Metal injection molding (MIM) has emerged as a game-changer in manufacturing. This innovative process offers a unique blend of benefits that traditional manufacturing methods often can’t match. However, like any technique, it comes with its challenges. In this article, we’ll delve deep into the metal injection molding advantages and disadvantages, providing a comprehensive overview for industry professionals.
Metal Injection Molding: An Overview
Metal injection molding combines the flexibility of plastic injection molding with the strength of powdered metals. It involves mixing metal powders with a binder material to create a ‘feedstock’ shaped using injection molding machines. Once molded, the parts undergo a process to remove the binder, followed by a high-temperature sintering phase that solidifies the metal, resulting in a fully dense component.
Advantages of Metal Injection Molding
- Complex Geometries and Intricate Designs: One of the standout advantages of MIM is its ability to produce parts with geometries that would be challenging or even impossible with other methods. This opens up new design possibilities for parts manufacturers.
- High-Production Volumes: MIM is well-suited for high-volume production runs, making it a cost-effective choice for mass-producing precision components.
- Superior Strength and Durability: The sintering process ensures that MIM parts have excellent mechanical properties, rivaling wrought materials.
- Material Diversity: A wide range of metals, including stainless steel, titanium, and specialty alloys, can be used in the MIM process, offering flexibility in material selection.
- Reduced Waste: Since the metal powders are used efficiently in the MIM process, minimal material wastage contributes to sustainable manufacturing practices.
Disadvantages of Metal Injection Molding
- Initial Cost: Setting up for MIM can be expensive, especially considering the cost of specialized equipment and tooling development.
- Limitations in Size: While MIM is excellent for producing small to medium-sized parts, there might be better choices for larger components.
- Post-Processing: Some MIM parts may require additional post-processing, such as machining or surface treatments, adding to the overall production time and cost.
- Lead Time: The combined steps of debinding and sintering can add to the lead time, especially when compared to processes like die casting.
- Material Limitations: While MIM offers a range of material choices, not all metals or alloys are suitable for the process.
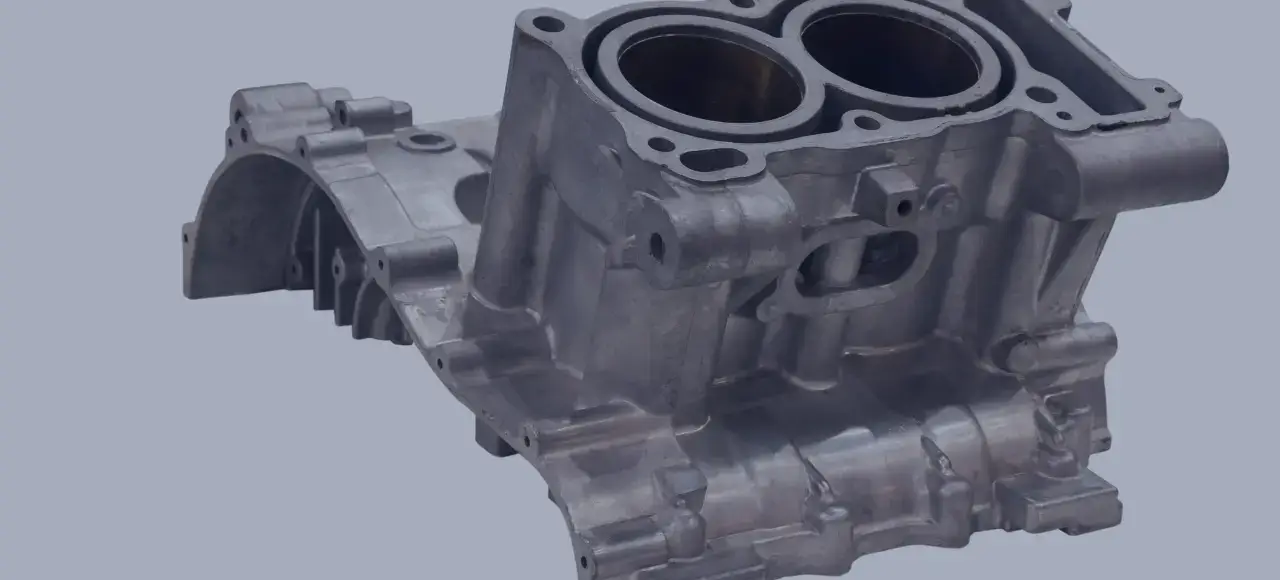
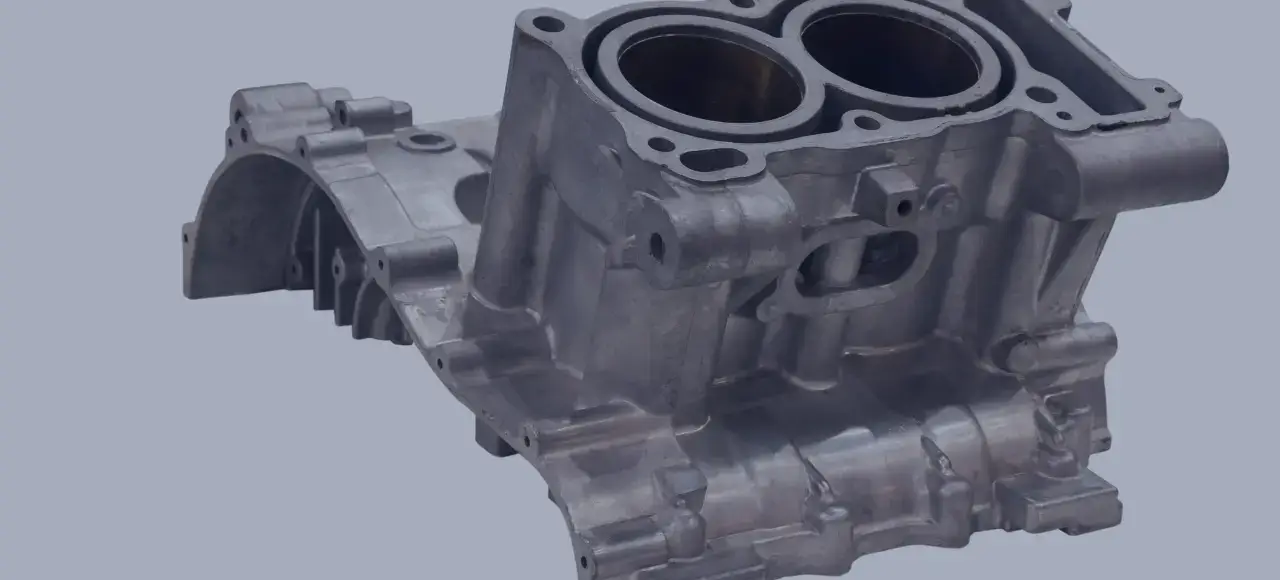
Applications of Metal Injection Molding
Given its unique capabilities, MIM has found applications across a plethora of industries:
- Consumer Electronics: Small, intricate components for gadgets, such as smartphones and laptops, can be efficiently produced using MIM.
- Medical: Surgical instruments, dental braces, and implantable devices, all of which require precision and durability, can be manufactured using MIM.
- Aerospace: The aerospace industry values MIM for its ability to produce lightweight, durable parts essential for aircraft performance.
- Automotive: Components like gears, levers, and connectors that need to withstand stress and wear benefit from MIM’s strength.
Challenges in Metal Injection Molding
While MIM offers numerous advantages, it’s not without its challenges:
- Tooling Costs: The molds used in MIM are often expensive, especially for intricate designs. This can increase the initial investment required.
- Material Constraints: Not all metals are suitable for MIM. Some metals may not sinter well, leading to parts with sub-optimal properties.
- Quality Control: Ensuring consistent quality can be challenging, mainly when producing parts with intricate designs or thin walls.
Factors Driving MIM’s Popularity
Several factors have contributed to the popularity of MIM:
- Technological Advancements: Modern machinery and software have enabled more precise control over the MIM process, ensuring consistent quality and reducing wastage.
- Economic Viability: As the demand for intricate parts increased, traditional manufacturing methods became less economically viable. With its ability to produce complex parts in bulk, MIM offered a cost-effective alternative.
- Sustainability: MIM’s efficient use of materials and reduced waste production make it an environmentally friendly option.
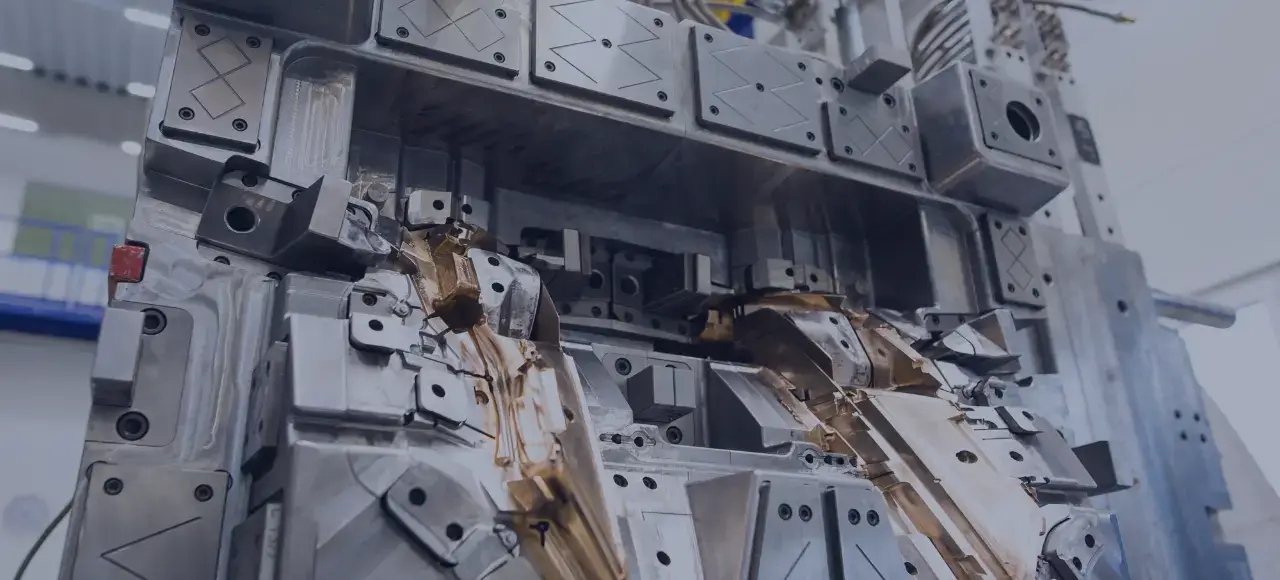
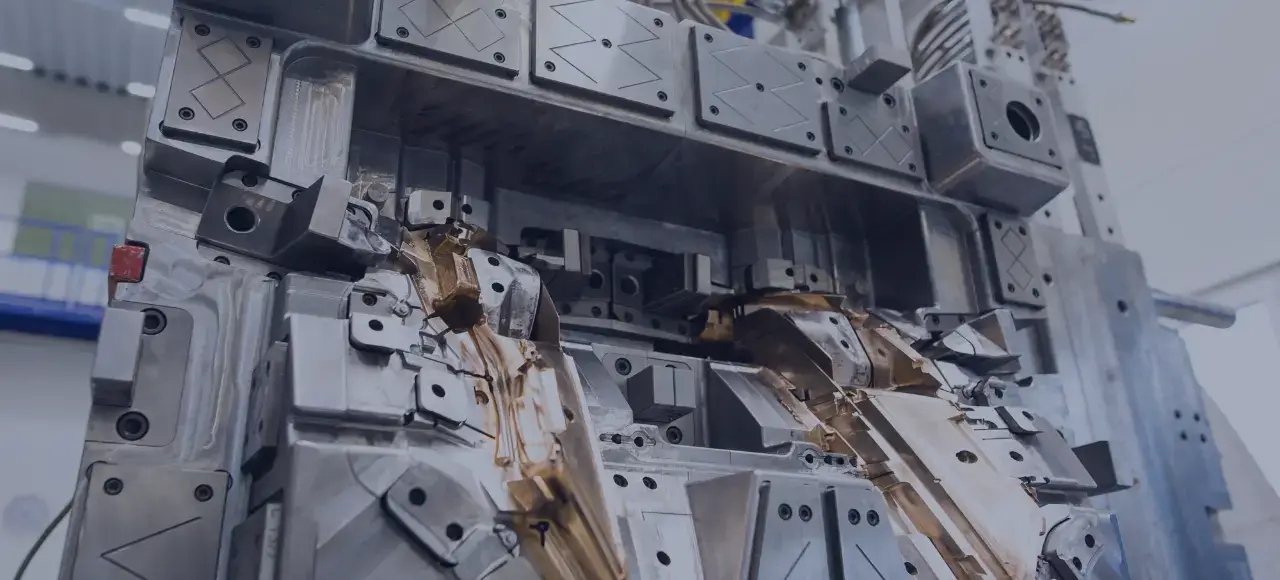
Quality Assurance in MIM
Ensuring the quality of MIM parts is crucial, mainly when they’re used in critical applications. Modern quality assurance techniques, such as X-ray fluorescence and computerized tomography scanning, are employed to inspect MIM parts. These non-destructive testing methods ensure that parts meet the required standards without causing any damage.
MIM vs. Traditional Manufacturing: A Comparative Analysis
While we’ve touched upon the metal injection molding advantages and disadvantages, a direct comparison with traditional manufacturing methods further highlights its strengths:
- Precision: MIM offers unparalleled accuracy, especially for intricate designs. Traditional methods, such as machining, might need help with such complexities.
- Economies of Scale: While the initial setup cost for MIM can be high, it becomes exceedingly cost-effective for large production runs.
- Material Efficiency: Traditional methods often involve subtractive processes, leading to material wastage. In contrast, MIM is an additive process, ensuring optimal material utilization.
Final Thoughts!
Metal injection molding is a testament to the manufacturing sector’s continuous evolution and drive for innovation. With its roots tracing back, MIM has grown exponentially in its capabilities, offering unparalleled precision and design flexibility. As we compared MIM with traditional manufacturing methods, its strengths in precision, economies of scale, and material efficiency became evident.
FAQs
MIM is a manufacturing technique that merges the principles of powdered metallurgy and plastic injection molding, allowing for producing metal parts with intricate designs.
MIM is compatible with a range of materials, including stainless steels, titanium, and specialty alloys, each chosen based on the properties of the final product.
MIM quality assurance employs modern techniques like X-ray fluorescence and computerized tomography scanning. These non-destructive methods ensure parts meet standards without causing damage.
The material determines the success of a MIM project. It affects the sintering process, the final part’s properties, and its suitability for the intended application. Hence, selecting suitable material is pivotal.