Automotive forging parts are created with technology that has been refined over the years to make them more precise, cost-effective, and durable. These parts are used in automobiles to improve performance and longevity. Cars are becoming lighter and more efficient each day, but this was only achieved with the help of forging. It is vital for car performance and its ability to save on fuel. This article explores the overview of forging, commonly used materials, a few forging processes utilized to create forging auto parts, and the future of the automotive industry with forged components.
Know About Automotive Forging Parts : Materials & Processes
Zetwerk provides high-quality Forged Components and all secondary operations.
Submit the relevant part drawings, 3D files, and other information by clicking on the button below.





Overview Of Forging
Forging is a metalworking process that involves heating the metal and then shaping it into the desired shape using compressive force. The process can be done in a forge or furnace or by other means such as hammers, presses, hydraulics, or compressed air.
- Open die forging
- Closed die (Impression die) forging
- Roll forging
- Cold forging
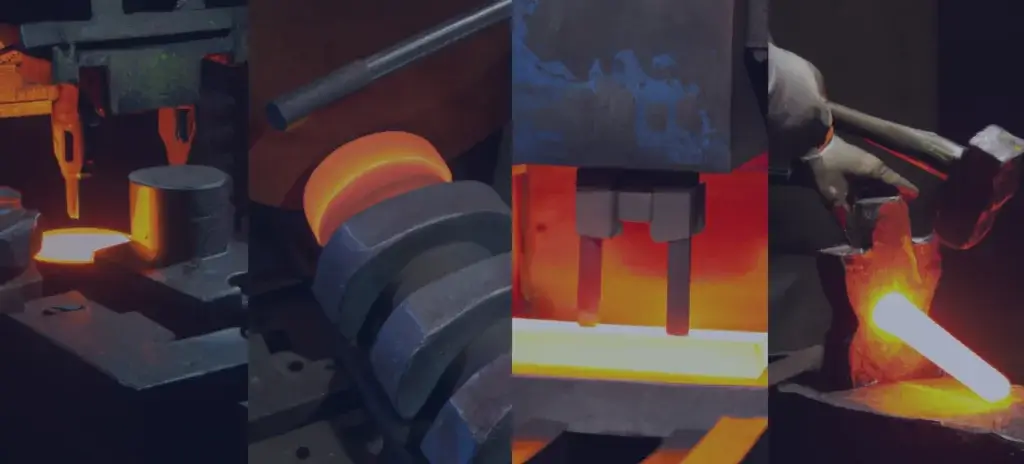
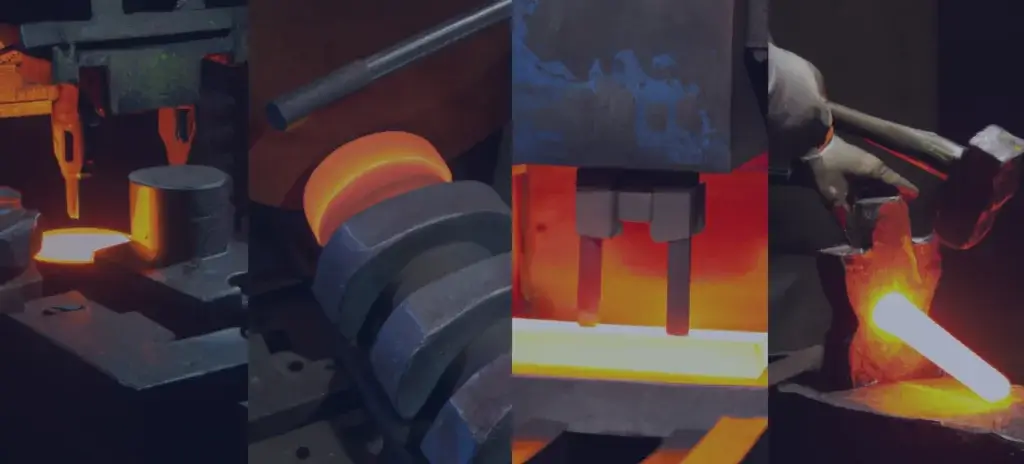
Forging’s Benefits
- Aligning the grain structure of the metal results in a stronger, more durable product
- Improved fatigue resistance
- Increased dimensional accuracy and consistency
- Improved surface finish
Applications Of Forging
- Automotive and aerospace components
- Hand and power tools
- Construction components
- Power generation and transmission components
- Medical devices
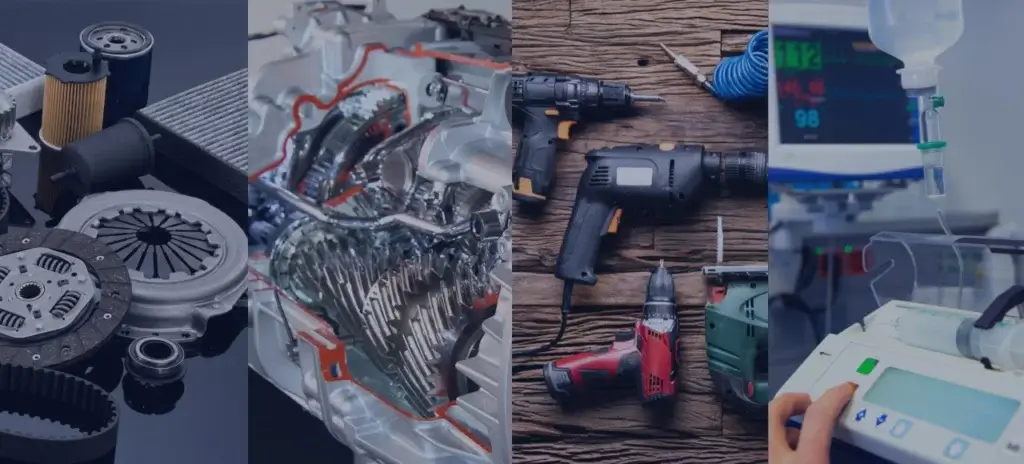
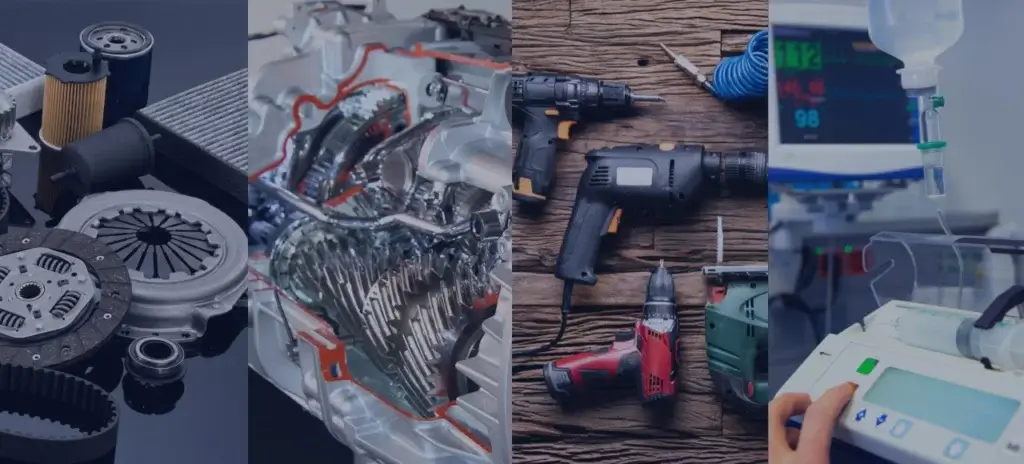
The Most Common Materials Used in Forging Auto Parts
A forging process transforms metals into auto parts under compressive force. Depending on what properties are required, this process can be performed on hot and cold materials. Forging auto parts includes engine parts such as connecting rods, crankshaft, pistons, injectors, and camshaft; chassis parts such as bearings and gears; axles, etc. Forged automotive components are used in many cars because they are strong, tough, and lightweight. Two of the most common materials used to manufacture forged automotive parts are aluminum and steel.
- Aluminum: It is gaining popularity in the automotive forging industry because lightweight vehicles are in high demand. Aluminum is an excellent material for forging auto parts because it provides increased strength, design flexibility, corrosion protection, and lower cost.
- Steel: The automotive industry uses steel in the construction of its vehicles because it is strong, widely available, and has high tensile strength. Car and truck manufacturers continue to rely on steel forging auto parts, which are integral to today’s vehicle designs. Forged steel parts can be found in both high- and low-volume models. These parts can make up over 250 different forgings, most of which are carbon or alloy steel.





Forging Process Used In Making Automotive Forging Parts
Different forging processes include drop (closed and open), press, upset, roll, and isothermal. Let’s see here the detailed view of two forging processes utilized in making forging auto parts.
Closed Die Forging Process : With a closed die process, however, the dies are attached to an anvil, and the hammer forces the molten metal into their cavities multiple times–or in some cases even hundreds of times-to create complex geometries. The high initial costs of forging make it more expensive to produce goods in small quantities. However, as production volumes increase, the forging process becomes more economical. Closed die forging offers exceptional strength compared to other methods of metal forming. It is used to produce automotive forging parts, tools, and other items that require high levels of precision.
Roll Forging : Roll forging is a way to make metal rods and wires longer. Manufacturers can create precisely shaped parts by placing heated rods between two grooved rollers, which rotate and shape the metal as pressure is maintained. The roll forging process eliminates flashing and produces a grain structure that is more favorable than other metal forging processes. Although roll forging uses rolls to create parts and components, it is still considered a metal forging process rather than a rolling process. Roll forging makes automotive parts and other tools, including knives.
Forged Parts: The Future Of Automotive Industry
Manufacturers use forged parts in their machines because of the strength and durability of these parts. To cater to the automotive industry’s needs, leading automotive forging parts manufacturers continuously develop new methods for advanced manufacturing forged components.
Forged parts offer car manufacturers several advantages over cast parts, such as:
- Forged parts can improve the vehicle’s strength, durability, and reliability.
- The ability to customize forged parts allows carmakers to create unique and innovative products that were not possible using cast parts.
- Cost-effectiveness is achieved through reduced raw material waste.
- Precise manufacturing of forged parts leads to enhanced performance.
- Forging components into automobiles allows manufacturers to create safer, more reliable vehicles with better fuel efficiency and performance.
- They weigh less which leads to better fuel efficiency.
Are you looking for the best-forged auto parts for your production and engineering needs? Look no further than Zetwerk, a leading provider of top-quality forging auto parts and components. Our products are manufactured to the highest quality and safety standards, ensuring reliable performance in any environment. We offer a wide selection of forged auto parts in different shapes and sizes, making it easy to find the right part for every application. With us, you can be sure you will get the best forged auto parts at competitive prices. Contact Zetwerk today to get started!




