Industry 4.0, often referred to as the Fourth Industrial Revolution, is reshaping how businesses operate, emphasizing interconnectedness, automation, real-time data, and smart manufacturing. At the core of this transformation are electronics manufacturing companies, serving as the backbone of technological advancement and enabling the seamless integration of cyber-physical systems.
The Role of Electronics Manufacturing in Industry 4.0
Electronics manufacturing companies play a pivotal role in Industry 4.0 by developing and producing the essential components that enable intelligent systems and advanced technologies. From sensors and microcontrollers to communication modules and IoT devices, these companies provide the building blocks for smart factories and connected ecosystems. Here are key areas where electronics manufacturers contribute:
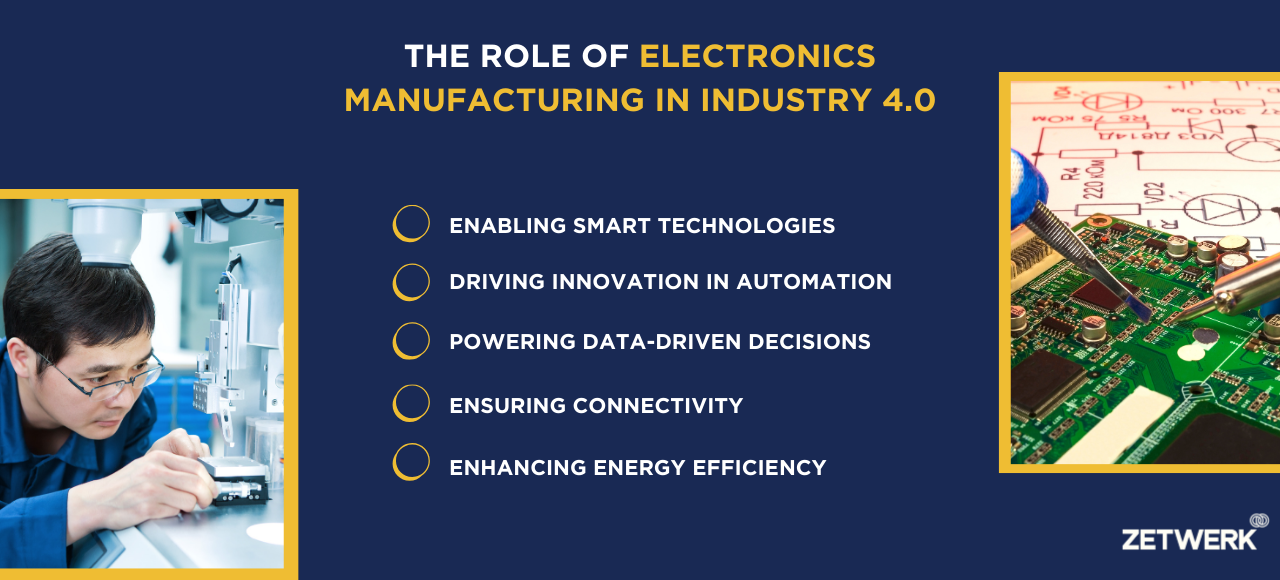
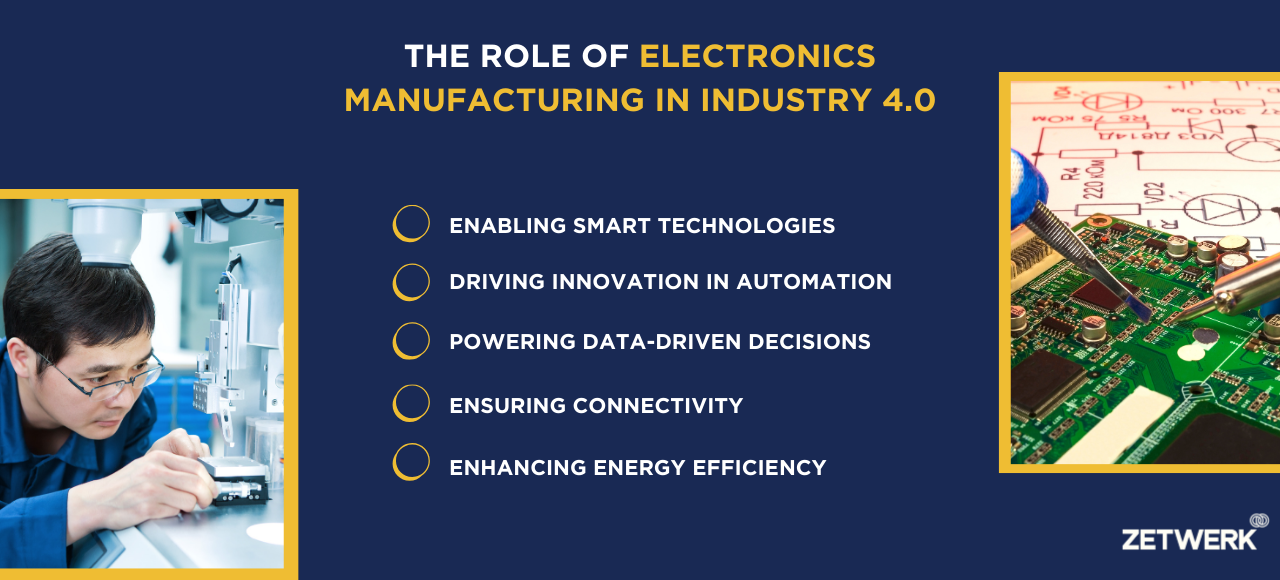
- Enabling Smart Technologies: Smart technologies rely on electronic components such as sensors, microprocessors, and IoT devices. Electronics manufacturers design and produce these components to ensure efficiency, reliability, and scalability in Industry 4.0 applications.
- Driving Innovation in Automation: Robotics and automation systems are critical to Industry 4.0. Electronics manufacturing companies supply the necessary components, such as actuators, controllers, and communication modules, to create efficient and autonomous systems.
- Powering Data-Driven Decisions: The collection, analysis, and utilization of data are at the heart of Industry 4.0. Electronics manufacturers provide hardware like edge devices, gateways, and communication systems that enable real-time data transfer and processing.
- Ensuring Connectivity: The seamless integration of devices and systems in Industry 4.0 depends on robust connectivity solutions. Electronics manufacturing companies deliver essential components like wireless modules, antennas, and network infrastructure to enable seamless communication.
- Enhancing Energy Efficiency: As sustainability becomes a critical focus, electronics manufacturing companies are at the forefront of producing energy-efficient components, such as power management ICs and energy harvesting modules, reducing the carbon footprint of industrial systems.
Importance of Quality and Customization
Quality and customization are non-negotiable for electronics manufacturing in the context of Industry 4.0. With the rise of complex, interconnected systems, businesses demand high-quality components tailored to their unique requirements. Electronics manufacturers must adhere to rigorous quality standards, such as ISO certifications, while offering flexible solutions to meet diverse industry needs.
Global Supply Chains and Tariff Mitigation
Electronics manufacturing companies operate in a globalized environment where supply chain efficiency is paramount. Many companies adopt strategies like manufacturing in low-cost regions, leveraging tariff-free zones, and establishing local assembly facilities to optimize costs. These measures not only ensure cost competitiveness but also reduce lead times, enhancing overall supply chain resilience.
Challenges Facing Electronics Manufacturers in Industry 4.0
While electronics manufacturers are critical to Industry 4.0, they face several challenges, including:
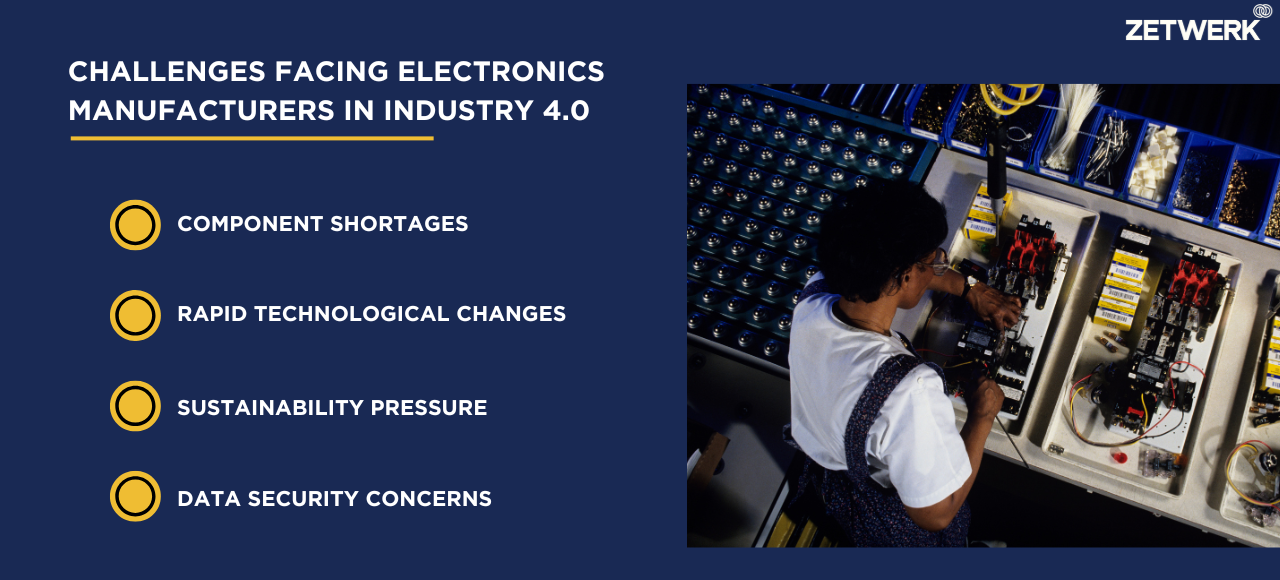
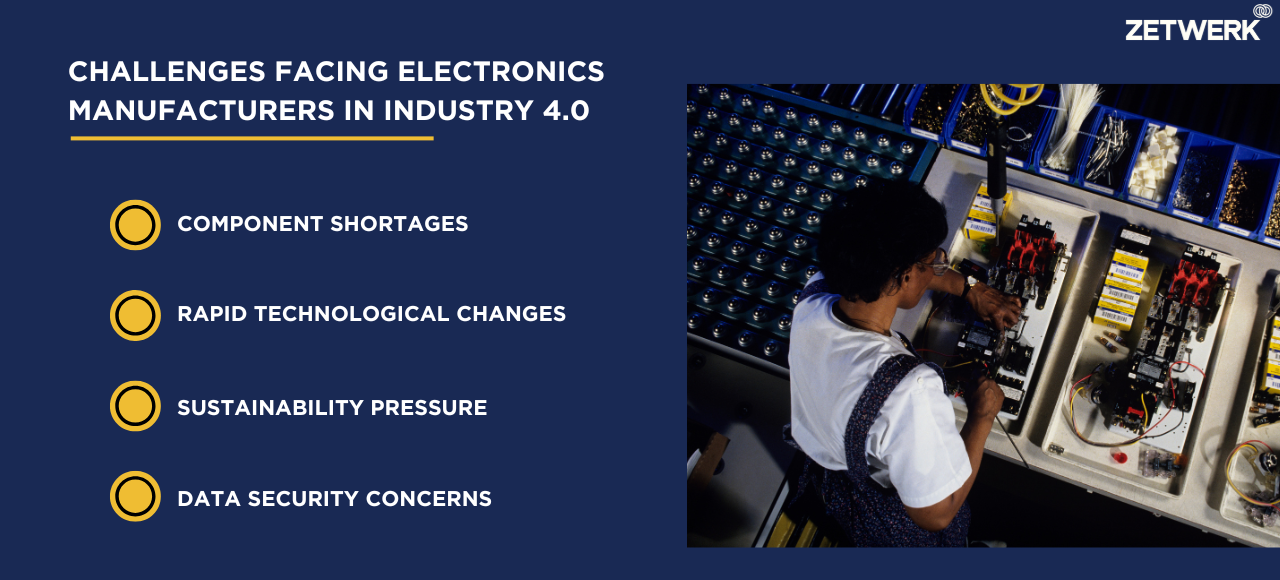
- Component Shortages: The global semiconductor shortage has highlighted the vulnerability of supply chains. Electronics manufacturers must adopt strategies to mitigate these risks, such as diversifying suppliers and adopting advanced inventory management systems.
- Rapid Technological Changes: The pace of technological evolution requires manufacturers to continuously innovate and invest in R&D to stay competitive.
- Sustainability Pressure: With increasing emphasis on sustainability, electronics manufacturers must adopt eco-friendly practices, including recycling programs and reducing hazardous material usage.
- Data Security Concerns: As connectivity increases, so does the risk of cyber threats. Electronics manufacturers must prioritize cybersecurity in their products to protect sensitive data and systems.
Key Strategies for Electronics Manufacturers
To stay relevant and thrive in Industry 4.0, electronics manufacturing companies can adopt the following strategies:
- Invest in Advanced Manufacturing Technologies: Embrace technologies like 3D printing, AI-driven automation, and advanced robotics to enhance productivity and reduce operational costs.
- Focus on Collaboration and Partnerships: Collaborate with technology providers, research institutions, and other stakeholders to drive innovation and develop cutting-edge solutions.
- Leverage Data Analytics: Utilize big data and analytics to optimize manufacturing processes, predict maintenance needs, and improve overall efficiency.
- Prioritize Workforce Development: Equip employees with the skills required to operate and manage advanced systems, ensuring a smooth transition to Industry 4.0 practices.
- Adopt Sustainable Practices: Implement eco-friendly manufacturing processes, use recyclable materials, and reduce energy consumption to align with global sustainability goals.
The Future of Electronics Manufacturing in Industry 4.0
The role of electronics manufacturing companies in Industry 4.0 will continue to expand as technologies evolve. These companies are not just suppliers; they are strategic partners enabling businesses to embrace digital transformation and achieve operational excellence. By focusing on innovation, quality, and sustainability, electronics manufacturers will remain at the forefront of Industry 4.0, driving the next wave of industrial advancement.



FAQs
A. Electronics manufacturers produce a wide range of components critical to Industry 4.0, including sensors, microcontrollers, communication modules, edge devices, and power management ICs.
A. Companies mitigate supply chain challenges by diversifying manufacturing locations, adopting advanced inventory management systems like JIT (Just-In-Time), and leveraging technology for predictive supply chain analytics.
A. Electronics manufacturers are prioritizing sustainability by adopting green manufacturing practices, recycling electronic waste, reducing hazardous materials, and designing energy-efficient products.