In the fast-evolving world of electronics, wire assemblies form the backbone of countless devices and systems. Whether it’s a consumer gadget, industrial machinery, or aerospace application, wire assemblies ensure that electrical signals and power flow seamlessly. While the importance of wire assemblies is evident, what truly sets apart a quality wire assembly from an average one? Here, we’ll dive deep into the critical elements of wire assembly, industry best practices, and how quality impacts performance, reliability, and cost-efficiency.
Understanding Wire Assembly
Wire assembly, also known as cable harnessing, involves combining multiple wires or cables into a single unit, typically bound by connectors, terminals, and protective sheathing. These assemblies are designed to transmit electrical signals or power across systems efficiently.
Key Components of Wire Assemblies:
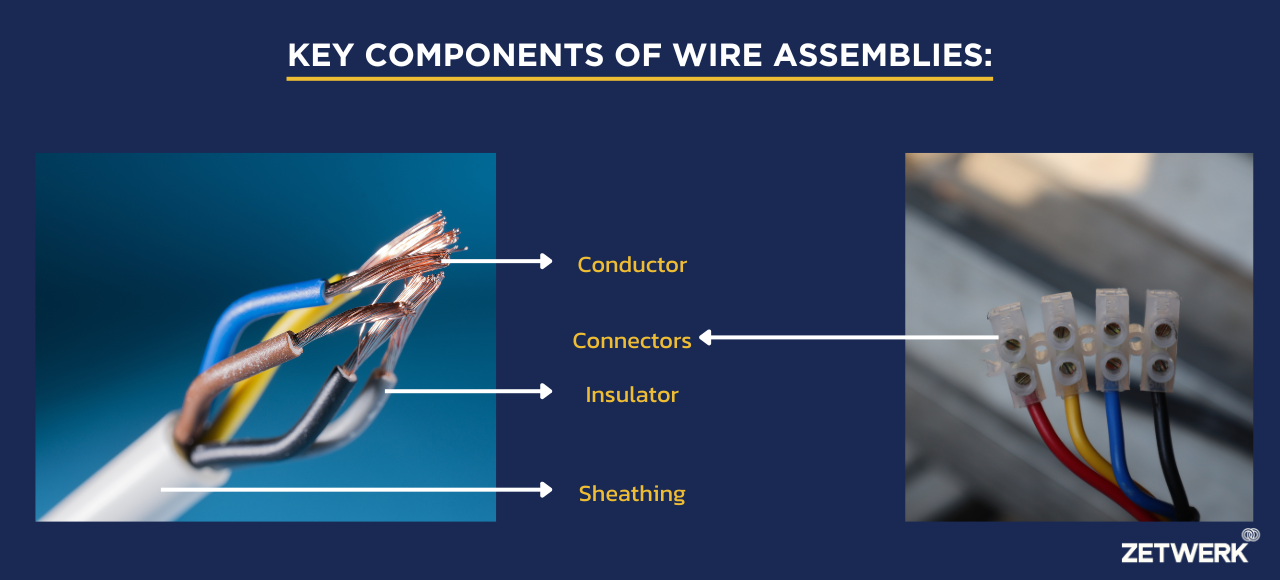
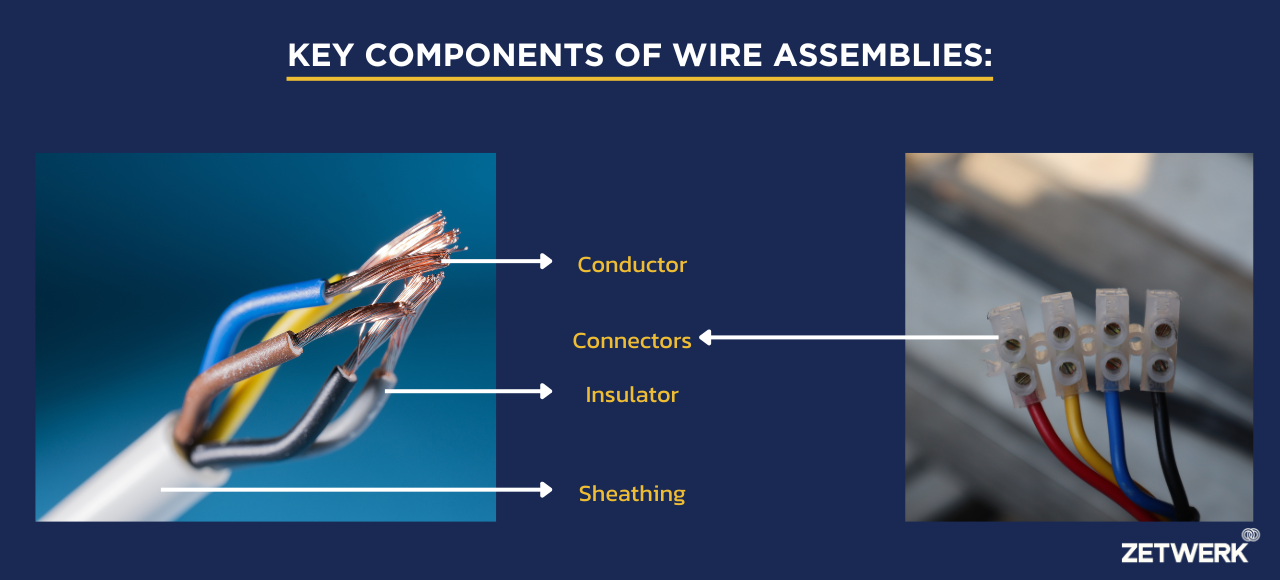
- Wires and Cables: The core conductors of electrical signals or power.
- Connectors: Interface points enabling connectivity.
- Terminals: Secure end points ensuring signal transmission.
- Sheathing: Protective covering for durability and safety.
Elements of High-Quality Wire Assemblies
When it comes to ensuring that wire assemblies meet stringent operational requirements, several factors come into play:
a) Material Selection
Using high-grade materials ensures durability and reliability. Conductors like copper or silver provide excellent conductivity, while protective sheathing materials, such as PVC or Teflon, resist environmental factors like moisture, heat, and abrasion.
b) Precision Manufacturing
Quality wire assemblies are produced with high precision to match exact specifications. This includes cutting wires to the correct length, stripping insulation accurately, and ensuring tight crimping of connectors and terminals. Advanced automation tools play a crucial role in maintaining consistency and precision.
c) Testing and Validation
Testing is a cornerstone of quality assurance. Common tests for wire assemblies include:
- Continuity Testing: Ensures there are no breaks in the electrical connection.
- High-Pot Testing: Verifies insulation strength under high voltage.
- Pull Testing: Confirms the mechanical integrity of terminals and connectors.
d) Customization Capabilities
Every application has unique needs. A superior wire assembly provider offers customization options, such as specific lengths, unique connector configurations, and compatibility with specialized equipment.
e) Compliance and Certifications
Meeting industry standards, such as IPC/WHMA-A-620 for wire harnesses, ensures that assemblies adhere to recognized quality benchmarks. Certifications also ensure compatibility with industries like automotive, aerospace, and healthcare.
Key Challenges in Wire Assembly Manufacturing
a) Design Complexity
Modern devices demand compact, lightweight, and multifunctional assemblies. Managing the complexity of designs without compromising on performance is a challenge requiring expertise and innovation.
b) Global Supply Chain Disruptions
Supply chain challenges can lead to delays in sourcing essential materials, affecting production timelines. Partnering with globally integrated manufacturers can mitigate such risks.
c) Quality Consistency
Maintaining uniformity across high-volume production requires advanced automation and robust quality control protocols.
Benefits of High-Quality Wire Assemblies
Investing in superior wire assemblies offers long-term benefits:
- Enhanced Performance: Reliable signal transmission reduces system failures.
- Longevity: Durable materials extend the lifespan of assemblies in challenging environments.
- Safety: Proper insulation and robust connectors prevent electrical hazards.
- Cost Savings: Reduced downtime and maintenance translate to lower operational costs.
Best Practices for Ensuring Quality in Wire Assemblies
a) Partner with Experienced Manufacturers
Choosing a manufacturer with a proven track record ensures access to expertise, advanced technology, and adherence to quality standards.
b) Leverage Automation
Automation minimizes human error and ensures consistency in processes like wire cutting, crimping, and assembly.
c) Rigorous Quality Control
Incorporating multi-stage testing—from raw material inspection to final assembly checks—guarantees that only the best assemblies reach customers.
d) Prototyping and Iteration
Before full-scale production, creating prototypes allows for testing and validation, ensuring that the assembly meets all requirements.
Applications of Wire Assemblies Across Industries
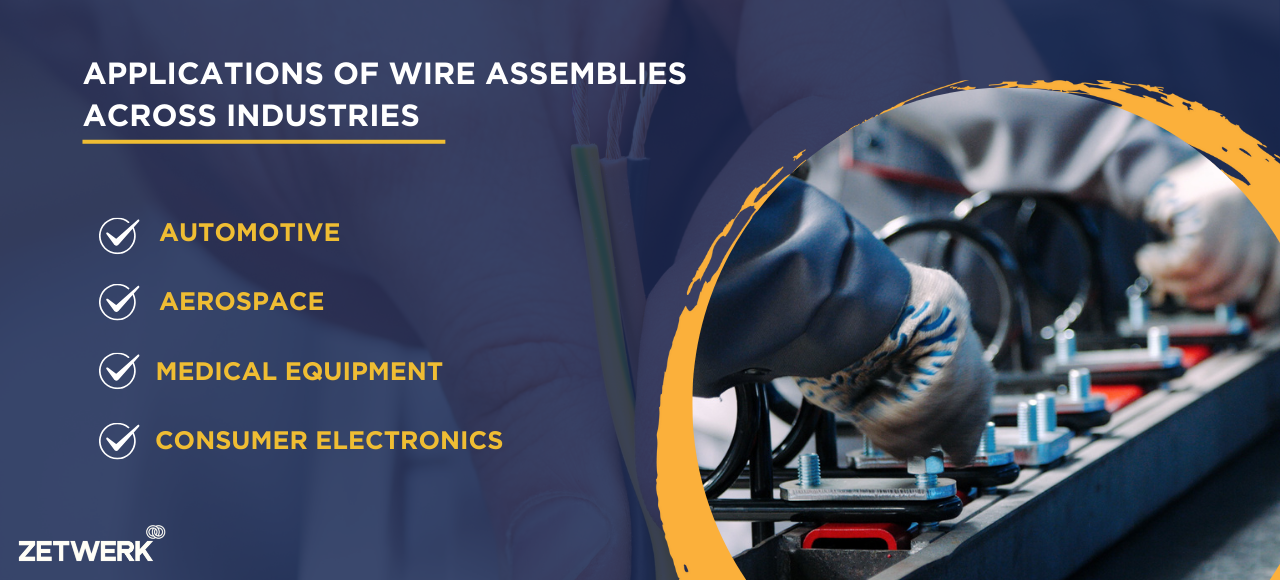
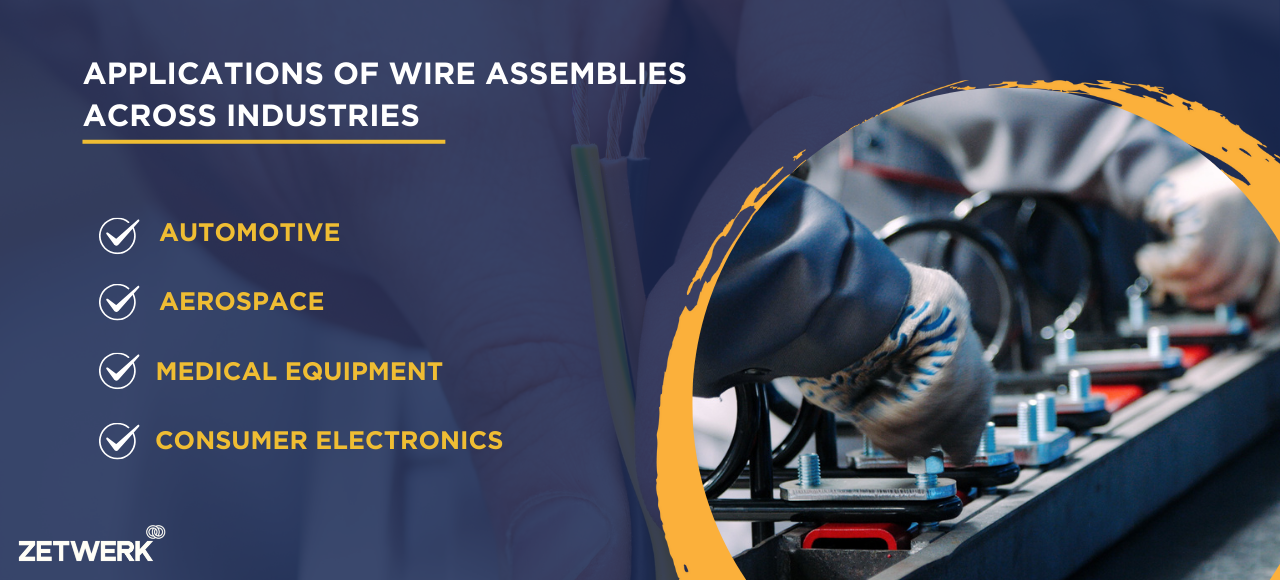
a) Automotive
Wire assemblies power essential systems such as engine controls, infotainment systems, and safety sensors.
b) Aerospace
Complex harnesses are used in avionics, navigation systems, and communication devices, where precision and reliability are critical.
c) Medical Equipment
From diagnostic machines to life-support systems, wire assemblies enable seamless operation of critical devices.
d) Consumer Electronics
Smartphones, laptops, and home appliances rely on compact, efficient wire assemblies to function optimally.
About Zetwerk Electronics
At Zetwerk, we understand the critical role of quality wire assemblies in driving technological advancements. With state-of-the-art manufacturing facilities and a commitment to excellence, Zetwerk Electronics delivers:
- Custom Solutions: Tailored wire assemblies that meet unique application requirements.
- Global Supply Chain Integration: Leveraging facilities in India and Vietnam to provide cost-effective, tariff-free solutions.
- Strict Quality Assurance: Adherence to international standards like IPC/WHMA-A-620 ensures top-notch quality.
- On-Time Delivery: Advanced logistics systems guarantee timely delivery, reducing downtime for our partners.
Whether you’re in the automotive sector, aerospace, or consumer electronics, Zetwerk Electronics is your trusted partner for reliable, high-performance wire assemblies. Let’s power innovation together.



FAQs
A. Wire assemblies typically involve individual wires, while cable assemblies combine multiple wires within a protective sheath. Cable assemblies are often used for more complex or demanding applications.
A. Look for providers with strong industry expertise, advanced manufacturing capabilities, certifications, and a track record of delivering customized solutions on time.
A. Industries like automotive, aerospace, healthcare, and consumer electronics heavily depend on high-quality wire assemblies for reliable performance and safety.
Contact Us
Contact us today to discuss your project requirements and discover how we can help you achieve your goals efficiently and effectively.