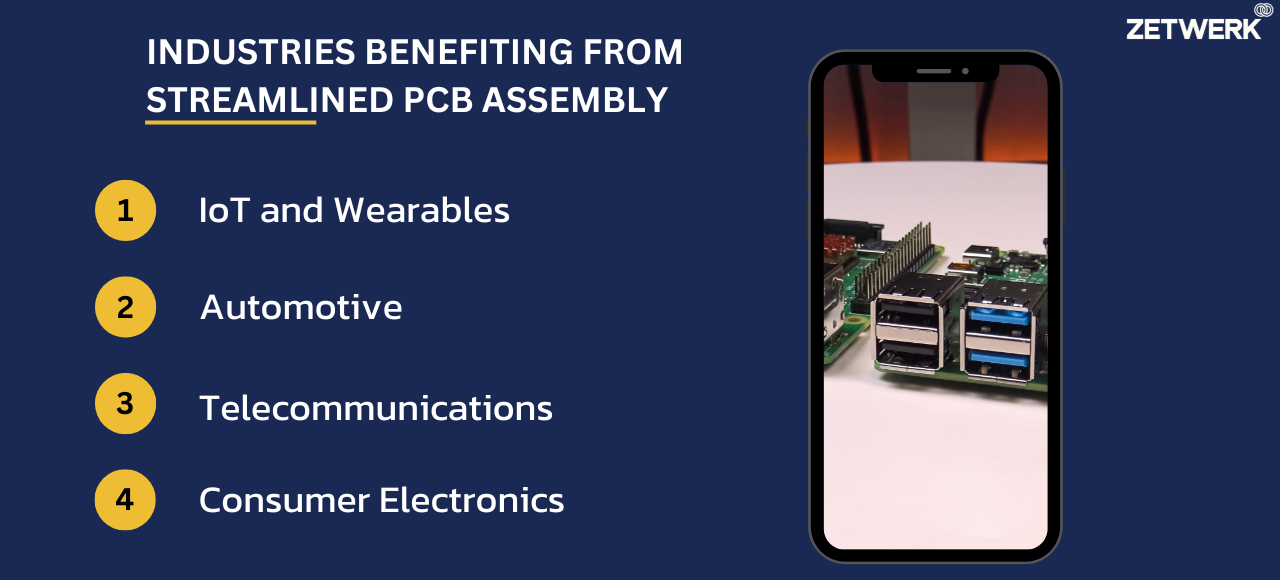
1. IoT and Wearables
Compact and efficient PCBs are critical for IoT devices and wearables, which demand high performance in small form factors.
2. Automotive
Advanced driver-assistance systems (ADAS), infotainment systems, and electric vehicle (EV) components require high-reliability PCBs.
3. Telecommunications
5G infrastructure and devices rely on high-frequency PCBs for seamless connectivity and signal processing.
4. Consumer Electronics
From smartphones to smart home devices, streamlined assembly ensures rapid production and consistent quality for high-demand products.
Why Choose Zetwerk Electronics for Streamlined PCB Assembly?
At Zetwerk Electronics, we specialize in delivering streamlined PCB assembly solutions tailored to next-gen electronics designs. With state-of-the-art facilities and a commitment to quality, we help our customers achieve faster time-to-market and superior product performance.
Our Advantages:
- Advanced Capabilities: High-speed SMT lines, AOI systems, and multi-layer assembly expertise.
- Global Reach: Facilities in India and Vietnam with local support in the U.S. and Mexico.
- End-to-End Solutions: From design support to assembly, testing, and logistics.
- Scalable Production: Adaptable to both small-batch prototypes and large-scale manufacturing.
- Commitment to Quality: Adherence to international standards like ISO 9001.
Conclusion
Streamlined PCB assembly is the key to achieving faster, more efficient production for next-gen electronics designs. At Zetwerk Electronics, we provide tailored solutions to help businesses innovate, scale, and succeed in a competitive market. Contact us today to learn more about our PCB assembly services.



FAQs
A. Streamlined PCB assembly leverages advanced automation, optimized workflows, and rapid prototyping capabilities. This reduces production timelines, enabling businesses to introduce products to market faster without compromising quality.
A. Industries like IoT, automotive, telecommunications, and consumer electronics benefit significantly from streamlined PCB assembly. These sectors require complex designs, fast production cycles, and reliable products to meet evolving market demands.
A. DFM ensures that PCBs are designed with manufacturing constraints in mind. This reduces production challenges, minimizes errors, and enhances overall efficiency by addressing potential issues early in the design phase.